Welding rods, also known as welding electrodes, are essential components in the realm of welding. Their critical function in establishing the connection between the welding equipment and the base material ensures a robust and durable weld.
To master the art of welding, understanding the various types of welding rods and their applications is pivotal.
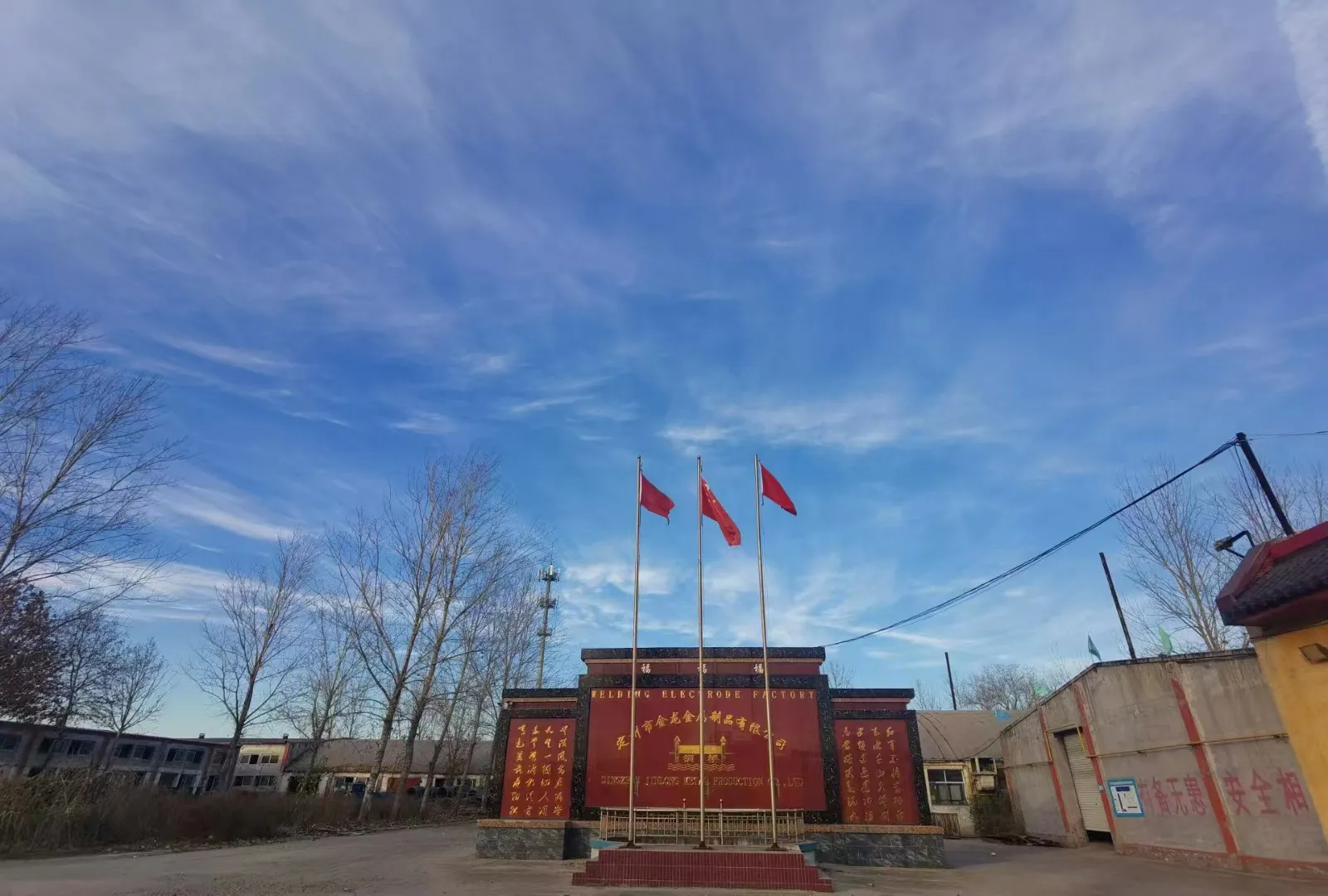
Welding rods are classified primarily into consumable and non-consumable electrodes. Consumable electrodes are designed to melt and fuse with the base material, forming the weld itself. Conversely, non-consumable electrodes do not melt and are primarily used as a conduit for electrical current.
