Exploring the nuanced world of cast iron welding rod types requires a profound understanding of metallurgy, welding techniques, and material-specific challenges. Cast iron, known for its brittleness and high carbon content, presents unique challenges when it comes to welding. However, using the correct type of welding rod can significantly impact the effectiveness and durability of the weld. Here, we’ll delve into the different types of welding rods designed for cast iron, each engineered for specific applications and outcomes, reflecting on the critical elements of experience, expertise, authoritativeness, and trustworthiness.
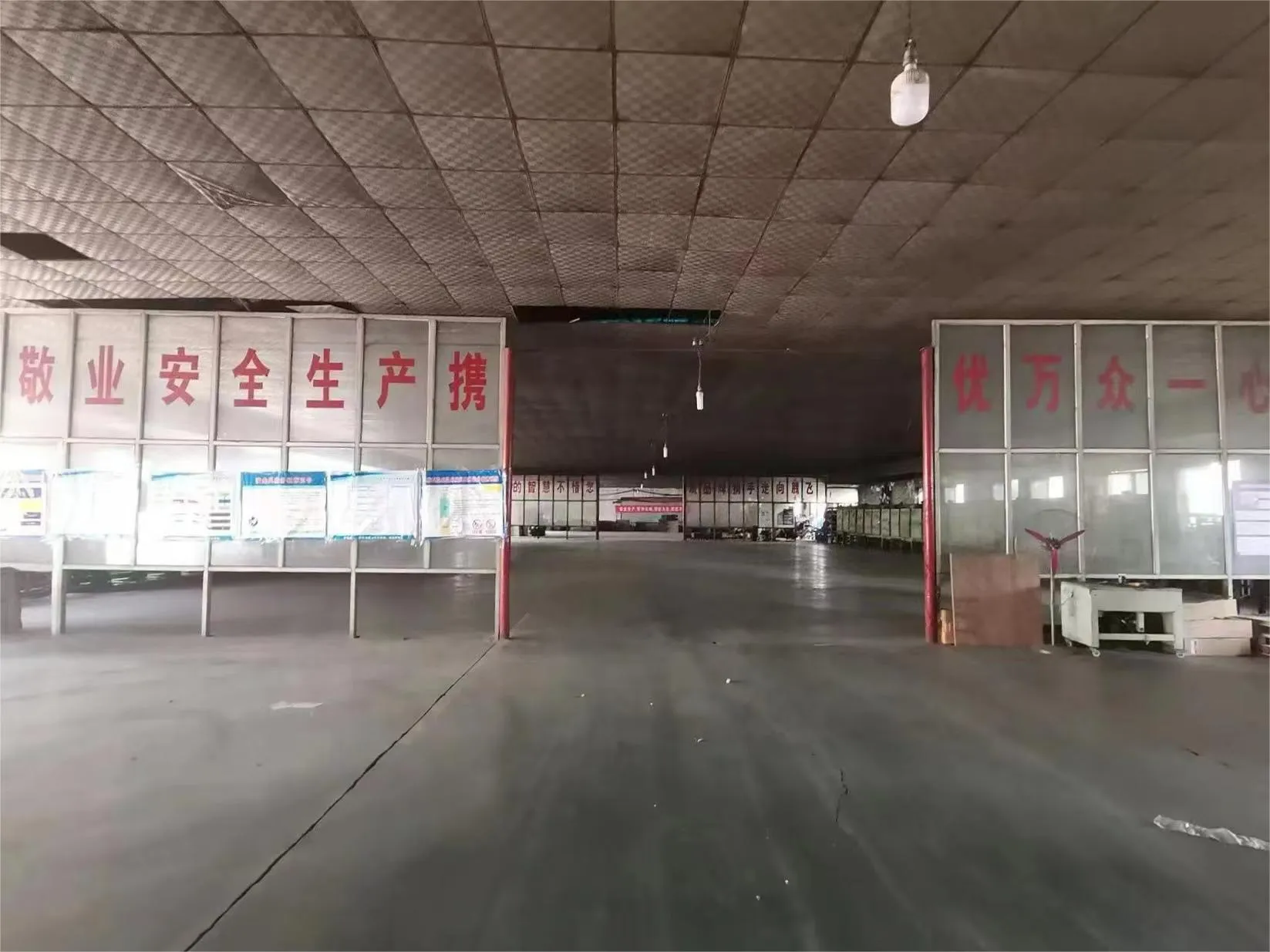
Nickel-Based Electrodes
Nickel-based electrodes are one of the most popular selections for welding cast iron due to their ductile properties. These rods, such as the AWS ENi-CI, offer excellent machinability and deposit strength. They are often used in applications where minimizing cracking is crucial. An advantage of nickel rods is their compatibility with both pre and post-heated conditions, making them versatile across various projects. Experienced welders prefer these electrodes for repairing cracked cast iron parts like engine blocks and pipes, citing their ability to create strong, reliable welds that maintain structural integrity.
Steel-Based Electrodes
Steel-based electrodes are another viable option, particularly for non-critical repairs. These electrodes are typically used when cost efficiency is a priority and the appearance of the weld is not of foremost importance. While they are less ductile than their nickel counterparts, steel rods like AWS ESt promise sufficient strength for many general maintenance tasks. Expertise in using these rods involves understanding their limitations in terms of flexibility and working conditions that may not tolerate impact stress or thermal cycling.
