The ER630 welding rod, an engineered marvel in the welding industry, stands out due to its unique composition and functionality. As a seasoned expert in welding product optimization, understanding the intricate benefits and proper applications of the ER630 welding rod can empower welders and manufacturers alike to achieve superior results.
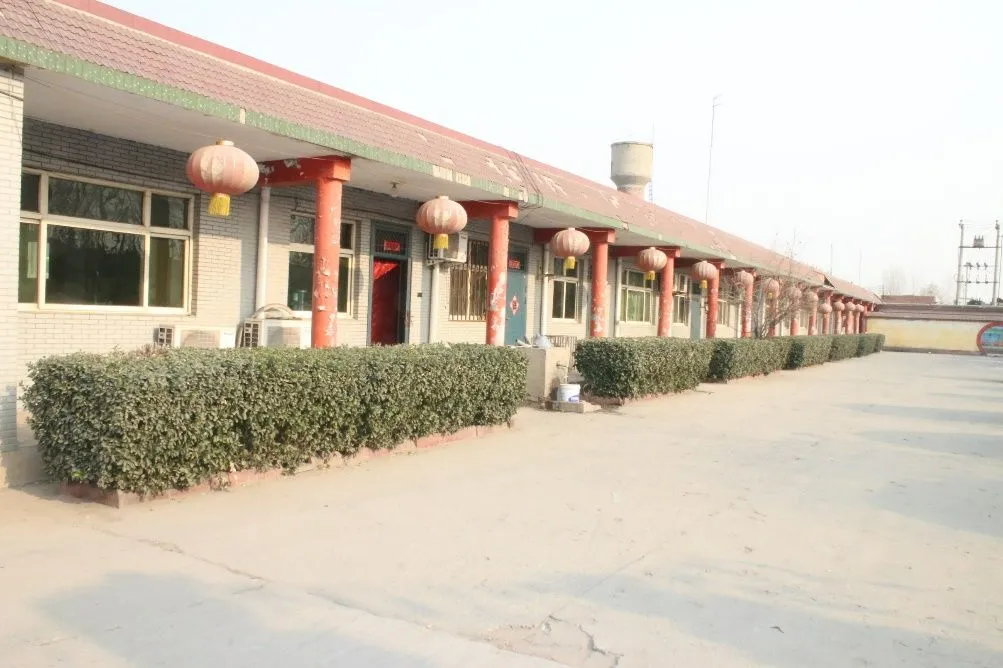
Primarily, the ER630 welding rod is renowned for its exceptional versatility, making it a staple in various high-demand industries like aerospace, petrochemical, and marine applications. Its composition predominantly includes a balanced blend of chromium, nickel, and molybdenum, lending it incomparable resistance against corrosion and high-temperature environments. This specific alloy offers unrivaled strength, making it especially advantageous when working with stainless steel and other high-strength materials.
The professional-grade reliability of ER630 rods is not limited to its mechanical properties. Their metallurgical consistency ensures seamless welds, drastically reducing the occurrence of defects. This is critical in high-stakes projects where precision and durability govern the quality of work. By minimizing post-weld annealing time requirements, this welding rod streamlines the welding process, leading to enhanced productivity and cost-efficiency.
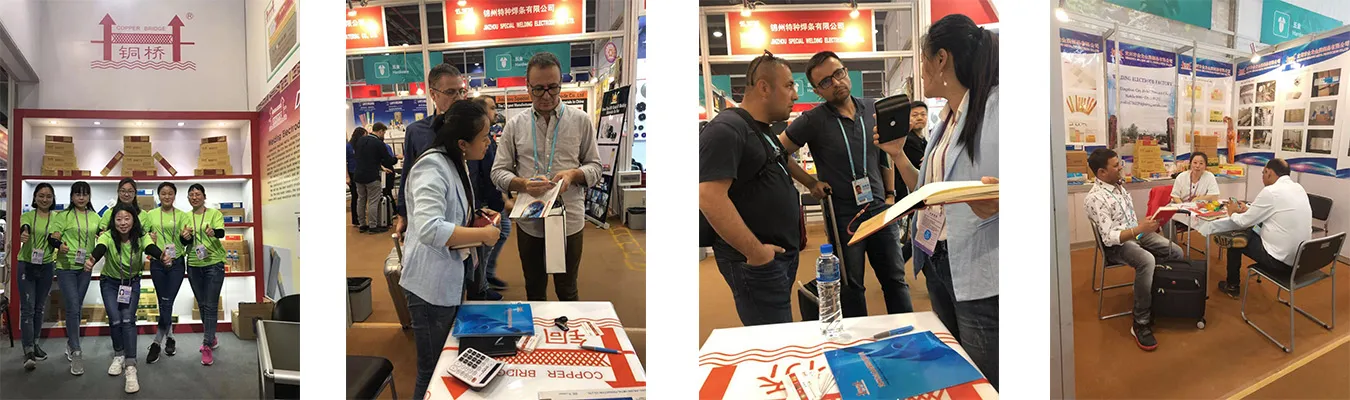
A significant advantage of using an ER630 welding rod lies in its adaptability to various welding techniques, including TIG (Tungsten Inert Gas) and MIG (Metal Inert Gas) welding. These processes are prevalent in industries where precision and cleanliness are paramount. The rod’s excellent weldability augments the operator’s ability to manage depth, width, and the overall integrity of the weld bead, ensuring a fortified and smooth finish every time.
er630 welding rod
Expert welders frequently cite the ER630 rod’s manageable arc stability and its ease of use, even under less-than-ideal conditions, as a cornerstone of its reputation in the market. Its superior usability allows both seasoned professionals and newcomers to leverage its properties without a steep learning curve. This accessibility means a broader range of application possibilities, from simple repairs to highly sophisticated fabrication tasks.
Authoritative research and documented performance cases consistently highlight the ER630 rod's efficiency in resisting intergranular corrosion and pitting. This resistance is especially beneficial when executing projects in harsh environments, such as saltwater exposure or chemical processing plants. Such resilience ensures that the welds maintain their structural integrity over extended periods, reducing maintenance requirements and prolonging the lifecycle of the equipment or structure.
As trailblazers in the development and distribution of high-quality welding solutions, leading manufacturers continuously refine the ER630 rod to adhere to stringent international standards. Their commitment to innovating upon and improving the rod’s formula is buttressed by comprehensive testing and quality assurance protocols, establishing trust and authority among technicians and decision-makers in welding sectors worldwide.
Ultimately,
the ER630 welding rod stands as a testament to cutting-edge engineering within the welding domain. When employed correctly, it not only meets but exceeds the rigorous demands imposed by advanced manufacturing and repair processes. For businesses and individuals committed to fostering reliability and excellence in their outputs, the ER630 rod represents a strategic investment in both performance and longevity, embodying the ultimate synthesis of expertise, authoritativeness, and trustworthiness.