When it comes to welding, selecting the appropriate electrode is pivotal to achieving optimal results. Two of the most commonly compared electrodes are 6011 and 7018, each with distinct characteristics and applications that make them suitable for different tasks. Understanding their unique features not only enhances welding performance but also ensures the structural integrity and longevity of the welds.
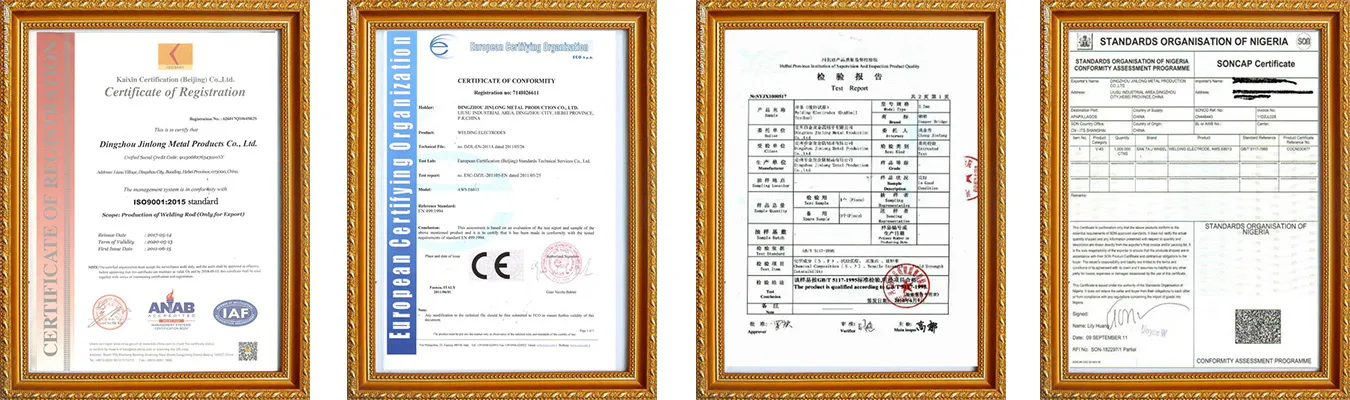
6011 electrodes are renowned for their versatility and impressive penetration capabilities. These rods are ideal for welding through rust, oil, dirt, or paint, which makes them particularly useful for maintenance and repair work. Their fast-freezing arc allows for effective vertical and overhead welding, accommodating a variety of positions. This ensures a great degree of flexibility on job sites where precise conditions cannot always be controlled.
The deep penetration of 6011 electrodes is due to their cellulose sodium coating, which produces a high-pressure arc and a forceful spray transfer. This capability allows for welding on materials that may not be perfectly fitted or aligned, making them indispensable for tasks on farms, in construction, and for heavy machinery repairs. Moreover, these electrodes work well with both AC and DC power sources, which adds another layer of versatility, especially when accessibility to specific power supplies can be limited.
