The E310 electrode is a stellar choice for welding applications, particularly when dealing with stainless steel materials. It's specifically designed to offer high performance and reliability, which are crucial factors in maintaining the integrity of welds in demanding environments. This article delves into the characteristics and benefits of the E310 electrode, drawing upon both expert opinions and practical experiences to guide users in their purchase decisions.
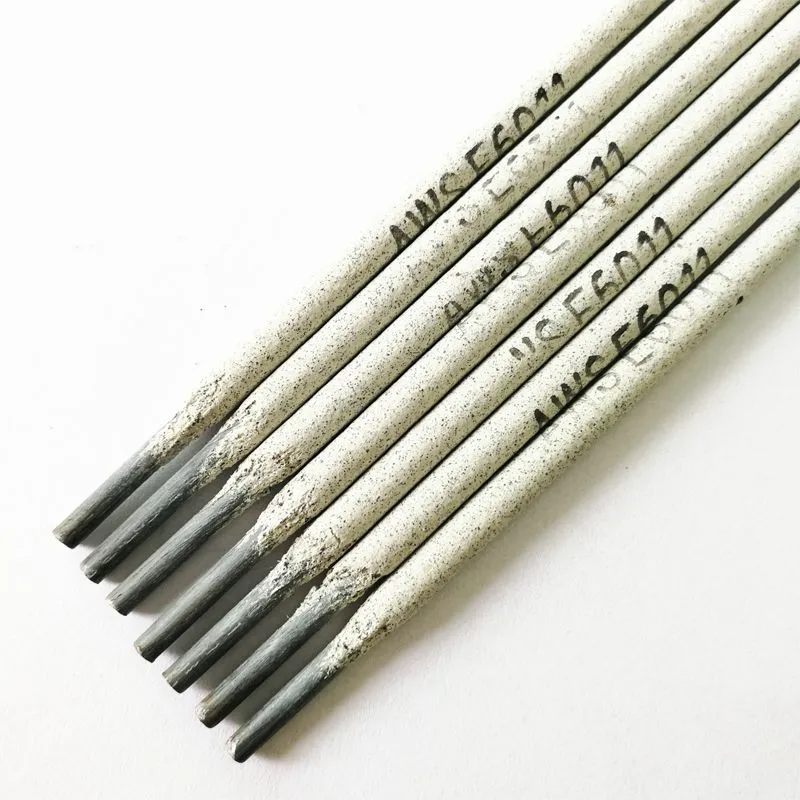
E310 electrodes are primarily composed of austenitic stainless steel alloy, which ensures excellent corrosion and heat resistance. This makes them an ideal selection for industries such as petrochemical, power generation, and shipbuilding, where materials are frequently subject to high temperatures and corrosive agents. The electrode's robust performance in these conditions enhances its reliability and broadens its applicability.
A key feature of the E310 electrode is its high chromium and nickel content, which not only improves the weld quality but also guarantees compatibility with a wide range of stainless steels. For welding professionals, this means fewer concerns about metal compatibility and a greater focus on achieving precision and durability in their projects. The versatility of the E310 electrode makes it a favorite among seasoned welders who require a dependable solution for diverse applications.
