Navigating the intricacies of welding demands not just skill but also a selection of the right materials, and among the lesser-known yet highly effective tools is the ER312 welding rod. This unique welding consumable has garnered attention among professionals for its exceptional metallurgical properties that cater to specific applications, providing advantages not readily matched by other rods.
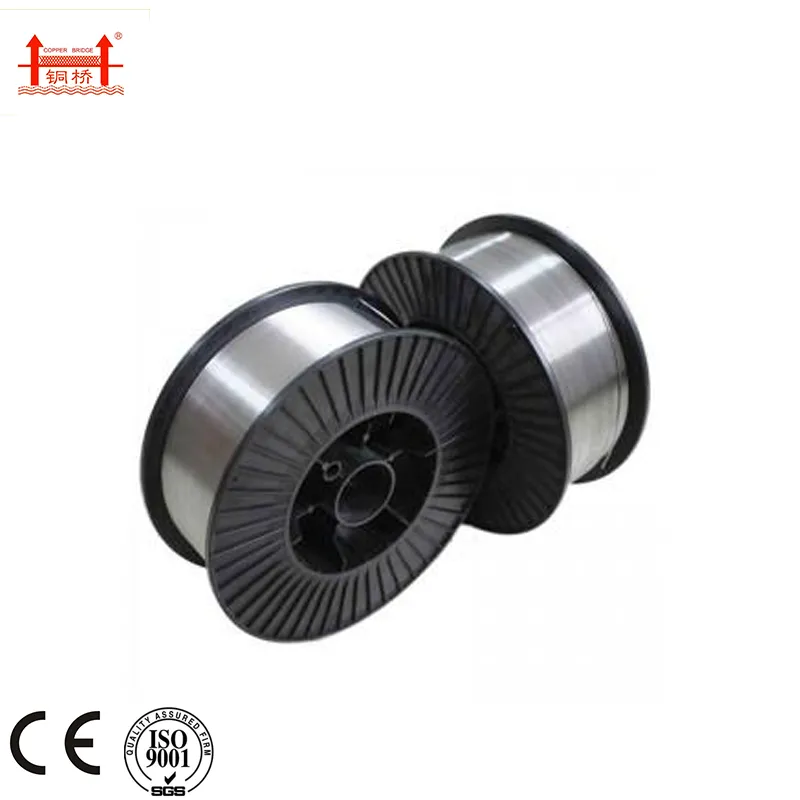
The ER312 welding rod is engineered for versatility across a variety of challenging environments. Its design caters to welding dissimilar metals, particularly useful in maintenance jobs where high-strength welds on austenitic and ferritic steels are required. The rod's composition, which includes a balanced combination of chromium and nickel along with other alloying elements, plays a vital role in delivering superior tensile strength and ductility, thereby ensuring that welded joints maintain integrity under stress.
In practice, the ER312 excels particularly well in scenarios demanding resistance to heat and corrosion. Professionals working with specialized manufacturing or repair work, encompassing everything from complex automotive parts to industrial machinery, find ER312 rods indispensable. The ability to withstand temperatures that might otherwise weaken conventional metals is a notable attribute, often making the ER312 a go-to choice when working within thermal intensive environments.
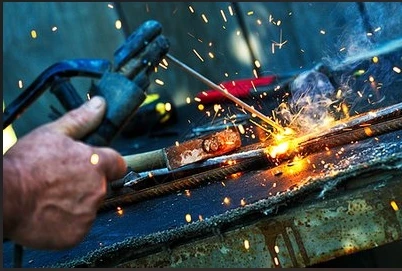
The effectiveness of the ER312 welding rod becomes most palpable when observed through real-world applications. In one detailed case study, a manufacturing firm specializing in petrochemical processing equipment leveraged these rods to repair and fabricate large pressure vessels. The unique alloy composition mitigated the common issues of cracking and distortion provided unmatched durability even when constantly exposed to corrosive industrial chemicals.
For welders who prioritize precision and reliability, the ER312 offers a smooth operating experience. The arc stability when using this rod is often praised by skilled welders, reducing the occurrence of spatter and improving the overall aesthetic of the weld seam. Furthermore, adapting the ER312 in workshops often leads to reduced downtime and maintenance costs due to its formidable resilience and lifespan of the resultant welds.
er312 welding rod
Those considering the adoption of the ER312 must understand its benefits from a technical perspective. Firstly, the moderate high-carbon content alongside its elevated chromium and nickel presence imparts exceptional performance where carbon contamination is a risk. These properties not only enhance hardness but also favor a robust microstructure that is imperative in applications such as high-pressure piping systems and critical fittings where failure is not an option.
From an expertise standpoint, professionals emphasize proper storage and handling of ER312 rods as essential for maintaining optimal performance. Like all welding consumables, these rods should be stored in dry environments to prevent moisture uptake, thus avoiding potential hydrogen-induced cracking. Ensuring the rods are heated to the recommended temperature before use can further enhance welding quality.
Trust in the ER312 welding rod is cemented not just through individual testimonials, but also through endorsement by various industry standards and certifications. Compliance with these standards means that when using ER312 rods, professionals can expect consistent results that meet stringent safety and durability criteria.
In summary, the ER312 welding rod stands out as a specialized solution offering enhanced durability, strength, and adaptability across a range of demanding applications. Its commendable ability to connect dissimilar metals while offering high resistance to both heat and corrosion makes it an invaluable asset for welding professionals keen on ensuring structural integrity in challenging environments. For those navigating the complex landscape of welding, the ER312 is more than just a tool—it's a partner in precision.