TIG welding cast iron presents several challenges, predominantly due to the material's high carbon content and its tendency to crack during the cooling process. However, with the right filler rod and technique, achieving strong,
long-lasting welds on cast iron is entirely possible.
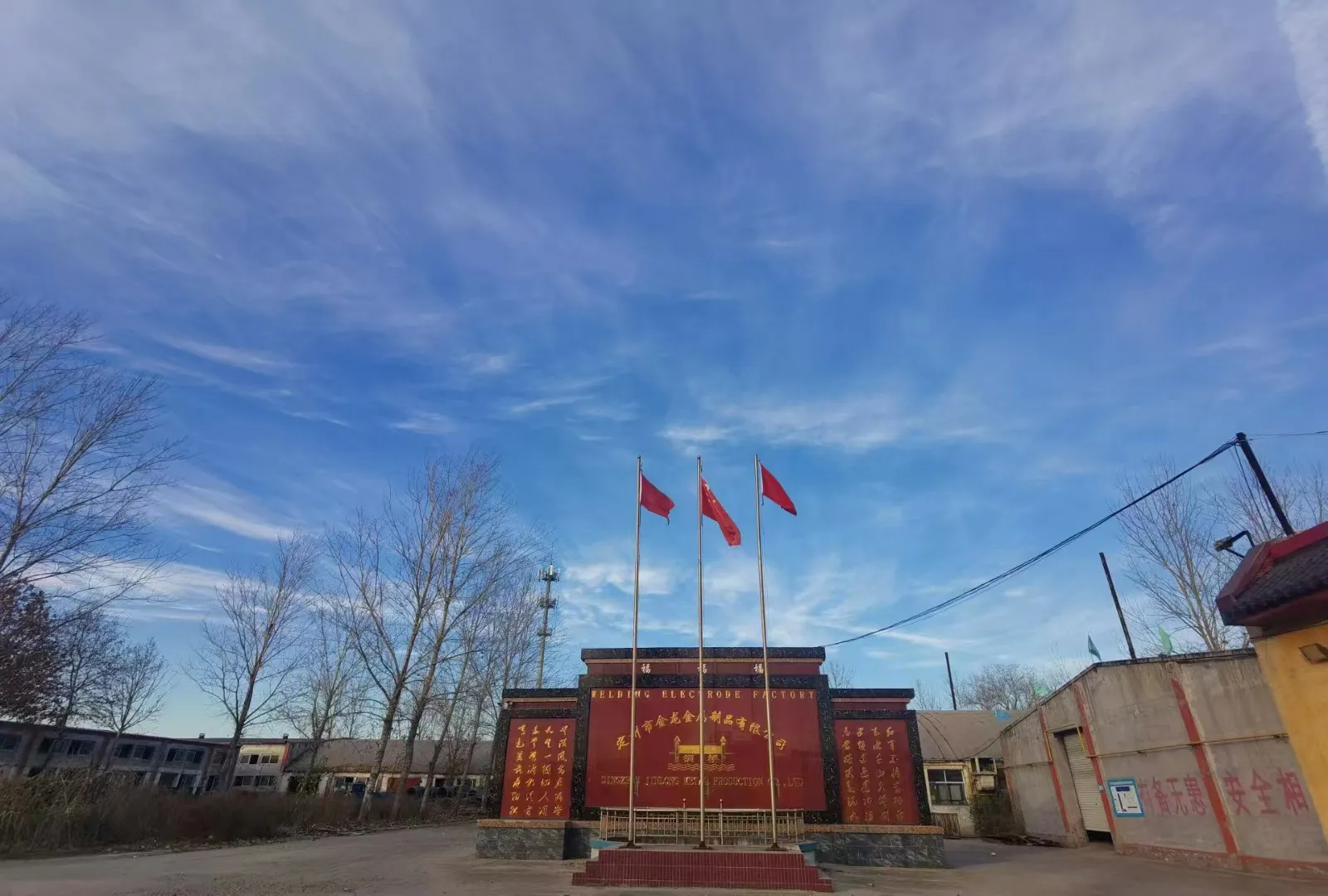
Selecting the appropriate filler rod is one of the critical factors in this process. A popular choice among professionals is the nickel-based filler rod, specifically the ERNiFe-CI and ERNi-CI rods. Nickel content is crucial because it offers significant benefits such as enhancing ductility and reducing the possibility of cracking. Nickel rods are compatible with a wide range of cast iron types, from grey to ductile iron, making them versatile for different projects.
The ERNiFe-CI rod is particularly noteworthy for its performance on alloy and non-alloyed cast iron. This filler rod is favored by experts because it mitigates the common issues associated with welding cast iron, such as post-weld chipping and cracking. Its composition allows for excellent fusion with the base metal, ensuring a robust bond that withstands stress and thermal variations. Additionally, the appearance of welds using this rod is aesthetically superior, which is a crucial factor in projects where the finish is visible.
