For anyone involved in the world of welding, understanding the nuances of electrode amperage, specifically for common electrodes like the E6013 1/8, is crucial. The E6013 electrode is widely celebrated for its versatility and ease of use, making it an accessible choice for both beginners and seasoned professionals. However, achieving the perfect weld requires mastery over electrode amperage settings, and it's essential to grasp how this affects welding quality and efficiency.
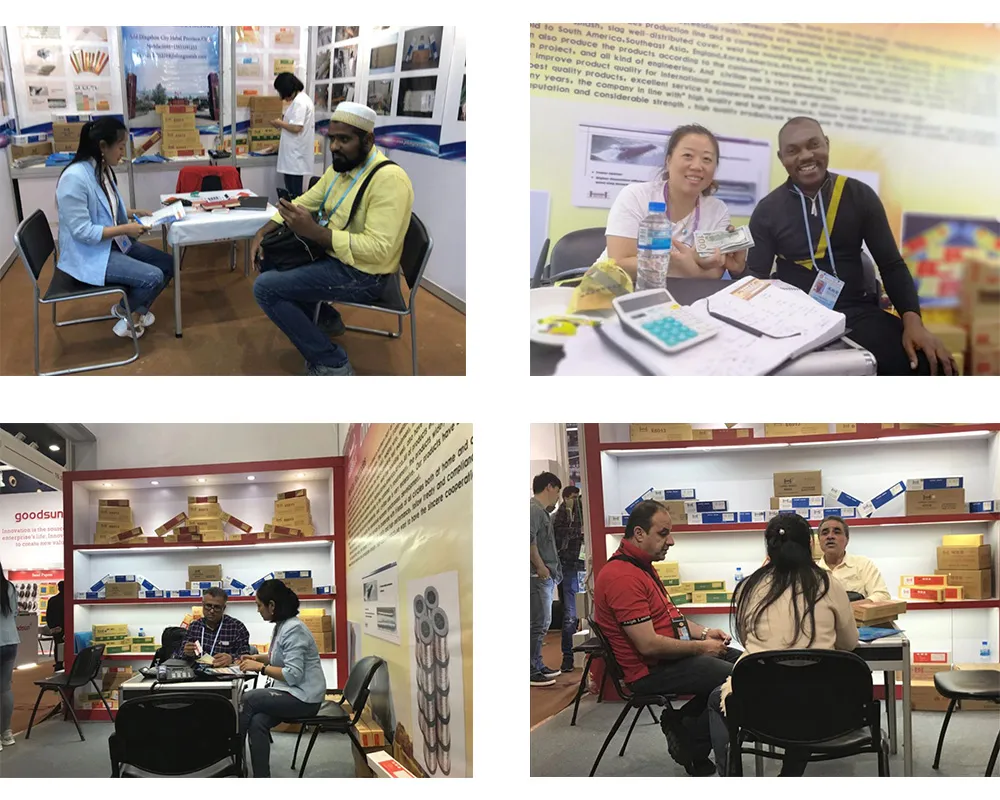
The E6013 electrode is a general-purpose welding rod, recognized for its smooth arc action and capability to produce high-quality welds in various welding positions, except vertical down. This electrode is often used in situations requiring good appearance and easy operability, such as in sheet metal welding and repair runs, where aesthetics and joint integrity are paramount.
When working with the E6013 1/8-inch electrode, a common question arises what is the optimal amperage setting? This decision is a balancing act that impacts penetration, bead appearance, and electrode performance. Generally, the recommended amperage range for E6013 1/8-inch electrodes falls between 90 to 150 amps. However, individual variables, including material thickness, welding position, and power source, play a significant role in fine-tuning this setting.
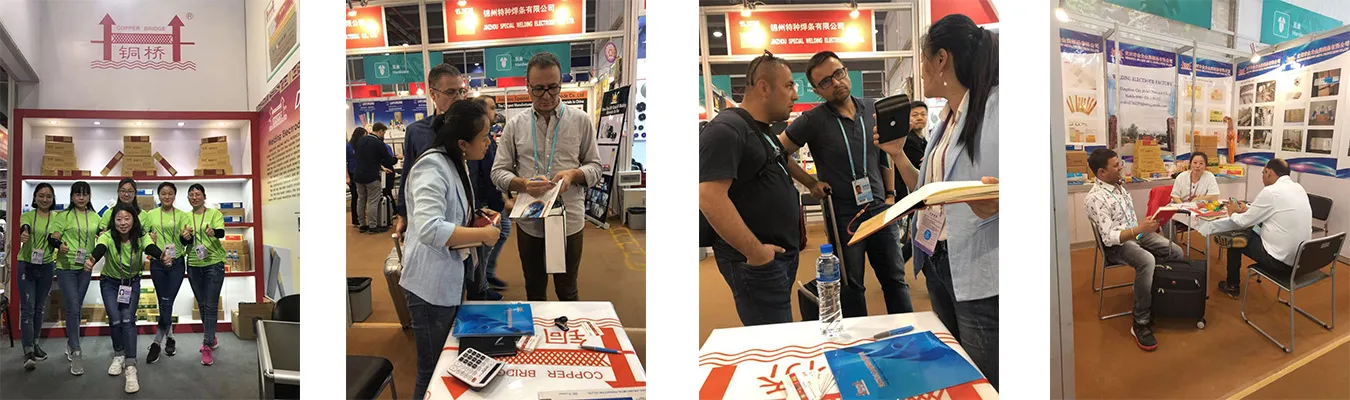
Experience shows that adjusting the amperage within this range can dramatically influence the outcome. For thinner materials, closer to the 90-amp threshold may be more suitable, ensuring minimal burn-through. In contrast, thicker materials might require pushing the amperage upwards towards 150 to secure adequate penetration. However, excessive amperage can lead to overheating, excessive spatter, and electrode decomposition, ultimately degrading the weld quality.
e6013 1 8 amperage
The expertise of seasoned welders emphasizes the importance of conducting test welds. This practical approach allows welders to observe the arc behavior and adjust the amperage to achieve the desired penetration and bead profile. Incorporating this trial-and-error method reinforces the concept that welding is as much an art as it is a science.
Moreover, it's essential to recognize the role of welding machines and their output consistency. Not all power sources deliver the same current output even when set at the same nominal amperage, underscoring the need for familiarity with one’s equipment. Trusting the amperage readings of your specific welding machine and cross-referencing with manual settings can provide a layer of certainty when adjusting for optimal performance.
A key to authoritative and trustworthy welding practices with the E6013 electrode also lies in maintaining proper technique. Holding a stable arc length, which is ideally equivalent to the diameter of the electrode, ensures a steady transfer of heat and filler material. Additionally, a consistent travel speed complements the amperage setting, as moving too quickly or sluggishly can either fail to fuse the materials properly or produce unsightly welds.
In conclusion,
successful welding with the E6013 1/8 electrode is underpinned by the meticulous adjustment of amperage. Skilled welders understand that besides the nominal guidelines, individual judgment plays a central role. It involves gauging material characteristics, experimenting with settings, and developing intimate knowledge of one's equipment—all critical in executing flawless, professional-grade welds. Cultivating these skills not only enhances expertise but also strengthens the trustworthiness and authority of a welder in this precision-driven craft.