Flux coated stainless TIG wire represents a significant advancement in the world of welding, offering unparalleled efficiency and precision for numerous applications. This innovative product is designed to enhance the quality of welds while maintaining the integrity of stainless steel components. In a market where precision and reliability are paramount, flux coated stainless TIG wire emerges as a critical tool for welding professionals and industries that demand the highest standards of craftsmanship.
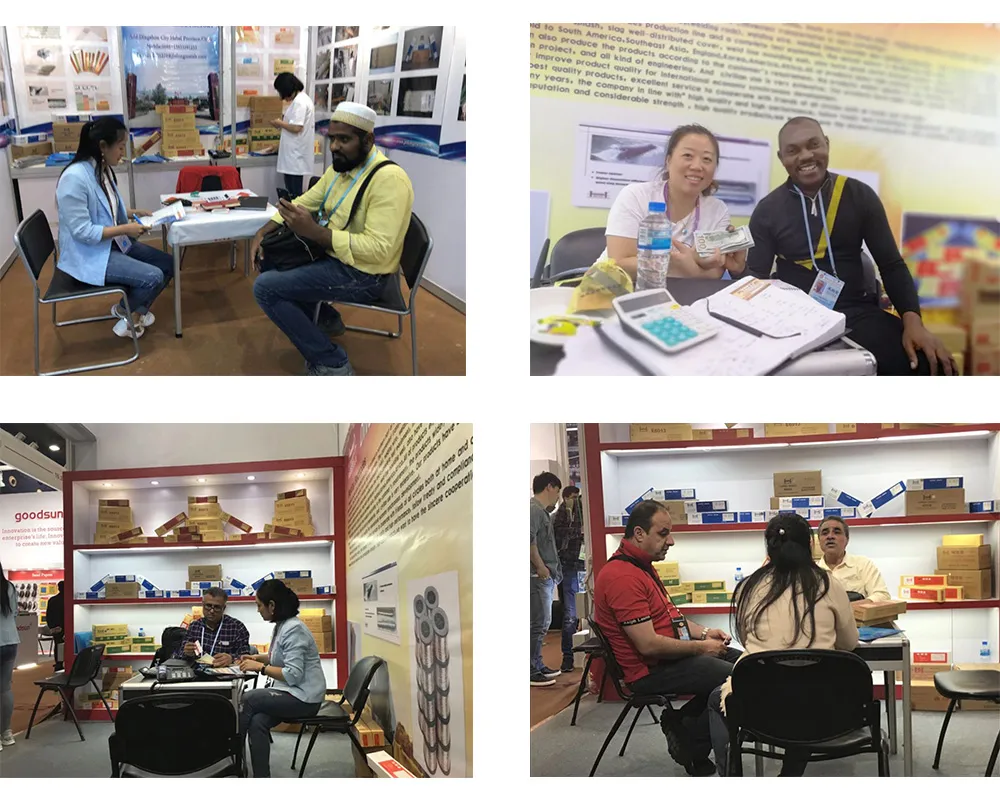
The primary advantage of flux coated stainless TIG wire lies in its ability to simplify the welding process while improving results. By incorporating a flux coating, this TIG wire eliminates the need for a separate shielding gas. This not only streamlines operations but also reduces costs and setup time. In environments where precision welding is crucial but access to gas cylinders is limited or impractical, flux coated TIG wire becomes an indispensable solution. Furthermore, the convenience of not requiring external gas makes it ideal for on-site repairs and maintenance, particularly in remote locations.
Welding professionals often encounter challenges related to contamination and oxidation, which can compromise the integrity and appearance of stainless steel welds. The flux coating on this TIG wire acts as a protective barrier, effectively minimizing these issues. It helps to prevent the intrusion of contaminants and protects the weld pool from atmospheric gases, ensuring a clean and smooth weld bead. This results in superior weld quality with reduced instances of defects, rework, or post-weld cleanup, ultimately saving time and resources.
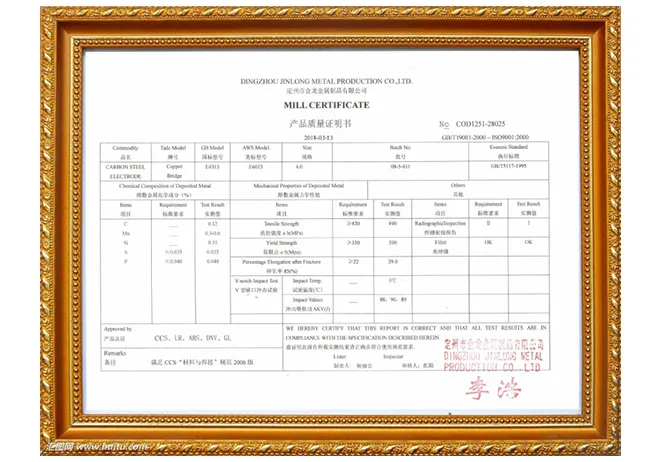
The performance of flux coated stainless TIG wire is underscored by its exceptional versatility. Suitable for a range of stainless steel alloys, it is particularly effective in joining thin materials where precision is critical. The wire’s adaptability across different welding positions—flat, horizontal, vertical, or overhead—adds to its practicality, enabling welders to tackle diverse projects with confidence. Moreover, its application in various industries, from food processing and pharmaceuticals to aerospace and petrochemicals, demonstrates its robustness and wide-ranging utility.
flux coated stainless tig wire
Addressing the aspect of expertise, the development and application of flux coated stainless TIG wire is backed by extensive research and rigorous testing. Manufacturers invest heavily in the development of these products to ensure compliance with industry standards and to fulfill specific customer requirements. Consequently, this wire is engineered to provide consistent arc stability and smooth feeding, contributing to its reliability and high-performance outcomes. As users adapt to this technology, they benefit from tailored training programs and comprehensive support, reinforcing the wire’s integration into their standard practices.
Authoritativeness is reinforced through the certifications and endorsements that flux coated stainless TIG wires often acquire. Recognized by welding organizations and regulatory bodies, these endorsements affirm the product’s capability and safety. Such accreditation provides welders and project managers with the assurance they need to specify this wire in critical applications without compromising quality or safety.
Trustworthiness is central to the adoption and continued use of flux coated stainless TIG wires. By delivering consistent performance and demonstrating resilience under demanding conditions, these wires earn the trust of welding professionals globally. Feedback from industry veterans emphasizes their satisfaction with the enhanced control and precision offered, further validating the wire’s role in achieving exacting standards in stainless steel welding.
In conclusion, flux coated stainless TIG wire is a transformative product in the welding arena, offering significant benefits related to efficiency, quality, and versatility. Through expert engineering and authoritative validation, it provides a trusted solution for challenging welding environments. Welding professionals seeking to enhance their craft and meet stringent industry demands will find in this product a reliable partner, capable of elevating their work to meet the highest standards of quality and performance.