The E7018 welding electrode stands out as a staple in the welding industry, celebrated for its versatility and excellent mechanical properties. A deep dive into the various attributes of the E7018 offers invaluable insights for both novice and seasoned welders seeking to enhance their welding projects.
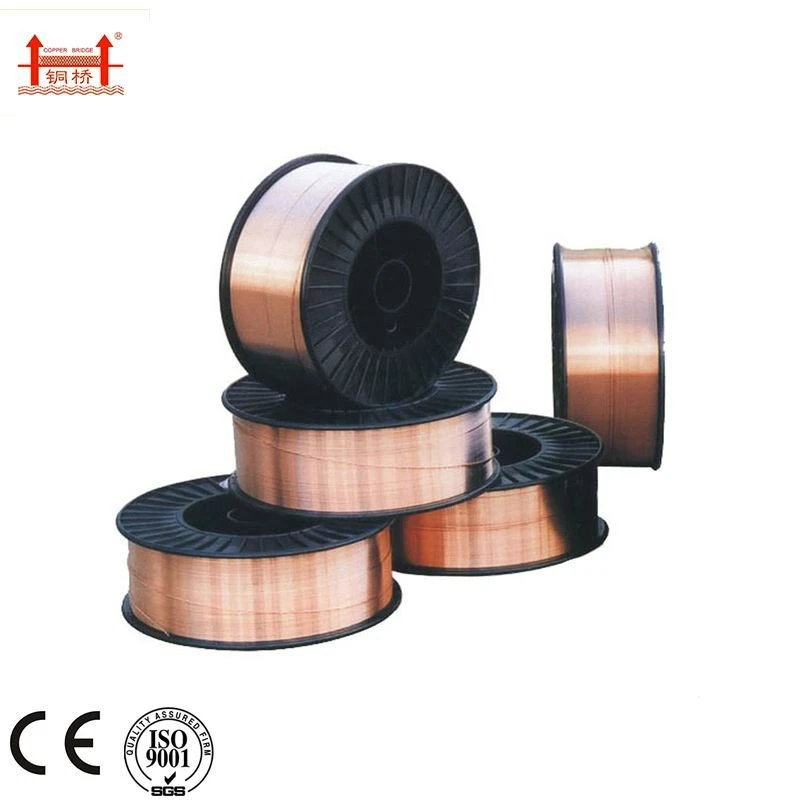
The E7018 electrode is classified under the American Welding Society (AWS) specifications, where E signifies it's an electrode, 70 represents the tensile strength of the weld, approximately 70,000 psi. The number 1 indicates the electrode can be used in all welding positions, and the final 8 characterizes the type of coating and current used. This specific combination of attributes makes the E7018 a reliable choice for producing high-quality welds in a range of environments.
Real-world experience among welders has repeatedly shown the benefits of using E7018 electrodes. Its low-hydrogen potassium coating is particularly advantageous, significantly reducing the risk of cracking by limiting the hydrogen levels in the weld area. This feature is especially critical when working with higher strength steels where cracking can be a major issue. Welders who have encountered difficulties with cracking in the past often turn to E7018 as a solution, and it delivers consistently.
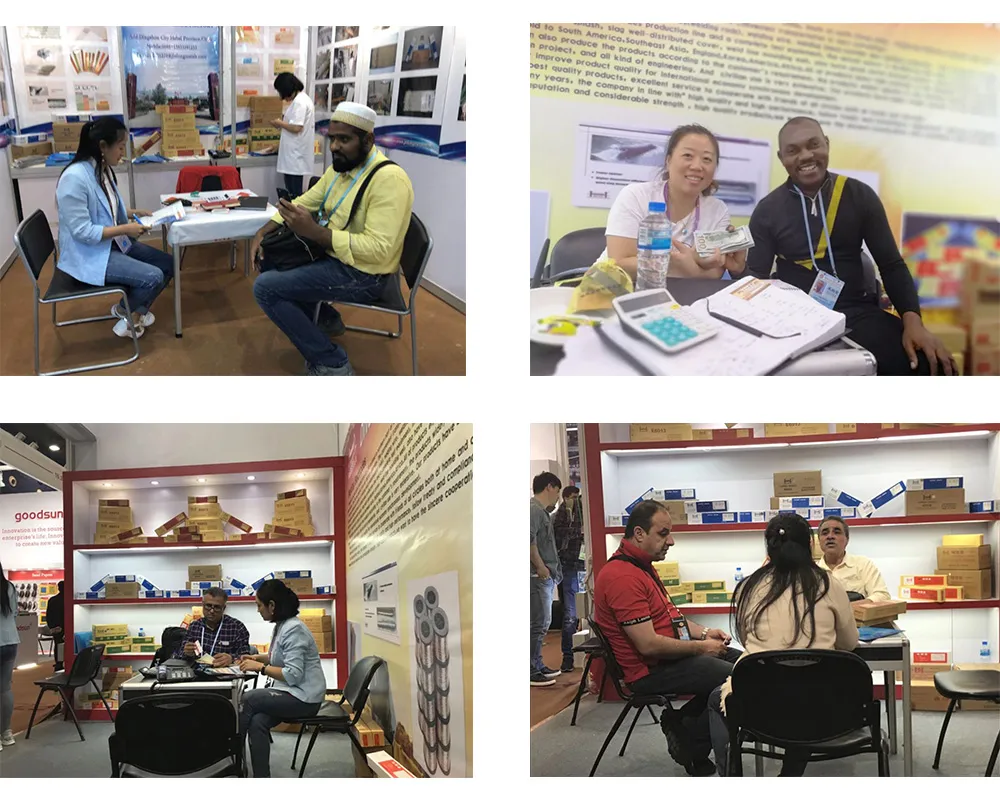
From a professional standpoint, its operation is suited for both AC and DC currents, making it adaptable to the equipment available, whether in a professional shop or a smaller workshop setting. When used with a DC current, the E7018 provides a steady arc and minimal spatter, which is perfect for welder skill development and efficient job completion. It is also noteworthy that this electrode creates a smooth, aesthetically pleasing weld bead, which is crucial in applications where the visual aspect of the weld is as important as its strength.
e7018 welding electrode
The E7018's authoritative standing in the welding field is further cemented by its widespread use across various critical industries, including construction, shipbuilding, and significantly, in structural work across the globe. Its consistent performance in creating strong, ductile joints makes it a favored choice for fabricators who need to ensure robust, long-lasting connections in their structures.
For those considering adding E7018 electrodes to their toolkit, understanding its storage requirements is vital for maintaining its integrity. It's essential to store these electrodes in a dry, controlled environment, often requiring a rod oven to prevent moisture absorption. This practice ensures that the low-hydrogen attribute of the E7018 is preserved, preventing common welding defects like porosity and hydrogen-induced cracking.
Testimonies from expert welders consistently affirm the trustworthiness of the E7018 electrode in delivering superior results. Its reputation as a go-to solution is not just due to the physical properties of the welds it creates, but also because of the confidence it instills in users. Knowing they’re working with an electrode that’s backed by a strong track record of success allows welders to focus on honing other aspects of their welding skills.
In summary, the E7018 welding electrode embodies a blend of experience-backed reliability, professional versatility, industry authority, and enduring trust. Whether one is engaged in repairing machinery, constructing edifices, or refining small-scale projects, the E7018 promises and delivers a welding solution built on strength, dependability, and durability. This makes it not just an option but a preferred choice in numerous welding applications around the world.