High carbon steel welding electrodes are a pivotal component in the metal fabrication industry, offering unparalleled strength and durability for various applications. These electrodes, characterized by their high carbon content, present unique challenges and rewards compared to their low carbon and mild steel counterparts. As an expert with substantial experience in metal fabrication and welding technologies, this piece aims to provide a comprehensive look into the use, selection, and nuances of high carbon steel welding electrodes, delivering insights that resonate with industry professionals.
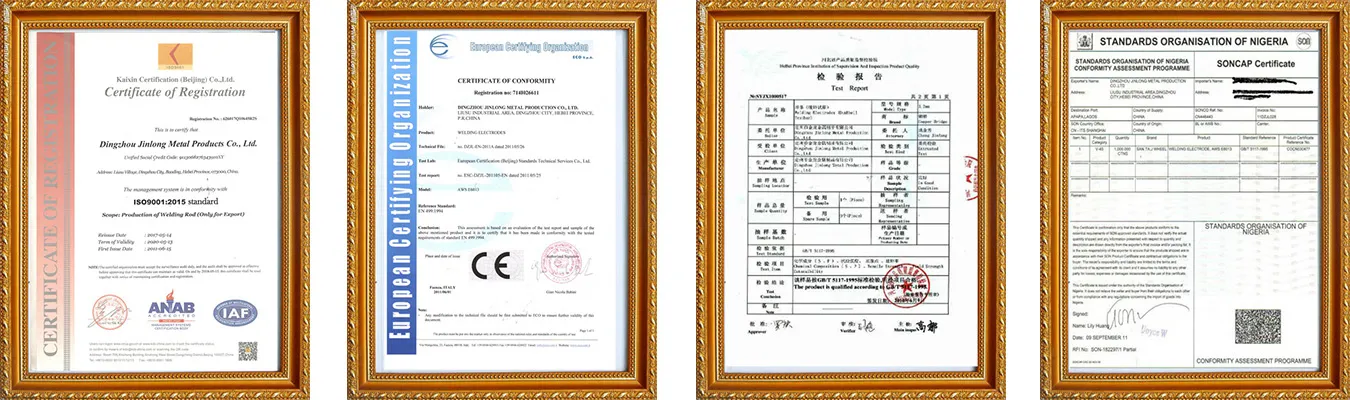
Understanding High Carbon Steel Electrodes
High carbon steel welding electrodes are designed for welding high carbon and alloy steels. These electrodes contain a substantial proportion of carbon, usually greater than 0.5%, making them suitable for projects that demand high tensile strength and rigidity. This characteristic makes them ideal for manufacturing cutting tools, automotive parts, and high-strength structural components.
Expertise in Application
When deploying high carbon steel welding electrodes, a deep understanding of welding dynamics is essential. The elevated carbon content can lead to challenges such as increased brittleness and susceptibility to cracking if not handled properly. Therefore, preheating the metal is a best practice that mitigates these risks by reducing thermal shock. Furthermore, post-weld heat treatment (PWHT) is often required to relieve stresses and ensure a robust metallurgical bond, emphasizing the need for professional expertise during the welding process.
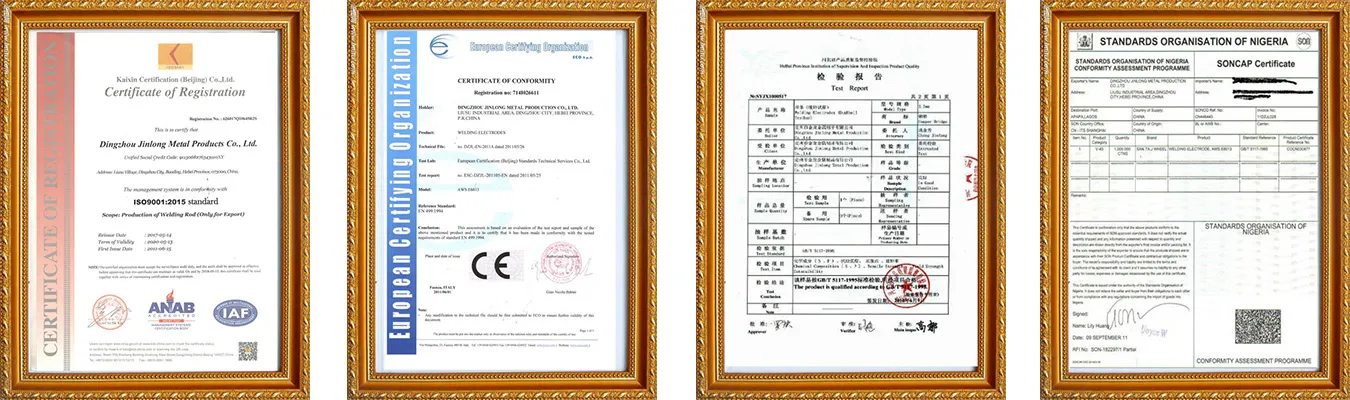
Selection Criteria
Choosing the right electrode involves evaluating factors such as the base material's carbon content, the anticipated load, and environmental conditions. Electrodes must match the mechanical properties of the base metal to achieve optimal performance. For instance, E10018-D2 electrodes might be selected for welding chrome-molybdenum steels due to their superior strength and ductility, which can withstand high-pressure applications. This selection process underscores the authority required when specifying electrodes for critical engineering projects.
high carbon steel welding electrodes
Trustworthiness in Quality Assurance
Ensuring the quality and reliability of welds with high carbon steel electrodes demands a commitment to rigorous standards and quality controls. Reputable manufacturers engage in thorough testing, such as impact and tensile tests, to certify that the electrodes meet industry standards like AWS, ISO, or DIN. Welding professionals often value electrodes from proven suppliers known for consistency and compliance with stringent quality benchmarks, thereby ensuring trustworthiness in every application.
Practical Experience with Challenges
Fieldwork experience reveals that dealing with high carbon steel welding frequently involves troubleshooting issues like hydrogen-induced cracking. Experts mitigate this by using low-hydrogen electrodes and maintaining controlled humidity levels to prevent moisture absorption. Moreover, achieving precise temperature management during and after welding has been proven vital in preventing weld failures. These insights reflect the depth of practical experience needed to excel in welding high carbon steel components.
In conclusion, high carbon steel welding electrodes are indispensable for projects needing exceptional strength and durability. Their application demands a high level of expertise, with careful attention towards electrode selection, preheat and post-weld treatments, and quality assurance practices. Industry professionals who possess both experience and a commitment to adhering to rigorous standards can effectively harness these electrodes' capabilities, reflecting a mastery over one of the most challenging yet rewarding aspects of metal fabrication.