The versatility and reliability of the E7018 electrode make it a staple in the welding industry, renowned for its unique characteristics that cater to both industrial and personal projects. This electrode stands out primarily due to its low hydrogen content, which effectively minimizes the risk of cracking—a crucial advantage that enhances the structural integrity of welded joints.
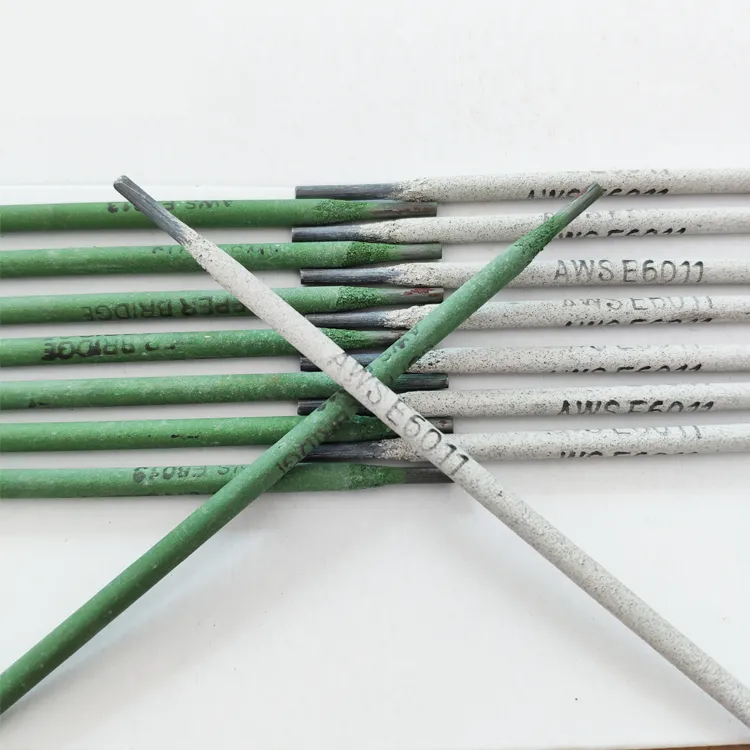
One of the defining features of the E7018 electrode is its iron powder coating. This coating is not merely an aesthetic feature but a technological enhancement that facilitates a stable arc and ensures a consistent deposition rate. The resultant welds are not only aesthetically pleasing but also structurally sound, owing to the efficient slag removal process that accompanies this electrode.
For those immersed in construction or heavy machinery manufacturing, the E7018's commendable tensile strength proves indispensable. With a tensile strength of 70,000 psi, it guarantees durability and strength, making it particularly suitable for high-stress applications. This strength, combined with its ductility, enables it to withstand significant stress and strain, ensuring longevity and resilience in demanding environments.
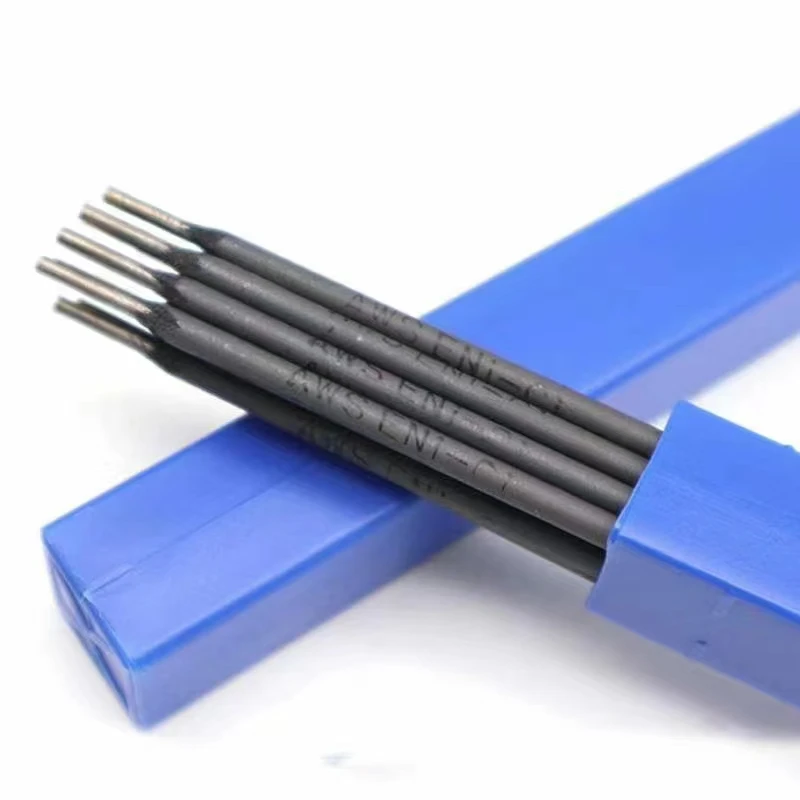
The electrode's performance is further amplified by its capability to perform well in all-position welding. Whether welding flat, vertical, horizontal, or overhead, the E7018 delivers impeccable results, allowing welders the flexibility to tackle a diverse array of projects with precision. This attribute is particularly beneficial in complex and multifaceted construction projects where varied welding positions are inevitable.
Another laudable aspect of the E7018 electrode is its user-friendly nature. The electrode's forgiving arc characteristic is particularly appealing to novice and seasoned welders alike. It facilitates ease of use by promoting a smooth, stable arc, which not only enhances the overall welding experience but also reduces the learning curve for beginners, promoting confidence and competence in welding tasks.
electrode e 7018
In terms of storage and handling, the E7018 electrode demands specific care to maintain its low hydrogen properties. Proper storage in a dry environment and preheating techniques are essential to prevent the ingress of moisture, which could potentially compromise its performance. These precautions ensure that the electrode delivers optimal results and maintains its integrity over time.
The E7018 electrode’s adaptability is not limited to its welding technique capabilities but extends to its usage across various metals, including carbon steel and low-alloy steel. This adaptability makes it a cost-effective solution for projects requiring different material welds, thereby reducing the need for multiple electrode types in a single project.
Professionals in sectors such as shipbuilding, pipelines, and heavy equipment manufacturing can rely on the E7018 for its impeccable performance in challenging conditions. Known for its ability to produce high-quality results, it reinforces its position as a trustworthy candidate for critical applications where failure is not an option.
The credibility of the E7018 electrode is bolstered by its adherence to stringent industry standards and certifications, ensuring that its performance is consistent and reliable, meeting the stringent expectations of industrial applications. This adherence to standards not only confirms its quality but also its trustworthiness and reputation in the welding community.
In conclusion, the E7018 electrode provides a harmonious blend of strength, versatility, and convenience. Its robust features are a testament to its design and manufacturing excellence, lending it the expertise and authority needed to be a preferred choice among welding professionals. Its proven track record across industries speaks volumes of its trustworthiness, making it an indispensable tool for any welder's arsenal. Whether you are navigating the complexities of industrial projects or pursuing personal fabrications, the E7018 electrode stands as a reliable ally in achieving exceptional welding outcomes.