Choosing the right cast iron welding rod can significantly impact the success of a welding project. When it comes to weld repair or construction involving cast iron, selecting a welding rod with the appropriate properties is crucial. Cast iron, known for its durability and excellent wear resistance, requires special consideration due to its unique metallurgical structure. In this article, we'll delve into the world of cast iron welding rods, offering insights based on real-world experiences and professional expertise.
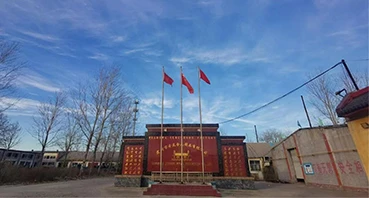
The Challenge of Welding Cast Iron
Cast iron's unique properties—such as high carbon content and brittleness—pose challenges during welding. It's susceptible to cracking when subjected to rapid temperature changes. Thus, the choice of welding rod plays a pivotal role in minimizing these risks. Over the years, professionals have shared their experiences, highlighting both successes and pitfalls specifically attributed to the correct or incorrect choice of welding rods.
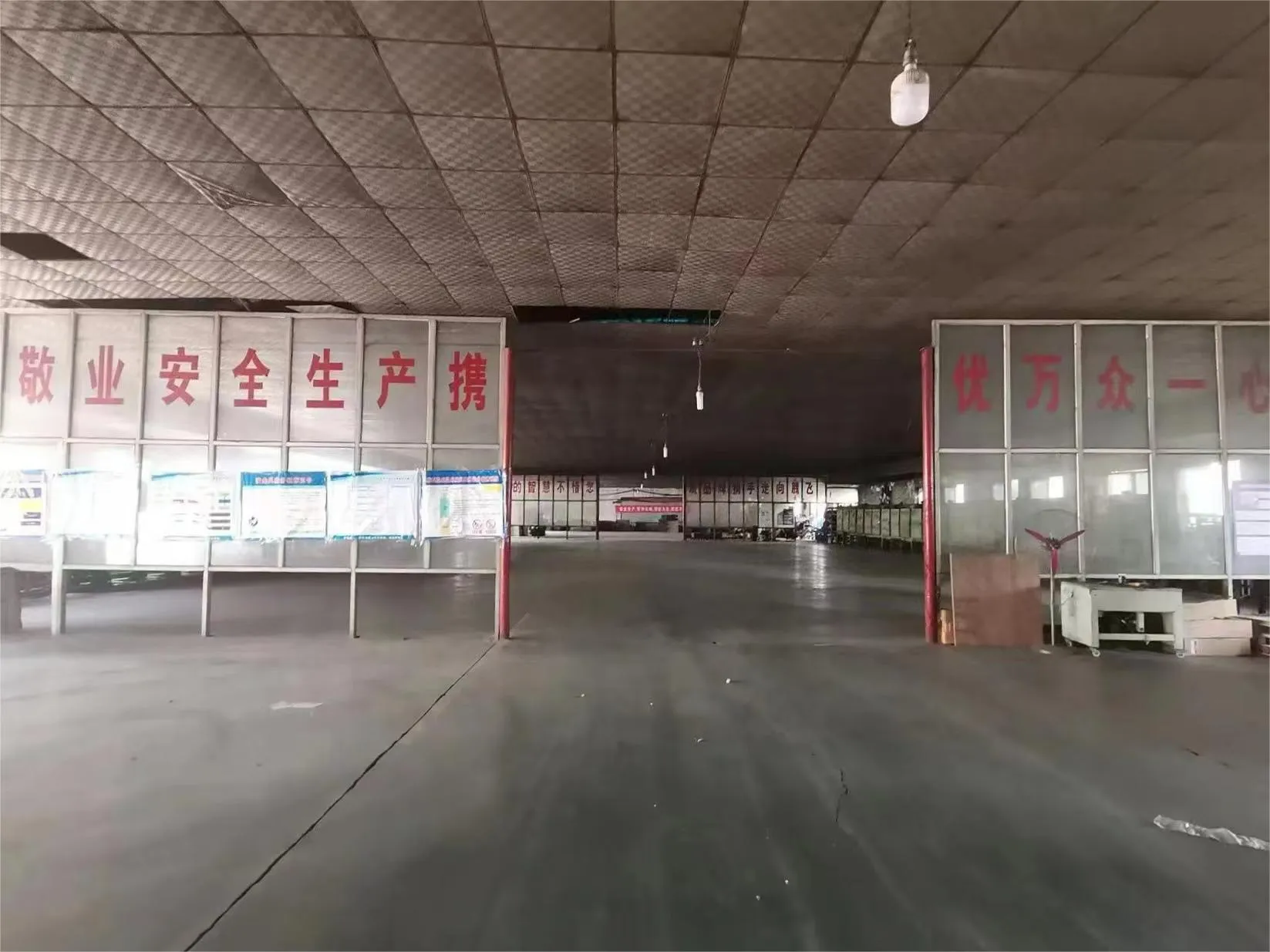
Understanding Different Types of Cast Iron
Before diving into the choice of welding rods, it's important to recognize the various types of cast iron, including gray iron, ductile iron, white iron, and malleable iron. Each type has distinct properties and applications that affect how it is welded. For example, gray iron—commonly used in engine blocks—is often easier to weld compared to white iron, which is highly brittle.
Experience-Based Selection of Welding Rods
From practical experiences shared by seasoned welders, nickel-based rods often emerge as a preferred choice for welding cast iron. Nickel rods, like the EniFe-CI, are renowned for their ability to accommodate cast iron's high carbon content while providing excellent machinability post-weld. Welders often note that while nickel rods are more expensive, they offer superior results that justify the cost.
Another popular rod is the EniFe-CI-A, which contains a higher nickel content, offering even more flexibility and less chance of post-weld cracking. This is particularly beneficial in high-stress applications or when welding different types of cast iron. Real-world examples show successful repairs on components like heavy machinery parts and piping when using these rods.
