E7018 welding electrodes have emerged as a staple in the welding industry due to their unique specifications and characteristics. These electrodes are primarily designed for joining low carbon and medium tensile steels and execute both jobs with remarkable efficiency. Individuals who have worked with E7018 often laud its ability to produce high-quality welds with minimal risk of defects. This article aims to elucidate the specifications of E7018 electrodes and shed light on why they are a preferred choice among welding professionals.
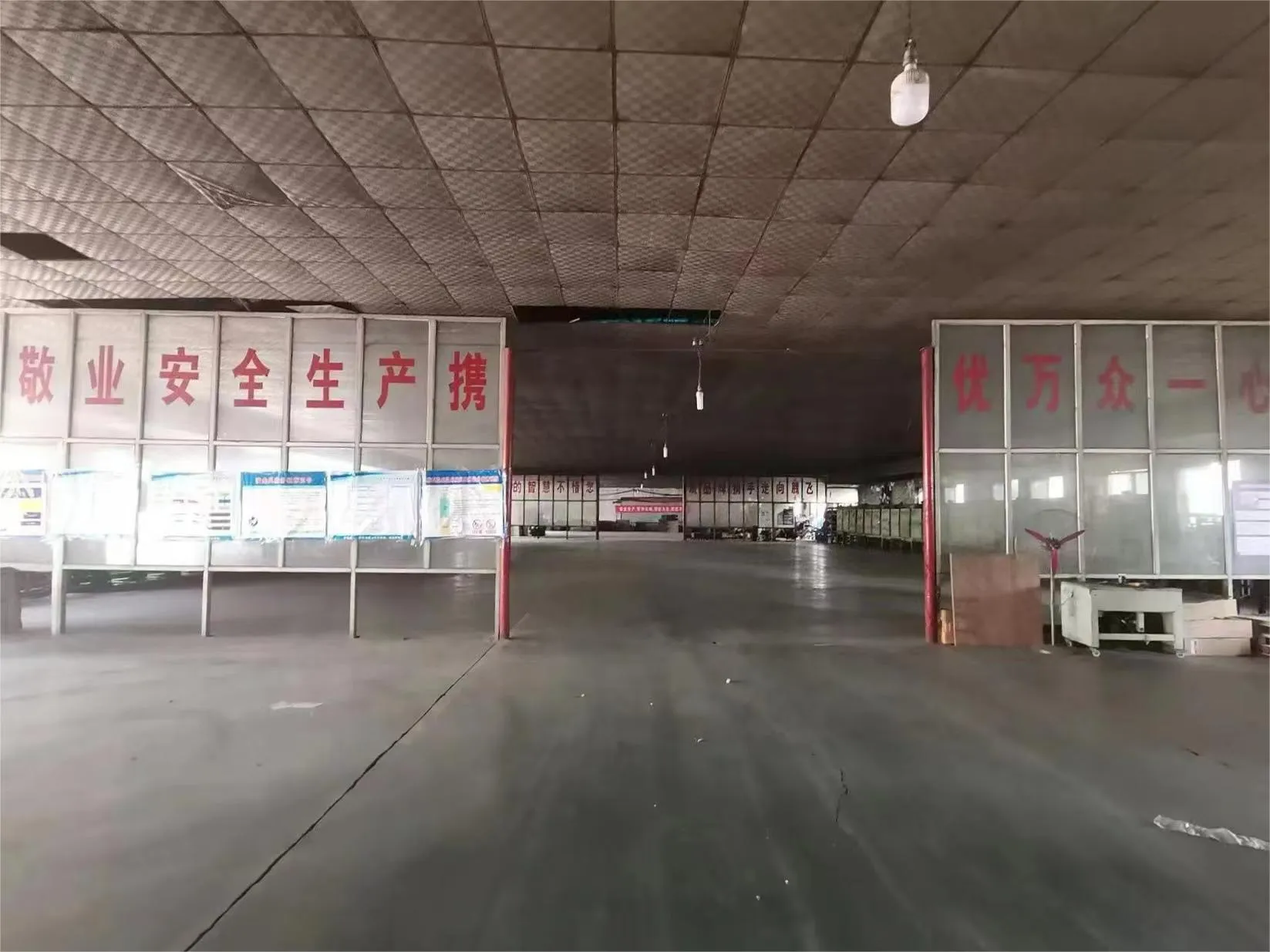
The distinct designation '7018' encapsulates key performance attributes intrinsic to these electrodes. The first two numbers, '70', signify the electrode's tensile strength, specifically 70,000 psi. This measure is a testament to its strength and stability once welded, which is an essential consideration for structural applications where performance cannot be compromised. The next digit, '1', indicates the electrode's all-position usability. Whether it's flat, horizontal, vertical, or overhead, E7018 can seamlessly adapt, making it versatile for various welding scenarios. The final number, '8', hints at the coating type and the current type that the electrode is compatible with, defining a low hydrogen electrode suitable for AC and DC both currents.
