The realm of welding offers a fascinating mix of techniques and tools, and one essential component in the fabrication landscape is the downhill welding electrode. For those stepping into this industry or those who are seasoned professionals, understanding its nuances can enhance performance and product outcomes.
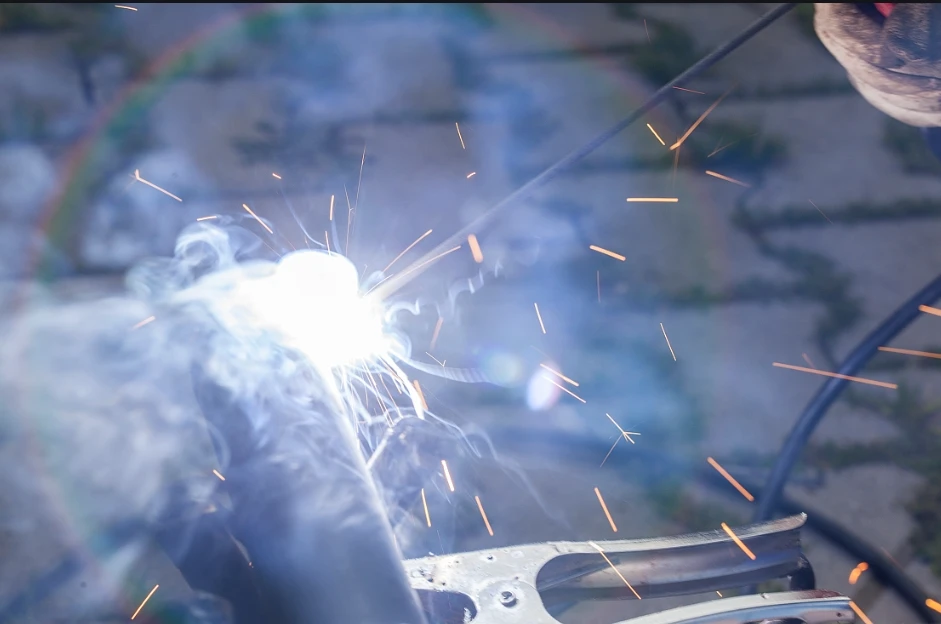
Downhill welding, characterized by its weld progression from top to bottom, is especially prevalent in industries where speed and appearance take precedence. The downhill welding electrode is tailored uniquely to cater to this technique, ensuring optimal penetration and a clean weld bead.
From an experience perspective, the primary advantage of using downhill welding electrodes is their efficiency in covering substantial lengths with speed and precision. One seasoned welder noted, Switching to a specific downhill electrode reduced our project time by almost 30% without compromising on quality. The kinetic energy in the downhill movement aids the electrode to maintain a stable arc, producing a more uniform weld that demands less post-weld treatment.
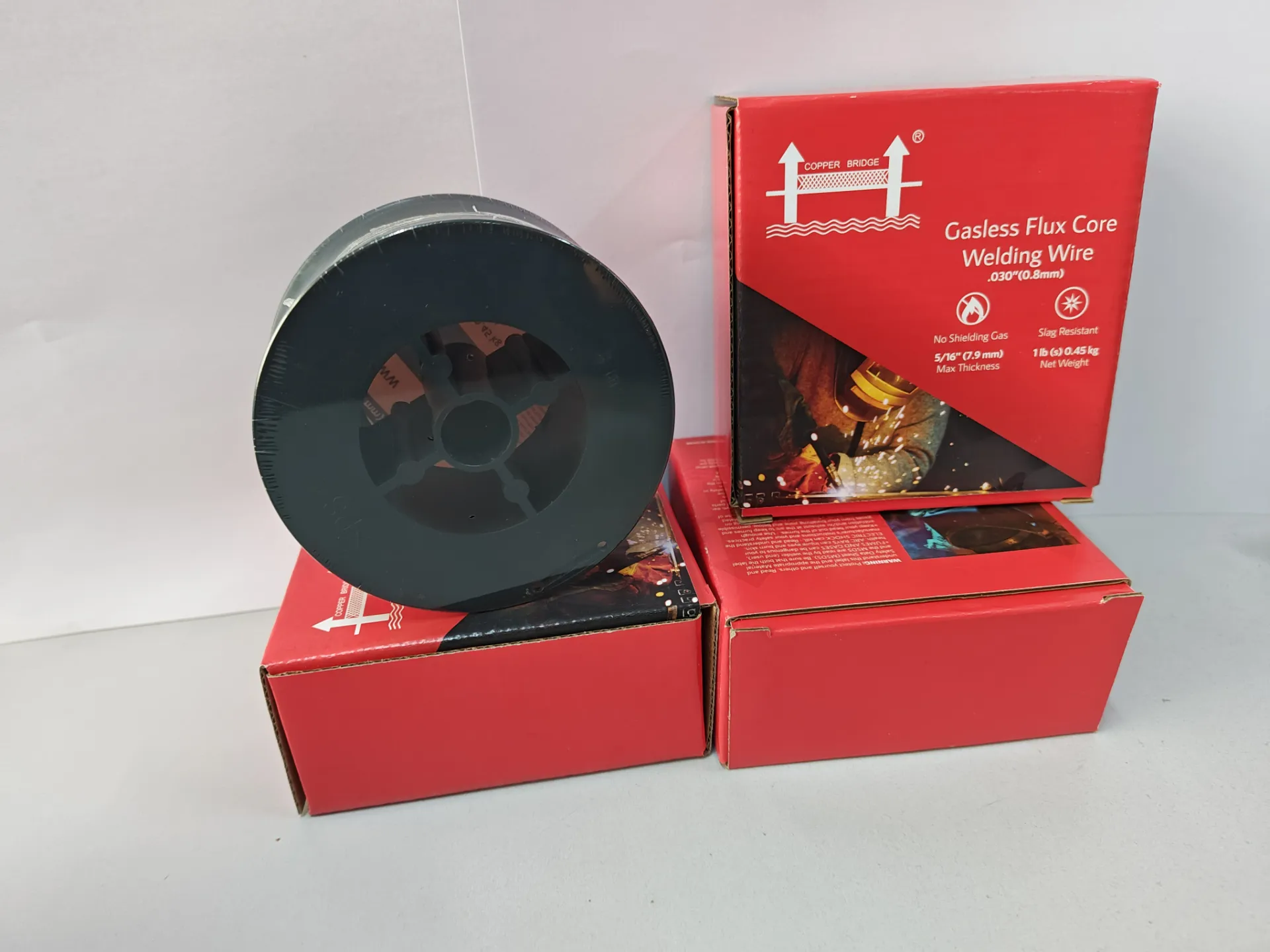
The expertise involved in choosing the right downhill welding electrode cannot be overstated. It requires an understanding of the base metal properties, joint design, and the desired penetration depth. Designed with specific flux coatings, these electrodes support greater deposition rates, making them ideal for large-diameter pipes and structural components. Their effectiveness in delivering a smooth, clean weld bead has been demonstrated in various sectors, including oil and gas pipelines, where joint integrity is paramount.
downhill welding electrode
