In the ever-evolving world of welding, the ER7018 electrode stands out as a crucial component, embodying reliability and excellence in the realm of arc welding. For professional welders aiming to achieve precision and strength in their work, understanding the intricacies of this electrode is paramount. This piece delves into the unique attributes and practical applications of the ER7018 electrode, offering insights grounded in expert knowledge and authentic experiences.
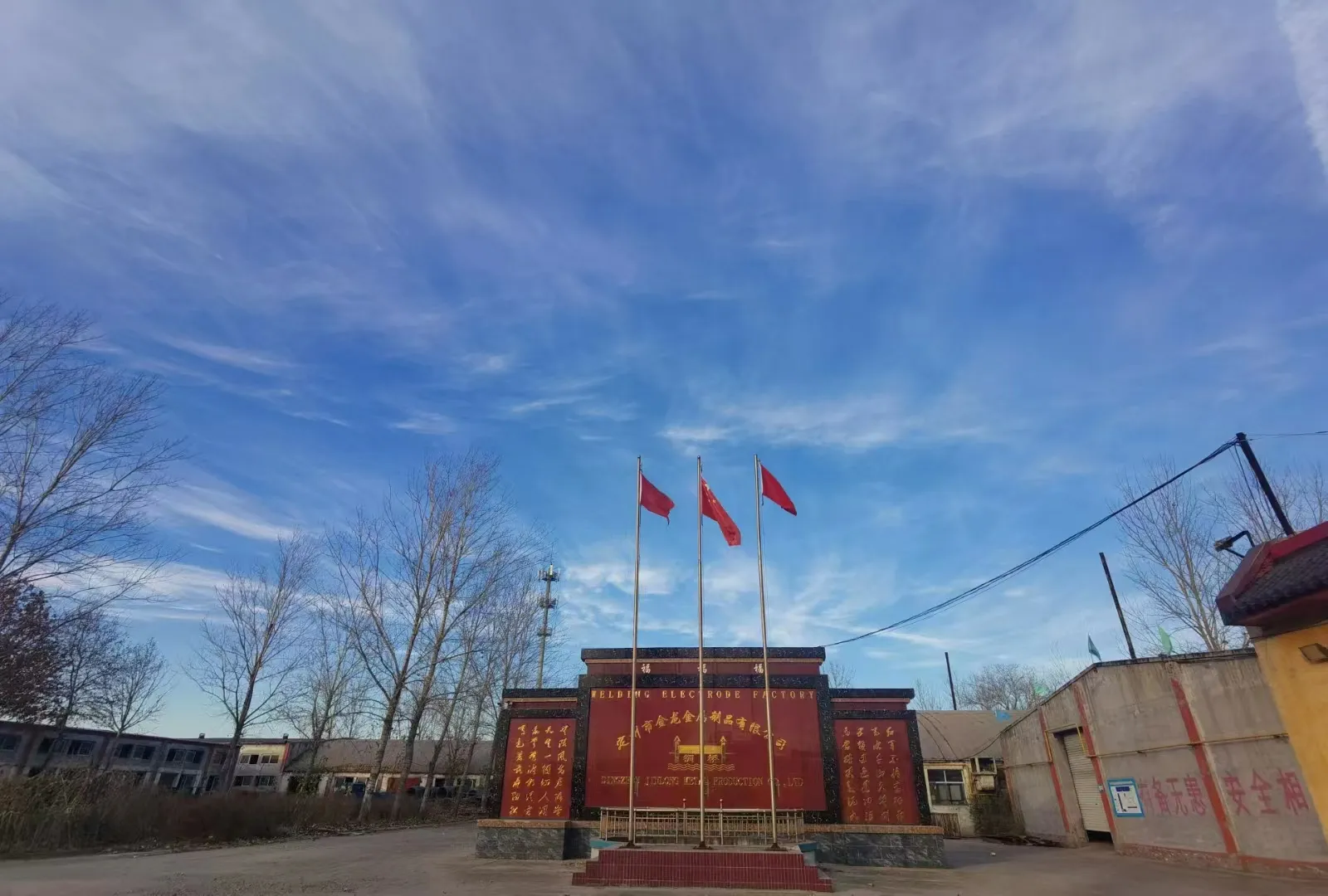
The ER7018 electrode, often revered in the welding industry, is distinguished by its low-hydrogen iron powder coating, which grants it superior crack-resistance and high deposition rates. It is typically used for welding carbon steel and low alloy steel, making it perfect for tasks that demand robustness and durability, such as constructing steel structures, ships, bridges, and storage tanks. With a tensile strength rating of 70,000 psi, it establishes itself as a dependable choice for welds subjected to demanding conditions.
