Choosing the right welding rod is fundamental to the success of any welding project, especially when dealing with cast iron. Cast iron is renowned for its unique properties that require specialized handling, making the selection of the welding rod crucial. The term cast iron welding rod no refers to the importance of identifying which welding rods are suitable for cast iron without specifying a single product, opening the field for understanding the best options available.
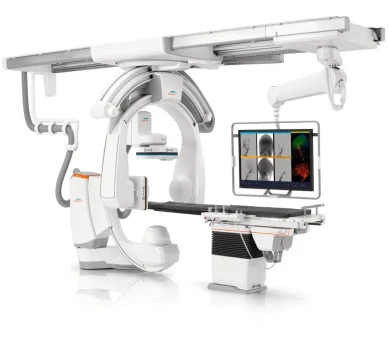
Throughout history, cast iron has presented a complex challenge for welders due to its high carbon content and brittleness. Unlike other metals, welding cast iron necessitates an understanding of its behavior under stress and heat. The nuances of welding cast iron stem largely from its tendency to crack or distort if not managed properly during the welding process.
Experience plays a pivotal role in mastering cast iron welding. A seasoned welder has learned through trial and error which rods offer the best results, adapting techniques to the unique characteristics of the specific cast iron at hand. Nickel-based welding rods, for example, are often recommended due to their strength and flexibility, which compensate for cast iron's tendency to crack. Nickel 99 and Nickel 55 are two prominent types of rods that professionals often prefer, each offering different properties that can be leveraged depending on the specific requirements of the task.
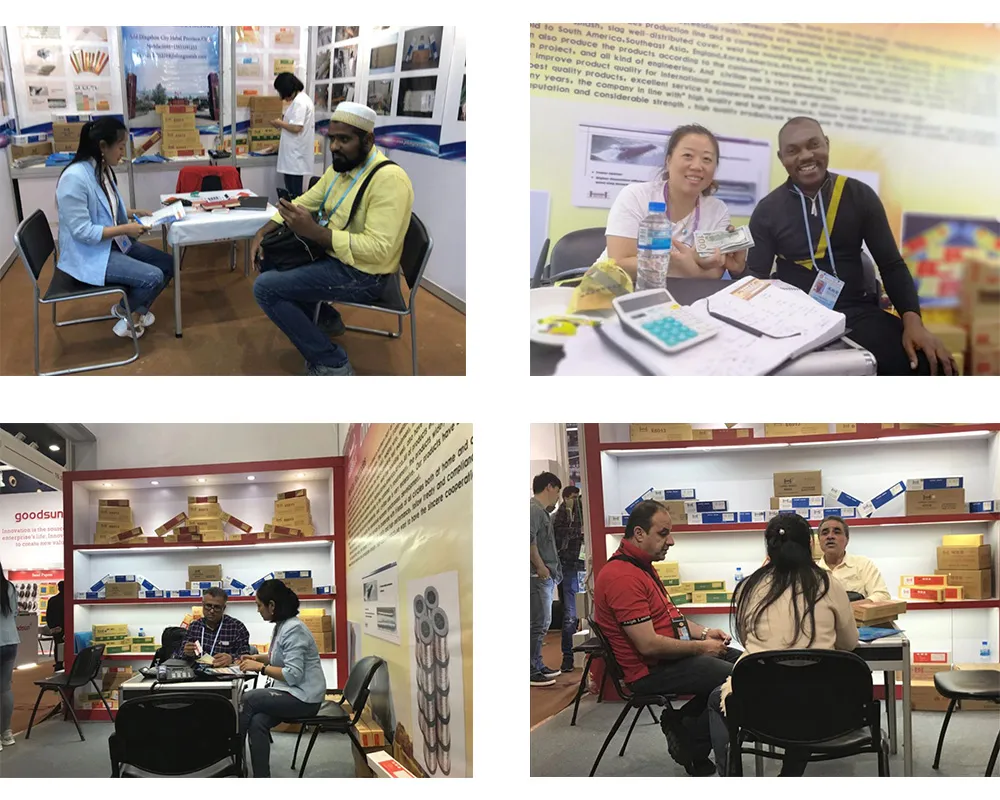
Expertise in this niche area requires not only familiarity with the materials but also the ability to troubleshoot and adjust on the fly. Many experts agree that preheating cast iron to a specific temperature can mitigate cracking. Controlling the cooling process is equally crucial to avoid rapid temperature changes that lead to stresses in the material. A professional welder understands these variables and adjusts techniques accordingly, ensuring optimal outcomes regardless of casting variations.
Authoritativeness in the domain of welding means staying updated with technological advancements and material studies. Over the years, welding rod manufacturers have developed rods designed specifically for cast iron, which incorporate elements that enhance ductility and reduce the risk of cracking. Companies renowned for their innovation in welding technology often provide detailed user guides and technical support to maximize the effectiveness of their products. By relying on these trusted sources, welders can access the latest industry knowledge and tools.
cast iron welding rod no
Trustworthiness also hinges on the sharing of authentic experiences and results. Welders dedicated to quality outcomes document their processes, successes, and failures, creating a wealth of knowledge for peers in the industry. Online forums and welding communities often serve as platforms where such information is exchanged, fostering a collaborative environment where individuals can learn from shared experiences.
When selecting a welding rod for cast iron, it is essential to consider the specific type of cast iron being welded—grey, ductile, or malleable—each of which may respond differently to welding techniques. Professionals recommend conducting a small test weld on a sample piece before proceeding with the main project to evaluate the compatibility of the rod and the material.
Finally, maintaining high-quality standards is non-negotiable when using cast iron welding rods. Continuous education through workshops and certifications ensures that welders maintain proficiency in the latest techniques and safety protocols. Rigorous adherence to these standards reassures clients about the integrity of the work performed, contributing significantly to building a reputation for reliability and excellence in the field.
By understanding these critical factors, welders can make informed decisions that lead to successful projects, reinforcing their reputation and that of the industry at large. Cast iron welding, with the appropriate rod and technique, transforms from a daunting task into a showcase of expertise and skill.