A key factor contributing to the widespread adoption of E7018 electrodes is their low hydrogen content. In the realm of metallurgy, hydrogen-induced cracking is a lingering nemesis that can lead to catastrophic failures post-weld. E7018 expertly mitigates this risk thanks to its coating which significantly reduces hydrogen diffusion into the weld pool. This low hydrogen characteristic not only fortifies the weld integrity but also enhances consistency across varying operating conditions.
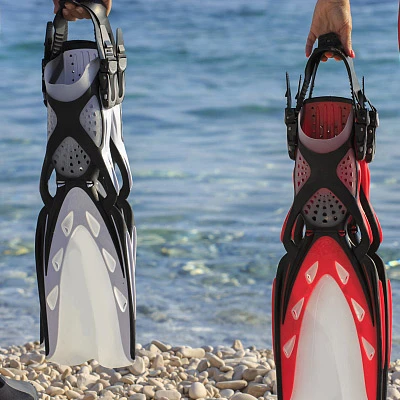
Expert welders often emphasize the smooth arc characteristics of E7018, which makes it accessible even for beginners transitioning into welding more complex assemblies. The smooth bead appearance and minimal spatter typify professionalism in craftsmanship, which is appealing in industries focusing on aesthetics as much as structural integrity. Additionally, its excellent gap bridging capabilities prove invaluable when dealing with imperfectly aligned workpieces, a common real-world scenario.
Safety is always a priority in welding, and E7018 electrodes stand out here too. The slag coverage provided is not only a protective barrier during the welding process but also aids significantly in managing post-weld clean-ups. This feature alone streamlines workflow by reducing the time typically spent on removing slag, thus enhancing productivity without compromising safety.
e7018 specification
From an authoritative standpoint, codes and standards often reference E7018 when discussing compliance with welding procedures. One such standard is the American Welding Society’s (AWS) D1.
1 structural welding code. The reliability, performance, and consistency of E7018 under rigorous testing grant it approval for numerous critical applications, instilling confidence in both engineers and inspectors who lean on its proven track record.
Trustworthiness in a product stems from not just its technical specifications but also the user experience it delivers. E7018 electrodes have garnered a reputation over the years due to positive outcomes documented across projects of varying complexities. Users continuously report reduced instances of porosity, cracking, and other common welding challenges. Its ease of use further translates to lower downtimes, fewer reworks, and consequently, reduced costs — factors that are particularly persuasive in large-scale operations.
E7018 electrodes epitomize a blend of engineering precision and practical usability, symbolizing the evolution of welding materials to cater to modern demands. Their robust specifications align well with expectations placed cross-sectorally, reinforcing them as an indispensable asset for both present and future welding ventures.
As with any tool or material in engineering, continuous assessment, and adaptation ensure relevance and efficacy. E7018, backed by empirical data and industry acknowledgment, continues to hold its ground, reinforcing a legacy that echoes precision, reliability, and excellence in the field of welding.