One of the defining features of the ER7018 electrode is its ability to produce smooth, spatter-free welds. This attribute can be attributed to its chemical composition and coating, which ensure an arc that is stable and easy to control. For welders, especially those working on intricate or lengthy projects, the ER7018 provides not just effectiveness but also efficiency, reducing the time spent on post-weld cleaning and enhancing overall productivity.
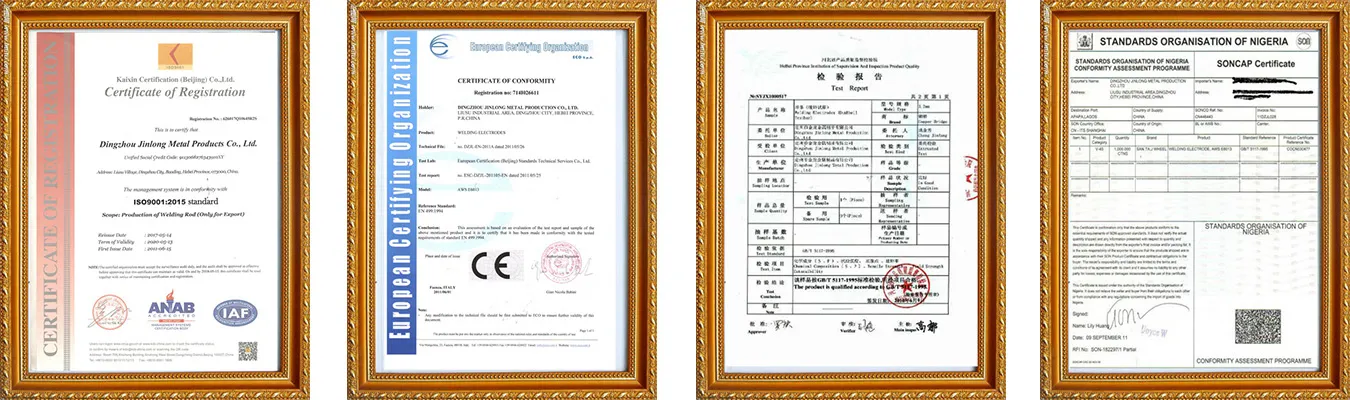
Multiple years of experience in fieldwork highlight a critical advantage of the ER7018 its versatility across various positions and environments. Whether working vertically, horizontally, or overhead, this electrode consistently delivers reliable results. This positional versatility minimizes the need for electing different electrodes for various parts of a project, streamlining the workflow and cutting costs without sacrificing quality.
From a professional standpoint, the expertise required to maximize the benefits of the ER7018 electrode cannot be overstated. Before initiating any project, welders should ensure proper storage to prevent exposure to moisture, which could compromise the electrode's performance by increasing hydrogen content. Additionally, welding procedures involving this electrode mandate precise control over parameters such as amperage settings to mitigate risks of defects like porosity or inadequate fusion.
er7018 electrode
In complex manufacturing environments, the decision to employ ER7018 electrodes is often underscored by its reputation for trustworthiness. Industry certifications affirm its compliance with stringent standards, offering assurance that it will meet or exceed performance expectations. This is particularly vital in sectors where weld integrity directly impacts safety and structural integrity.
Technical community forums are replete with testimonials from seasoned professionals who vouch for the ER7018’s unparalleled reliability. Many have recounted instances where this electrode's superior performance under harsh conditions translated into fewer callbacks and greater satisfaction for end clients. This trustworthiness stems from its proven track record of consistent results.
Despite its many strengths,
the use of ER7018 electrodes demands adherence to best practices. Welding experts recommend regular training to refine the skills necessary for working with this electrode type, as well as ongoing education regarding new welding technologies and methodologies.
In summary, the ER7018 electrode embodies a balance of expertise and practicality, making it a staple for many in the welding industry. Its unique composition and design facilitate exceptional weld quality, positioning it as an authoritative choice for critical applications across various sectors. As industries continue to evolve, embracing innovative materials and techniques, the foundational application of reliable tools like the ER7018 will invariably remain central to achieving excellence in welding.