Selecting the Right Electrode for Stainless Steel Welding A Comprehensive Guide
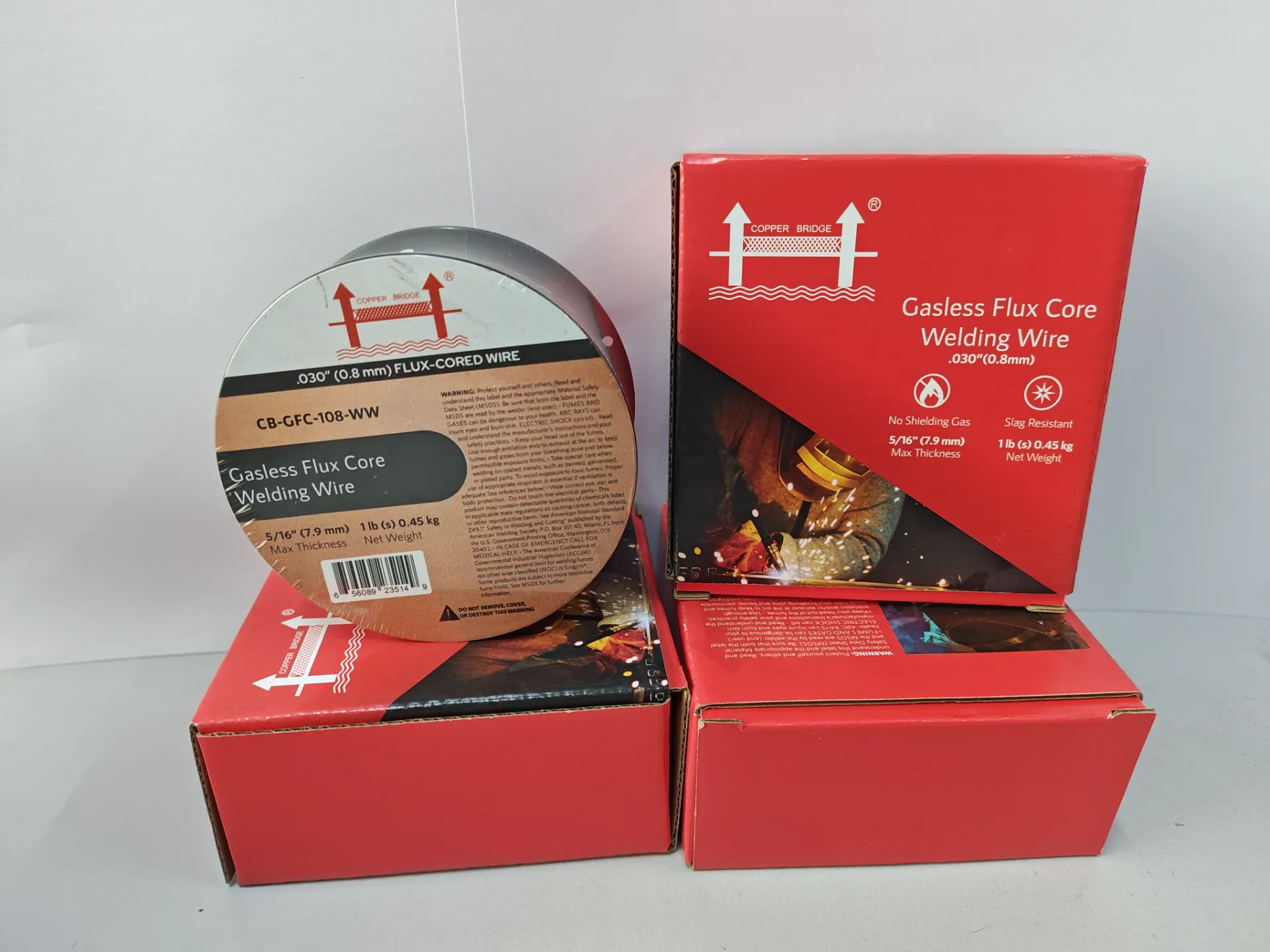
The art of stainless steel welding is intricate, requiring not only a steady hand but also a thorough understanding of materials and equipment. At the core of this process lies the choice of electrode, a factor that can significantly affect the outcome of your welding project. Electrode selection can influence weld quality, mechanical properties, and even the aesthetics of the final product. This article delves into the nuances of electrode selection for stainless steel welding, ensuring that your next project is both seamless and satisfactory.
A critical factor in electrode selection is the composition of the stainless steel. Stainless steels are classified into various groups, including austenitic, ferritic, and martensitic, each with specific properties and applications. For instance, austenitic stainless steel, represented by grades like 304 or 316, is commonly used for its corrosion resistance and excellent formability. When working with such materials, electrodes labeled as E308 or E316 are often recommended due to their similar composition, ensuring compatibility and corrosion resistance in the weld zone.