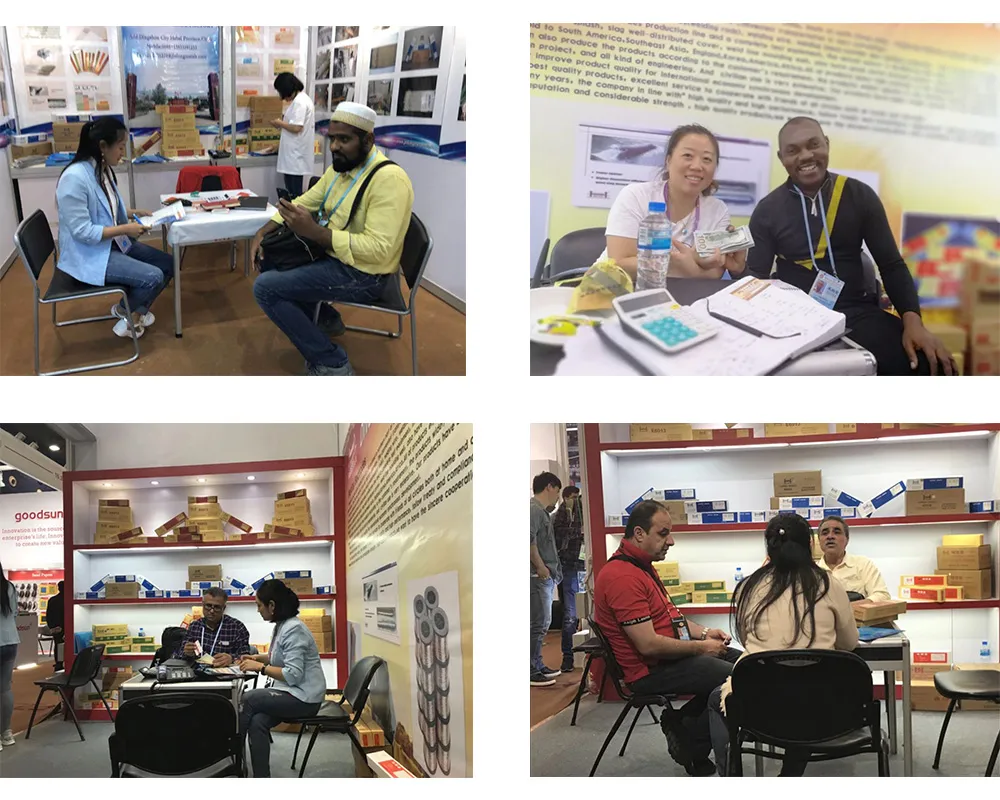
On the other hand, 7018 electrodes are typically preferred for projects requiring high-strength welds and where aesthetic presentation is critical. Their low-hydrogen potassium coating significantly reduces the risk of cracking, contributing to a smoother and more visually appealing weld bead. This makes 7018 rods a go-to option for structural steel welding, pressure vessels, and bridges, where the welds must withstand rigorous inspections and meet stringent standards.
The low-hydrogen nature of 7018 electrodes requires them to be kept dry before use; moisture can compromise the integrity of the weld by introducing hydrogen, which could lead to cracking. Proper storage in a rod oven is often necessary to maintain their effectiveness. Additionally, while they offer superior weld quality, especially on clean and new metals, the need for a DC power source in most cases and their somewhat larger slag make them less agile than 6011 when welding in challenging positions.
difference between 6011 and 7018
When deciding between 6011 and 7018, experience often dictates the selection. For welders working in environments where conditions are less than ideal, the forgiving nature of 6011 makes it the tool of choice. Contrastingly, in controlled settings where weld quality and appearance cannot be compromised, and where pre-weld preparation can be extensive, 7018 electrodes provide unmatched finished results.
Authoritative resources in the welding domain consistently highlight these attributes. The American Welding Society (AWS) outlines classifications that indicate the tensile strength and position capabilities of these electrodes, ensuring users select the correct rod for their specific project needs. Aligning choice with the AWS guidelines not only aids in achieving optimal results but also instills confidence in the structural durability of the welds formed.
In terms of trustworthiness, numerous case studies and expert testimonials from seasoned welders consistently affirm the performance characteristics of both 6011 and 7018 electrodes. Practical experience echoes the theoretical advantages these electrodes provide, cementing them as staples in professional welding kits. Training programs, as a result, often include comprehensive modules focusing on the correct usage, benefits, and limitations of each electrode type, preparing the next generation of welders to accurately assess and select the best tool for their requirements.
Ultimately, the decision between 6011 and 7018 hinges on specific project demands, including material condition, environmental settings, and the required strength and aesthetics of the weld. Each electrode, backed by expert knowledge and seasoned application, serves a vital role in welding, proving that informed selection is as crucial as the skill applied during the welding process itself.