Gas shielded welding wire, an essential component in modern welding processes, holds significance in producing durable, precise, and high-quality welds. Its relevance spans across various industries, including automotive, construction, and manufacturing, by providing superior shielding during the welding process.
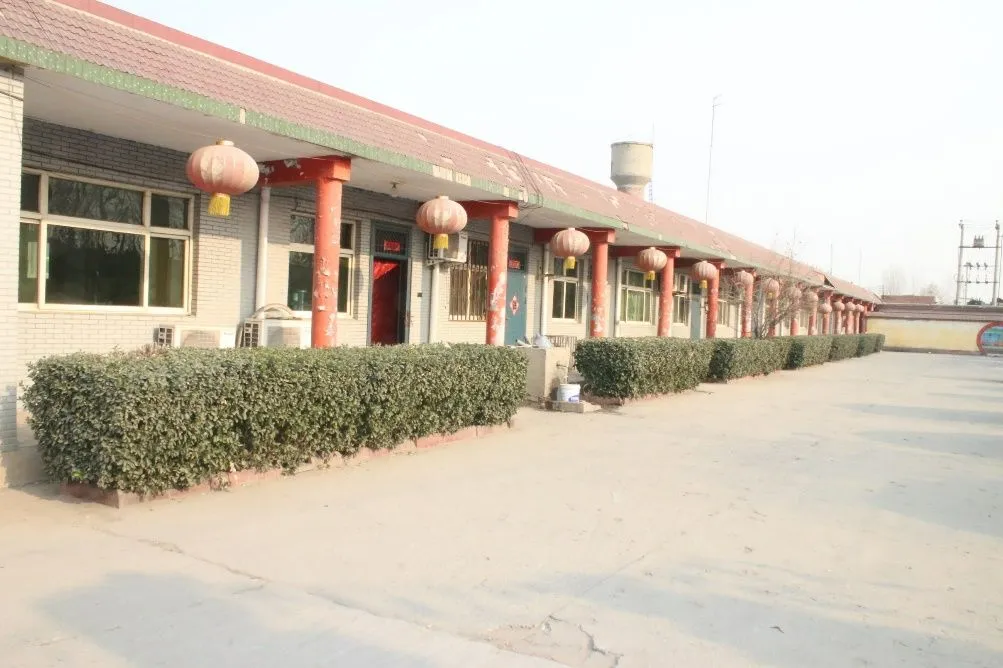
Gas shielded welding wires are typically used with MIG (Metal Inert Gas) and MAG (Metal Active Gas) welding processes. Unlike traditional welding methods that rely solely on a flux to protect the weld pool, gas shielded welding incorporates a shielding gas which actively protects the molten weld area from atmospheric contamination. This unique characteristic significantly enhances weld quality by reducing incidents of porosity and improving overall weld appearance and structural integrity.
When selecting a gas shielded welding wire, one of the primary considerations should be the base material to be welded. Common materials include carbon steel, stainless steel, and non-ferrous metals such as aluminum. Each type of base material requires a specific type of welding wire, designed to offer optimal compatibility and maintain mechanical properties of the welded joint. For carbon steel, ER70S-6 is a popular choice due to its high silicon and manganese content, which helps in deoxidizing the weld pool, resulting in excellent arc stability and enhanced bead appearance.
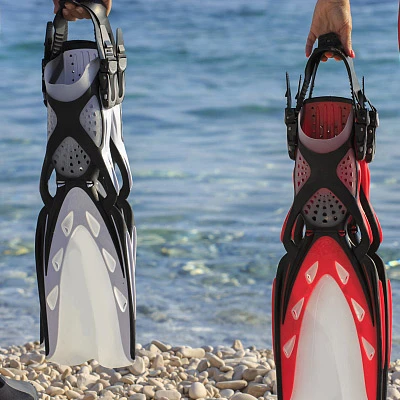
Stainless steel welding, on the other hand, demands wires like ER308L, notable for its low carbon content that minimizes carbide precipitation in the weld. This becomes crucial in maintaining corrosion resistance properties of the stainless steel, making it ideal for applications exposed to corrosive environments. Furthermore, for aluminum welding, wires such as ER4043 are commonly used; they are designed to deliver superior flow characteristics and minimize cracking in welds.
gas shielded welding wire
The choice of shielding gas is another crucial aspect of using gas shielded welding wire. Argon, often mixed with carbon dioxide or oxygen, is a popular choice due to its inert properties, which reduce oxidation during the welding process. For MIG welding, a mixture of argon with carbon dioxide in ratios like 75/25 or 90/10 is common for welding carbon and low-alloy steels, providing a good balance between arc stability, penetration, and spatter control. However, for materials like stainless steel, a tri-mix of argon, helium, and carbon dioxide can be employed to promote better heat input and improved weld pool fluidity.
Safety and handling are paramount when using gas shielded welding wires. Operators must ensure proper storage to prevent contamination from moisture and dust, which can adversely affect weld quality. Storing wires in a dry, temperature-controlled environment, typically in their original packaging, is recommended to prolong their usability and prevent quality degradation. Furthermore, operators must follow protective measures such as wearing appropriate personal protective equipment (PPE), ensuring proper ventilation, and adhering to all safety guidelines to mitigate health risks involved with exposure to welding fumes.
The economic implications of using gas shielded welding wire also warrant discussion. Despite a higher initial cost compared to other methods, the long-term benefits in terms of reduced post-weld cleanup, lower defect rates, and improved weld quality justify the investment. Achieving higher precision in welds translates into durability, which can significantly reduce maintenance costs and improve the lifespan of welded structures. Moreover, advancements in automation and robotics are further amplifying the efficiency and consistency of gas shielded welding processes, making it an increasingly viable option for industries looking to maximize productivity and quality.
In conclusion, gas shielded welding wire stands out as a cornerstone in achieving superior welding performance. Its continued evolution aligns with technological advancements and industry demands for higher efficiency, precision, and sustainability in welding operations. Being informed about the appropriate selection and use of welding wires, understanding the correlation with shielding gases, and adhering to best practices not only underscores the commitment to excellence but also secures a competitive edge in the industry. As industries continue to seek reliable and robust welding solutions, gas shielded welding wire remains at the forefront, symbolizing innovation and excellence in metal fabrication.