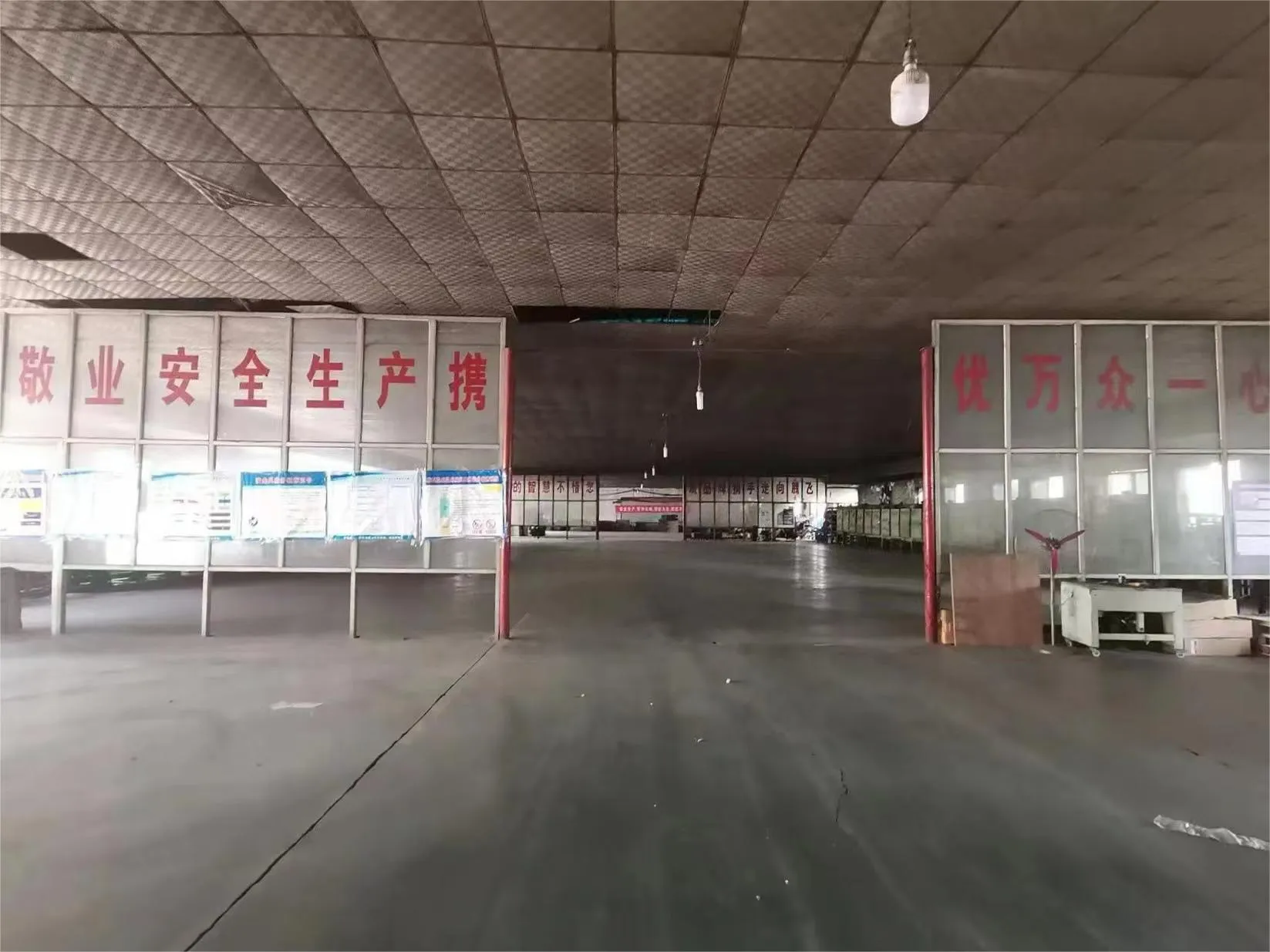
Ferritic stainless steels, on the other hand, require a different approach. They are less ductile but offer excellent resistance to stress corrosion cracking. Thus, electrodes such as E430 are ideal, enhancing the weld's mechanical resilience without compromising its integrity. For martensitic stainless steels, known for their high hardness and strength, electrodes like E410 or E420 are preferred. These ensure a robust weld that retains the desired mechanical properties, essential for applications subjected to high stress and wear.
The welding position—whether flat, horizontal, vertical, or overhead—also impacts electrode choice. Certain electrodes are designed specifically for positional work, offering easy operation and strong slag covering to protect the molten weld pool. It's advisable to select a versatile electrode that performs well across all positions to maintain consistent quality and reduce the likelihood of defects.
Furthermore, the welding technique employed—TIG, MIG, or manual metal arc welding—dictates specific electrode needs. TIG welding, for instance, leverages a non-consumable tungsten electrode that does not require replacement in the same way consumable electrodes do. This method is celebrated for producing high-quality,
precise welds. In contrast, manual metal arc welding involves consumable electrodes that must match the base material to ensure a cohesive bond and desirable weld characteristics.
electrode for ss welding
The choice also extends to considering the welding environment, such as wind conditions or the presence of contaminants. For outdoor projects or environments with variable conditions, using an electrode with a heavy flux coating can be advantageous, offering better shielding from atmospheric contaminants and minimizing the risk of porosity.
Beyond technical specifications, understanding real-world customer experiences with specific electrodes can provide invaluable insights. Users consistently emphasize the importance of ease of use, minimal spatter, and the ability to produce aesthetically pleasing beads. Brands that invest in R&D to improve these qualities often receive higher satisfaction ratings from professional welders and hobbyists alike.
For those seeking authoritative guidance, consulting manufacturers’ datasheets and adhering to professional welding standards is crucial. These resources provide detailed information on the appropriate applications, strengths, and limitations of different electrodes, supporting informed decision-making.
Trust in electrode selection also stems from authenticity and proof of performance. Brands that provide certifications or third-party endorsements foster greater trust among users, establishing a reputation for reliability and excellence.
Conclusively, selecting the appropriate electrode for stainless steel welding requires an intersection of theoretical knowledge, practical experience, and a keen awareness of project-specific needs. Whether you are tackling a complex industrial project or a simple DIY task, the right electrode ensures not only a successful outcome but also longevity and satisfaction. By understanding the subtleties of materials, positions, and welding methods, you empower yourself to make choices that advance your craftsmanship and deliver superior results.