Among consumable electrodes, the SMAW (Shielded Metal Arc Welding) rods are prevalent due to their versatility. These rods come in various compositions tailored to specific materials and welding conditions. For instance, E6010 rods are known for their deep penetration and are ideal for vertical or overhead positions, while E7018 rods offer a low hydrogen content, crucial for welding high-strength steel to minimize risks of cracking.
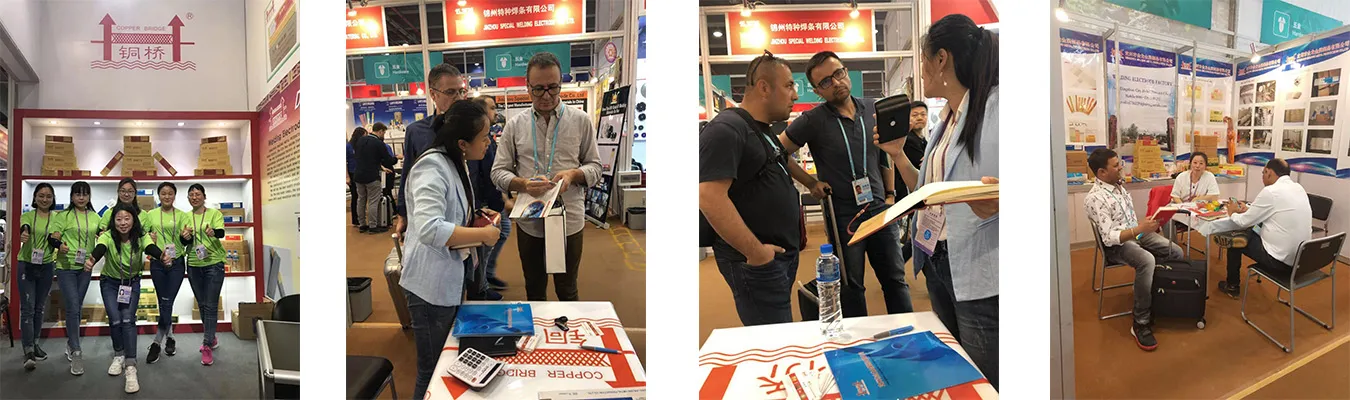
Another category within consumable rods includes the FCAW (Flux-Cored Arc Welding) wires. These require less skill to apply compared to SMAW rods, making them suitable for novices. Their tubular design, filled with flux, provides additional insulation and reduces spatter, making them suitable for outdoor construction where windy conditions might hinder other types of welding.
MIG (Metal Inert Gas) welding rods, or wires, stand out for their ease of use, and they enable continuous welding due to their wire-fed mechanism. MIG wires are excellent for thin sheets and auto body work, offering a cleaner weld with minimal cleanup. ER70S-6 is a popular choice in this domain, providing excellent tensile strength and good corrosion resistance.
different types of welding rods
Transitioning to non-consumable rods, the TIG (Tungsten Inert Gas) welding rods deserve mention. These electrodes do not melt during welding, allowing precision and control. They are indispensable for scenarios demanding clean, high-quality welds on thin materials such as aluminum or stainless steel. The common tungsten electrodes include thoriated, ceriated, and lanthanated varieties, each offering unique advantages. Thoriated tungsten rods are known for their durability and strong arc starts, but they require careful handling due to their slight radioactivity.
It's also vital to consider the coatings or flux material employed in these rods. The coating stabilizes the arc, protects the weld from impurities, and can greatly influence the resultant weld's mechanical properties. For instance, cellulosic coatings found on E6010 rods assist in generating a forceful arc, facilitating deep penetration and fast welding speeds, which are advantageous in high-pressure pipelines.
While expertise in choosing the right type of welding rod comes with experience, manufacturers like Lincoln Electric and Hobart provide comprehensive guides and support to aid both novices and experts in making informed decisions. For those pursuing industrial applications, consultation with welding technologists and utilizing product manuals can enhance understanding and effectiveness.
In summary, welding rods are more than simple consumables; they are tailored and engineered for specific tasks and materials. Mastering their use unlocks potential for quality welding, fostering trust in the craftsmanship involved. As welding technology progresses, staying informed on the latest advancements in welding rod compositions and techniques proves invaluable for achieving excellence in product fabrication and repair.