From a standpoint of authoritativeness, numerous industry certifications back specific downhill welding electrodes, such as AWS classifications that ensure they meet stringent quality standards. Consulting with welding engineers who specialize in structural applications can provide insights into selecting electrodes that align perfectly with operational requirements and environmental conditions, such as outdoor settings where wind and temperature variations may affect weld quality.
Trustworthiness in downhill welding electrodes is rooted in their consistent performance. Reputable manufacturers conduct extensive R&D, evidenced by rigorous testing protocols that push these electrodes to withstand demanding conditions. Testimonials from industry professionals who have relied on these electrodes for critical infrastructure projects further cement their credibility. As one project manager remarked, The reliability of our chosen downhill electrode saved us countless hours in quality assessments, giving us confidence in every completed joint.
For those involved in procurement, understanding the importance of certifications and client feedback becomes crucial. Partnering with suppliers who offer a proven track record and customer support can significantly enhance your welding operations' results.
In summary, integrating downhill welding electrodes into your work not only optimizes the welding process but also assures compliance with industry standards and project deadlines. The blend of user experience, technical expertise, certified authority, and proven trust makes these electrodes invaluable in today's fast-paced welding industry. Whether you're fabricating pipelines or constructing skyscrapers, the right downhill welding electrode can be the cornerstone of your project’s success, ensuring every weld stands the test of time.