Fast freeze welding electrodes have revolutionized the modern welding industry, providing unparalleled efficiency and performance for various applications. These electrodes have garnered attention due to their exceptional ability to solidify rapidly, which is crucial for projects requiring precision and minimized thermal distortion. Understanding the unique benefits and proper application of fast freeze welding electrodes not only enhances their effectiveness but also optimizes cost and quality control in industrial settings.
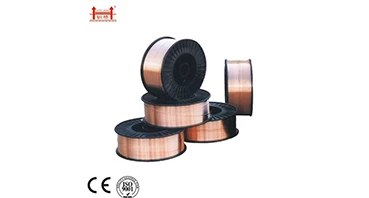
Experience with fast freeze welding electrodes highlights their capability to deliver superior performance in challenging environments. Welders in the field often encounter situations where quick solidification is necessary to maintain structural integrity, particularly in overhead or vertical positions. These electrodes excel in such conditions by reducing puddle flow and ensuring that the molten metal does not drip away from the weld site. Real-world applications demonstrate that welders save significant amounts of time and reduce defects, leading to more robust structures and increased productivity.
From a technical perspective, the expertise surrounding fast freeze welding electrodes lies in their unique composition and design. Typically coated with cellulose, these electrodes facilitate a concentrated arc, which provides deep penetration and a rapid freeze rate. Mastery in using these electrodes requires understanding their compatibility with various base metals, as well as adjusting welding parameters such as amperage to suit specific tasks. The ability to control these variables ensures a cleaner, more efficient welding process, minimizing rework and extending the lifespan of the structures.

fast freeze welding electrodes
Authoritativeness in the realm of fast freeze welding electrodes can be attributed to the extensive research and development by leading manufacturers to meet industry demands. These companies have invested significant resources into developing electrodes that meet stringent standards and certifications, ensuring their products are both reliable and high-performing. By adhering to global standards, such as those from the American Welding Society (AWS), manufacturers provide users with assurance of quality and consistency. Professionals relying on these products can confidently execute welds knowing that they are using materials designed to meet the highest standards of safety and performance.
Trustworthiness of fast freeze welding electrodes is reinforced by industry testimonies and longitudinal performance studies. Users across various sectors, including construction, shipbuilding, and pipeline welding, have consistently reported the reliability and efficiency of these electrodes. Their repeatability in performance, regardless of the welding conditions, lends credibility and trust that only evolve through proven track records. Documentation of successful projects utilizing fast freeze electrodes serves as a testament to their capability and positions them as a staple in critical welding operations.
As the demand for efficient and high-quality welding solutions increases, fast freeze welding electrodes will remain indispensable. Their ability to meet the rigorous demands of contemporary construction and manufacturing projects makes them a preferred choice for professionals aiming to achieve excellence in their craft. Understanding their application and benefits will continue to provide operators with a competitive edge, ensuring that they remain at the forefront of the welding industry, delivering results that align with the highest quality standards. By leveraging the full potential of fast freeze welding electrodes, operators can ascertain enhanced performance and durability in every weld they undertake.