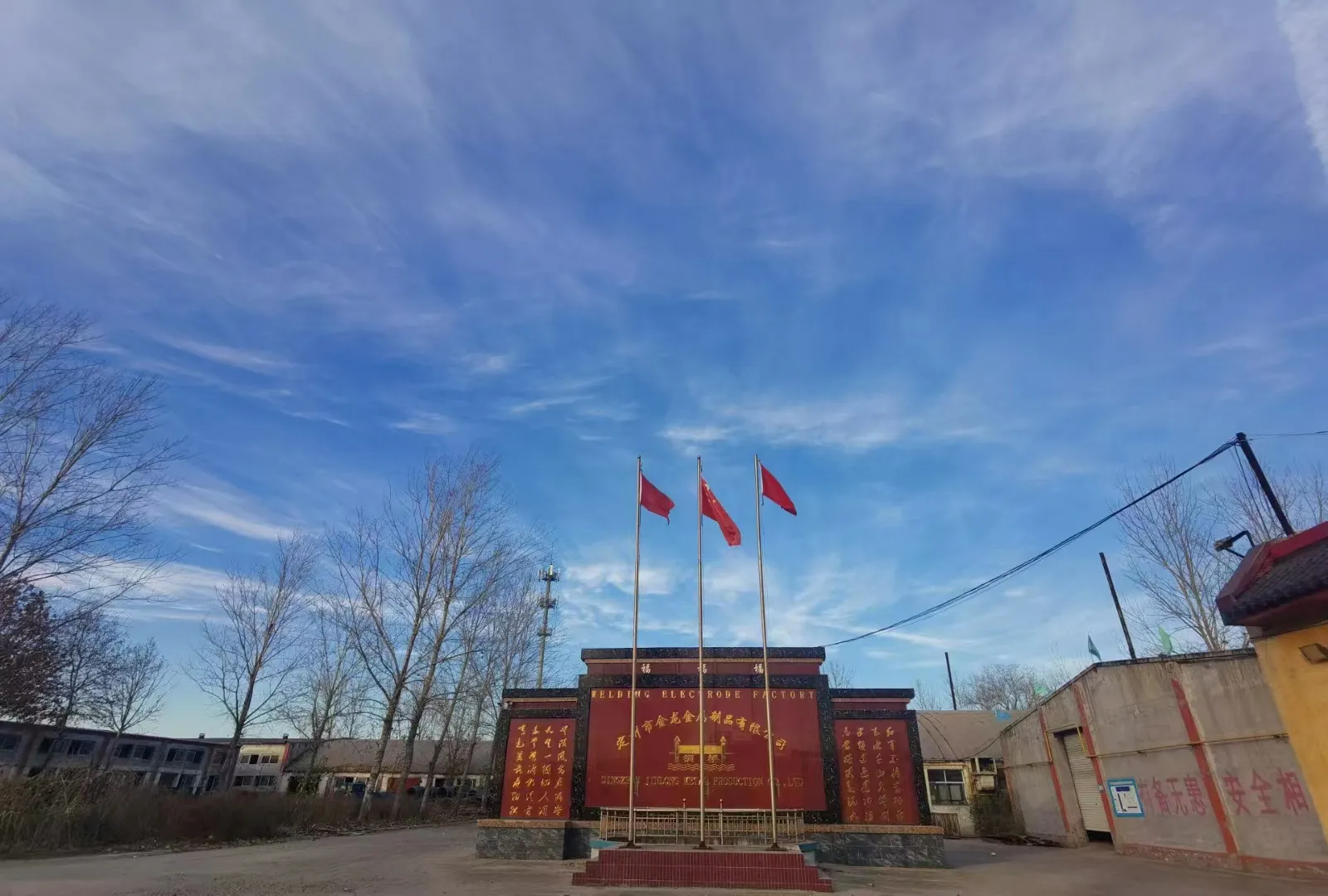
Bronze-Based Electrodes
Bronze rods offer a unique solution for cast iron welding, especially when dealing with high-stress applications or parts that experience frequent thermal expansion and contraction. Offering excellent thermal conductivity, these rods are prized for their ability to create strong adhesion without making the weld zone excessively hard or brittle. Welders with extensive hands-on experience emphasize the importance of surface preparation and the controlled application of bronze electrodes to ensure optimal bond and performance.
cast iron welding rod types
Fabrication and Repair Contexts
Choosing the right welding rod extends beyond rod composition. It involves a comprehensive assessment of the job’s requirements, such as whether the priority is structural strength, appearance, or machinability. In industrial fabrication settings where precision and durability are paramount, the expertise of seasoned professionals becomes indispensable, making their advisory role crucial to project success.
Factors Influencing Choice of Welding Rod
Several factors dictate the choice of welding rod for cast iron, including the cast iron type (grey, white, ductile), the size and shape of the parts to be welded, and the potential mechanical stresses they may encounter in service. Understanding these factors through a lens of authoritativeness, welders tackle projects with a strategic mindset, tailoring their techniques to suit each unique scenario.
Trust and Safety Measures
Trustworthiness in welding projects, especially those involving safety-critical components, hinges on not only using the right materials but adhering to stringent safety and inspection protocols. This includes pre-weld planning, post-weld inspection, and maintaining control over environmental factors such as moisture and temperature, which could impact weld quality.
In conclusion, mastering cast iron welding involves an intricate balance of selecting the appropriate welding rods, applying the correct techniques, and understanding the broader context of each project’s requirements. For professionals in the welding industry, continuous learning and adaption to evolving techniques and materials ensure not just the success of individual projects but also the advancement of the industry at large in offering reliable solutions tailored to the diverse challenges presented by cast iron.