Mastering the art of welding with enicl 99 nickel cast iron electrodes requires a profound understanding of both the material properties and techniques needed to achieve optimal results. As industries continuously seek advanced solutions for repairing and joining cast iron components, this specific electrode has proven to be indispensable. Here, we delve into the practicality, advantages, and technical nuances of using enicl 99 nickel cast iron welding electrodes, drawing upon real-life experiences and authoritative insights to provide a comprehensive guide that enhances knowledge and trustworthiness.
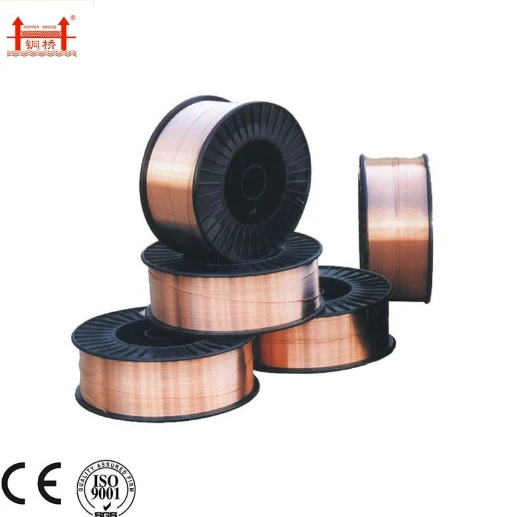
Enicl 99 nickel cast iron welding electrodes are renowned for their superior performance in welding cast iron, a material that is notoriously difficult to work with due to its brittleness and high carbon content. In applications ranging from repairing heavy machinery to restoring historical structures, these electrodes provide the flexibility and reliability necessary to ensure durability and strength.
One of the primary advantages of enicl 99 is its high nickel content, which offers excellent machinability and reduces the risk of cracking. Nickel's inherent properties help to accommodate the expansion and contraction stresses that occur during the heating and cooling cycles of the welding process. This makes it particularly advantageous for tackling jobs requiring precision and resilience, especially in sectors such as automotive repair and maintenance, where cast iron engine blocks frequently need refurbishing.
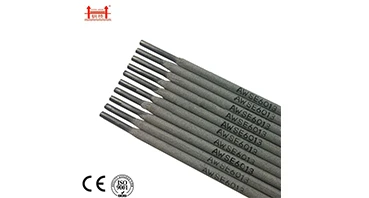
Expert welders have consistently praised the smooth arc characteristics and low penetration of these electrodes, which contribute to minimizing distortion in delicate cast iron pieces. Unlike other types of electrodes that might compromise the integrity of the metal, enicl 99 offers a unique balance that aligns with the thermal and mechanical properties of cast iron, ensuring that the welded joints remain robust over time.
When exploring the technical application of enicl 99 nickel electrodes, it becomes evident that pre-weld and post-weld procedures are just as critical as the welding itself. Preheating the cast iron is often recommended to reduce thermal shock and further prevent cracking. Experts suggest a targeted temperature of approximately 250°F to ensure uniform heat distribution. Following the welding process, a slow and controlled cooling phase is essential. This can be achieved by wrapping the welded component in heat-retentive materials such as thermal blankets to gradually bring the temperature down, avoiding abrupt changes that might induce stress.
enicl 99 nickel cast iron welding electrode
Industry professionals have also identified that correct electrode storage is vital for maintaining performance standards. Moisture can significantly affect welding outcomes; hence, storing electrodes in a dry environment or, optimally, in a rod oven set to prescribed temperatures, ensures their quality is retained.
To ensure you maximize the benefits of enicl 99 nickel cast iron welding electrodes, it is crucial to select the appropriate diameter for your specific application. Thinner electrodes might be suitable for intricate work requiring minimal welding material, while thicker electrodes offer expedited coverage for larger projects. Proper electrode manipulation, such as a weave bead technique, further enhances joint strength and finish quality, adhering to the meticulous standards demanded by both structural integrity and aesthetic considerations.
Testimonies from leading workshops emphasize that integrating enicl 99 into their toolkit has not only improved repair success rates but also extended the lifespan of the components they service. The adaptability and performance of these electrodes have been pivotal in reducing downtime, a critical factor in maintaining industrial productivity and client satisfaction.
In conclusion, utilizing enicl 99 nickel cast iron welding electrodes requires a strategic approach that combines technical expertise with practical experience. By adhering to best practices, from electrode storage to controlled cooling techniques, welders can achieve superior results, minimizing potential challenges associated with welding cast iron. Embracing these electrodes not only enhances operational efficiency but also affirms the commitment to high-quality workmanship, underscoring the trust placed in the welding professionals who use them.