Additionally, the selection might depend on the welding position and environment. Experienced professionals often recommend preheating components to between 400°F and 600°F, especially for thicker sections, to minimize the risk of thermal shock.
cast iron welding rod name
Expertise in Cast Iron Welding
Professional expertise emphasizes the importance of assessing the application requirements before selecting a welding rod. Experts stress that the welding technique—whether MIG, TIG, or stick welding—determines the rod type. For instance, TIG welding typically demands more precise rod selection to ensure the weld pool isn't contaminated.
Moreover, expert metallurgists often analyze the base metal through microstructural analysis to understand how welding will impact the specific cast iron type. This scientific approach aids in selecting a rod that will not only yield a strong weld but also maintain the structural integrity of the overall component.
Authoritative Insights on Welding Rods
Industry authorities often provide guidelines on the best practices for cast iron welding to ensure that repairs or fabrications meet required safety and quality standards. Standards organizations typically recommend specific rods, such as nickel-iron or pure nickel rods, for their reliability and consistency.
Evaluation criteria such as tensile strength, elongation, and post-weld machinability are vital metrics provided by authoritative entities. Welders are encouraged to follow these guidelines to avoid unforeseen failures over time.
Building Trust through Reliable Welding Practices
Trustworthiness in welding practices is built through transparency and consistent results. Welding professionals emphasize testing weld samples prior to full-scale application, a practice that verifies rod compatibility and weld strength. Documenting welding procedures, the rods used, and the pre-and-post welding treatments ensures that future projects can replicate successful outcomes or troubleshoot effectively, establishing a foundation of trust with clients and peers alike.
In conclusion, selecting the appropriate cast iron welding rod involves understanding the specific demands of the welding project, leveraging professional expertise, and adhering to authoritative guidelines. Through careful consideration and informed choices, welders can tackle the challenges of cast iron, ensuring durable and high-quality welds that withstand the test of time.