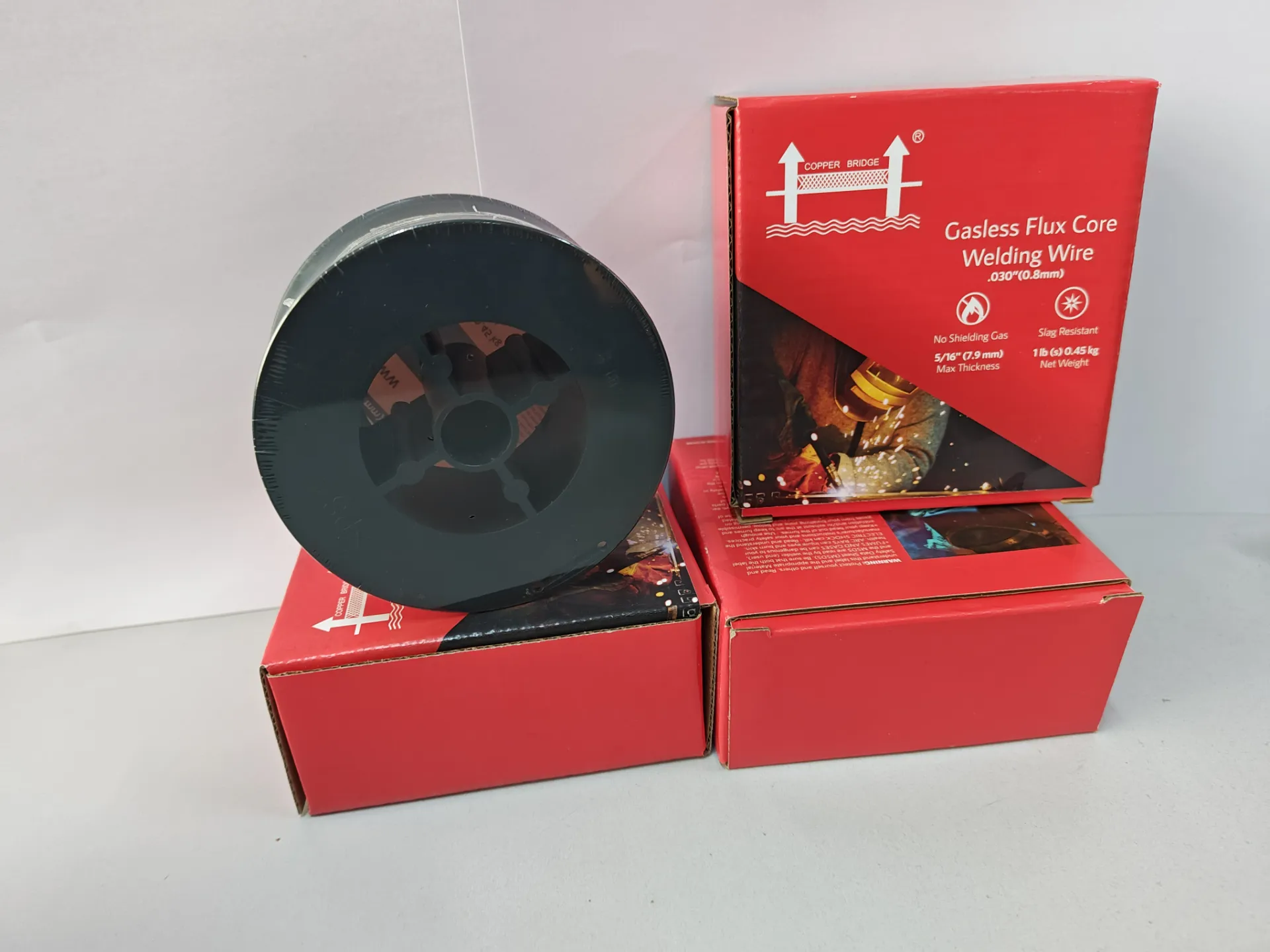
Before beginning the welding process, thorough preheating of the cast iron component is recommended. Experience dictates that heating the metal to temperatures between 500°F and 1200°F significantly diminishes the risk of cracking. The uniform heating of the component alleviates internal stresses, allowing the filler rod to meld seamlessly with the base material. After welding, a slow cooling process is essential to mitigate thermal shock and prevent any residual stress buildup.
filler rod for tig welding cast iron
The expertise involved in TIG welding cast iron extends beyond choosing the right filler rod. It requires an understanding of the welding environment and control over the welding speed and heat input. The welder's skill in maintaining a consistent arc length and their ability to adaptively respond to the molten pool's behavior significantly impact the final outcome. Professionals recommend maintaining a short arc length and avoiding excessive heat that can lead to overheating and subsequent issues.
Authoritative advice from seasoned welders also highlights the importance of meticulous cleaning prior to welding. Ensuring that the cast iron surface is free from contaminants such as oil, rust, and previous coatings can prevent the incorporation of impurities into the weld bond. Proper cleaning methods include the use of wire brushing and non-residual cleaning solvents designed specifically for cast iron processes.
Trustworthiness in the welding procedure can be bolstered through regular testing and quality checks. Adopting non-destructive testing methods such as ultrasonic testing or dye penetrant testing can validate the integrity of the weld without damaging the component. This is particularly important in applications where the reliability of the weld is crucial for functionality and safety.
In conclusion, TIG welding cast iron requires a blend of the right materials, careful preparation, and skilled application. The correct use of high-quality nickel-based filler rods such as ERNiFe-CI not only addresses the inherent challenges of welding cast iron but also offers a pragmatic solution for achieving durable, high-quality welds. By adhering to best practice welding techniques, regularly assessing the quality through strategic testing, and continuously expanding knowledge and expertise, welders can master the intricacies of TIG welding cast iron. Such dedication to the craft ensures that they deliver successful outcomes that meet, and often exceed, industry standards.