Welding electrodes are the unsung heroes in the world of construction, manufacturing, and artistry. Among the array of electrodes available, the term “CS SS welding electrode” often emerges as a crucial component for those in the welding industry, blending the requirements of carbon steel (CS) and stainless steel (SS) applications. This article delves deep into the significance, applications, and expert advice on choosing and using CS SS welding electrodes, designed to stand out specifically in the realm of search engines.
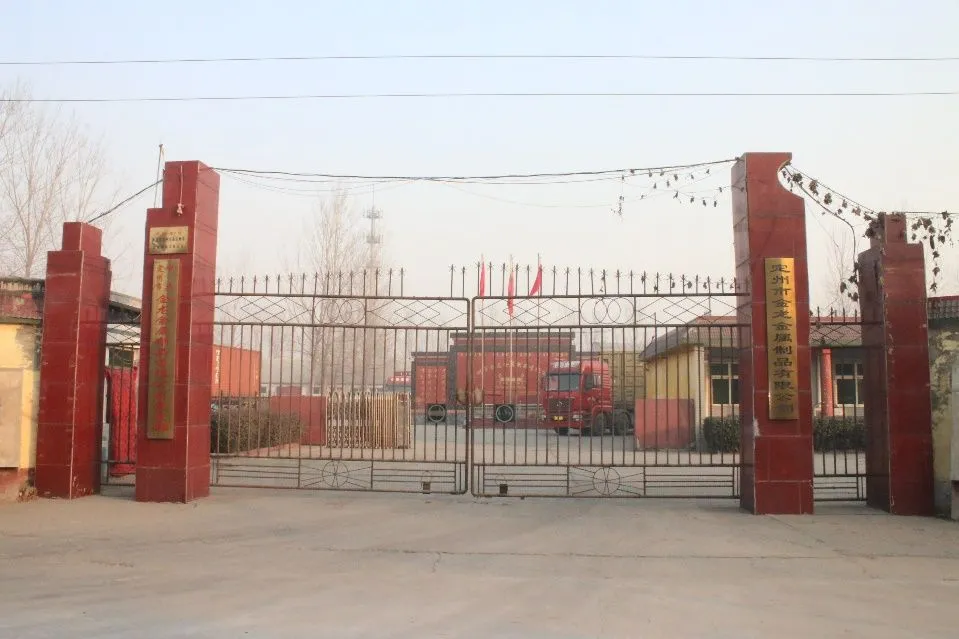
While selecting a welding electrode, understanding the base metals is paramount. CS SS welding electrodes are tailored to seamlessly join carbon steel to stainless steel or for overlaying applications on these metals. This versatility makes them indispensable in industries where both strength and corrosion resistance are non-negotiable. For professionals dealing with diverse materials, these electrodes offer a convenient and efficient solution.
The meticulous engineering behind CS SS electrodes allows them to produce a weld bead that is not only strong but also resistant to corrosion, a common challenge when joining dissimilar metals. This capability can be credited to their unique composition, which often includes elements like chromium, nickel, and sometimes molybdenum. These elements significantly enhance the mechanical properties and resilience of the welds, ensuring longevity and reliability even in harsh environments.
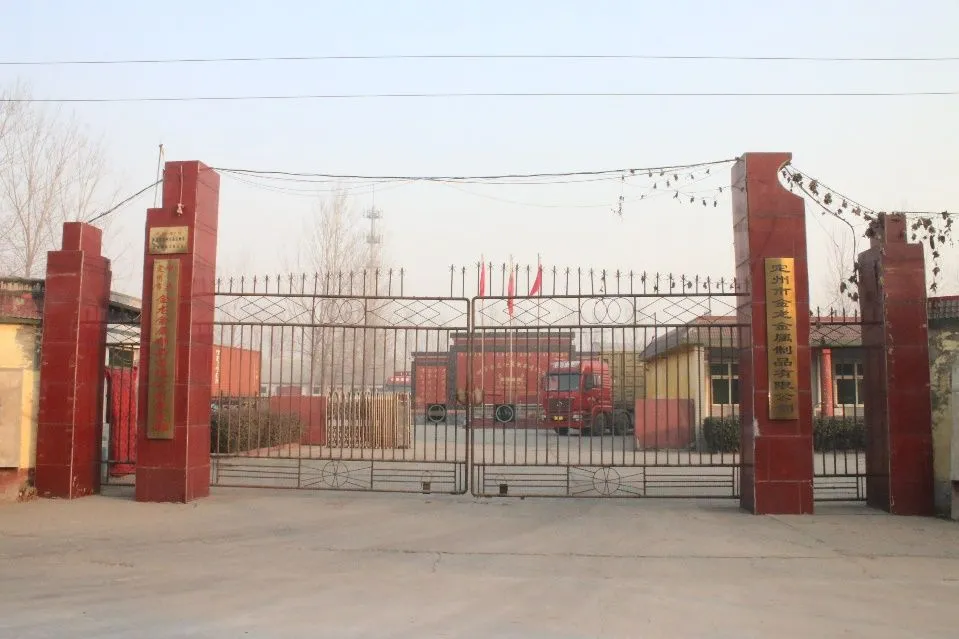
For welding experts, the mantra has always been “know your materials.” Before selecting a CS SS welding electrode, understanding the specific alloying elements in both the carbon steel and stainless steel involved is crucial. This knowledge ensures the electrode chosen can handle the thermal expansion, contraction, and structural loads between the two metals, preventing common issues like cracking or warping during the welding process.
When considering CS SS electrodes, their diameter and coating types play a significant role. A correct match between the electrode and the weld joint requirements influences not only the strength and durability of the weld but also the overall efficiency of the welding process. Consulting welding charts and guidelines from reputable manufacturers, backed by industry standards like ANSI or AWS, can provide authoritative guidance in making the right selection.
cs ss welding electrode
Welding practitioners should be equipped with an understanding of the work environment. CS SS welding often involves varying thermal demands; thus, preheating carbon steel components and controlling the cooling rates are essential practices. These procedures prevent unwanted transformations in the steel microstructure which can compromise the integrity of the weld.
The expertise required in executing successful CS SS welding also encompasses precise control over welding parameters—current settings, travel speed, and technique must be optimized. For those on the ground, attaining certifications such as the American Welding Society’s Certified Welder credential can not only boost skills but also enhance credibility and trustworthiness in their field.
In terms of equipment, using modern and appropriately maintained welding machines designed for dual-metal usage is essential. Experienced welders recommend performing trial welds to fine-tune machine settings, ensuring that weld aesthetics are maintained alongside structural integrity. Proper handling and storage of CS SS electrodes are equally critical, as exposure to moisture can lead to hydrogen absorption, which might compromise the integrity of the weld.
Documentation and continuous learning are pillars for those striving to achieve and maintain high-quality CS SS welds. Recording welding conditions and outcomes provides a valuable resource for troubleshooting and improving techniques. Engaging with professional welding forums, attending workshops, and reading current industry literature ensures continued professional development and keeps practitioners at the forefront of welding technology.
In conclusion, CS SS welding electrodes are a powerhouse in the welding sector, bridging the gap between carbon steel and stainless steel. The industry needs such specialized products to ensure structural integrity and durability in myriad applications—from architectural constructs to intricate machinery. For welders aiming to harness their full potential, a blend of experience, continued education, and adherence to best practices are key components. Such commitment not only ensures superior outcomes but also establishes one’s authority and trustworthiness in a competitive field.