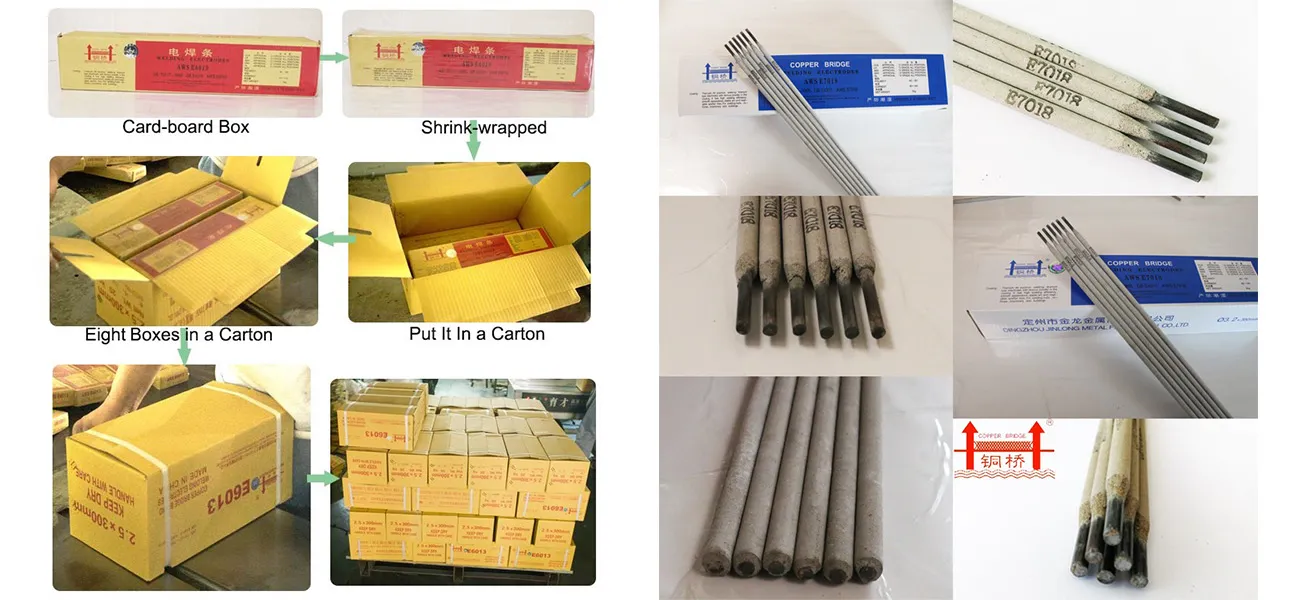
In terms of real-world application, users have reported significant improvements in weld integrity and strength when utilizing E310 electrodes. One welding expert noted that during a project involving the construction of a large-scale industrial boiler, the E310 electrode outperformed other alternatives by maintaining superior joint strength and exhibiting minimal warping even under extreme operational conditions. This endurance capability is often cited as a determining factor in the choice of electrode for critical infrastructure projects.
Professionals in the field emphasize the importance of handling and storage conditions to maximize the effectiveness of E310 electrodes. Proper storage conditions, such as controlling humidity and temperature, are vital to prevent any degradation of the flux coating that can lead to compromised weld quality. Maintaining a controlled environment ensures that the electrodes retain their intended chemical properties, which is fundamental to achieving consistent and high-quality welds.
e310 electrode
From a technical standpoint,
another aspect where E310 electrodes shine is their ease of use. The electrode is designed to provide a stable arc and produce minimal spatter, which significantly reduces cleanup time post-welding. This feature is particularly beneficial for large-scale industrial applications where time and efficiency are critical parameters. Furthermore, the electrode's capability to work efficiently in different positions adds to its versatility, allowing for greater flexibility in project execution.
Authoritative sources in the welding industry, such as the American Welding Society (AWS), back the reliability and performance claims of E310 electrodes through rigorous testing and certification. These certifications assure consumers of the electrode’s compliance with stringent standards, which boosts its credibility and trustworthiness among professionals relying on verified and high-quality materials for their work.
Buyers are advised to source their E310 electrodes from reputable suppliers to ensure they are acquiring authentic and high-quality products. The market does present counterfeit risks, and engaging with trusted vendors mitigates this concern, ensuring authenticity, and providing a safeguard against substandard performance.
In conclusion, the E310 electrode stands as a robust solution for welding needs that demand high-temperature resilience, corrosion resistance, and superior strength. Whether in the realms of heavy industry or precision engineering, this electrode commands a position of reliability backed by expert endorsement and proven field performance. Its prominent role in modern engineering applications underscores the importance of making informed and strategic purchasing decisions to leverage its full potential and advantages in professional welding projects.