Cast iron welding electrode prices have become a topic of significant interest among welding professionals, manufacturing industries, and DIY enthusiasts. Understanding the factors influencing these prices can provide insights into making informed purchasing decisions and optimize welding projects.
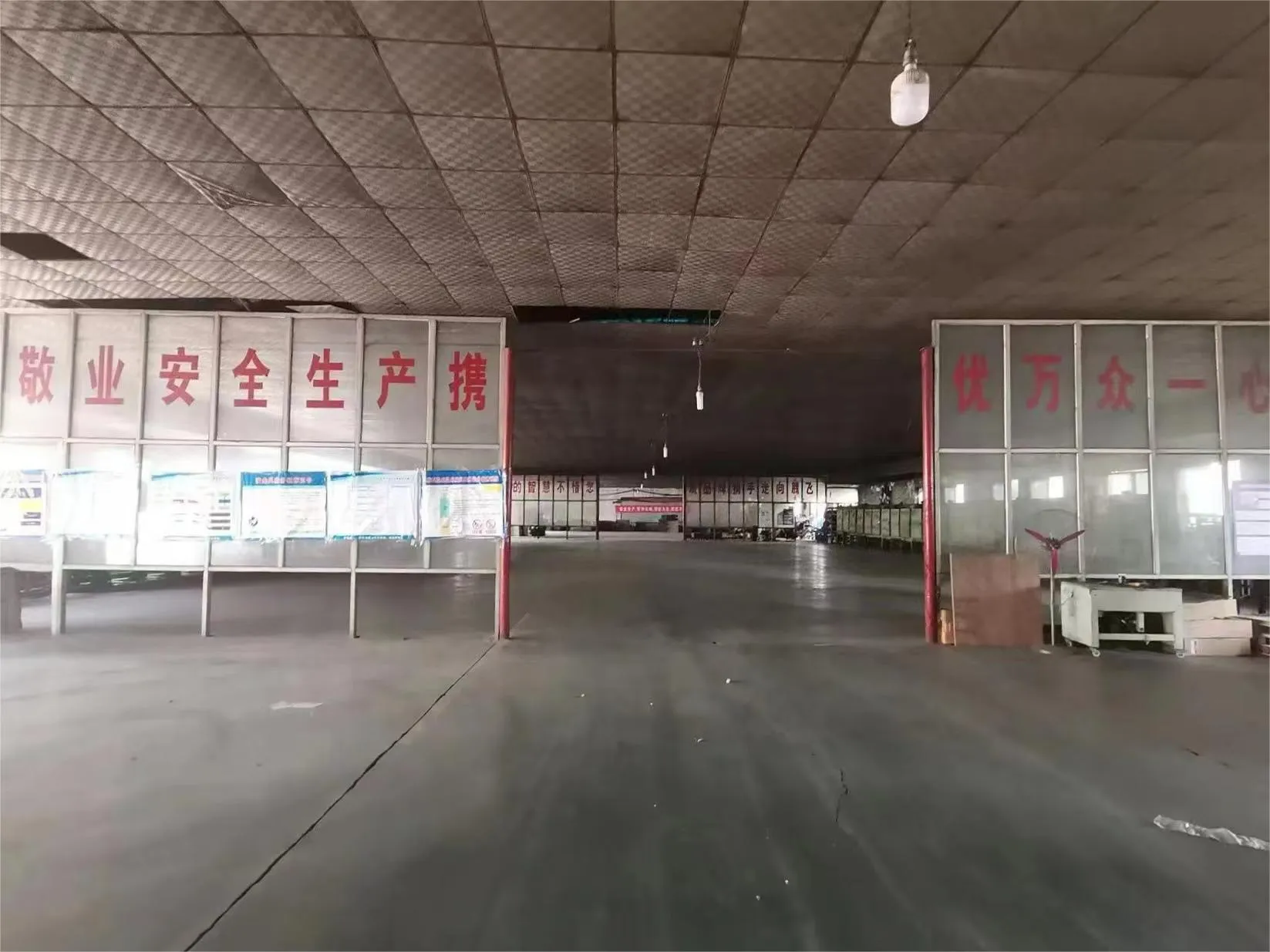
Welding electrodes, specifically designed for cast iron, play a crucial role in the strength and durability of welded joints. Cast iron, with its unique metallurgical structure, requires specialized electrodes to handle its brittleness and ensure strong adhesion. Therefore, the composition, coating, and brand of the electrode significantly impact the price.
Firstly,
the composition of the welding electrode affects its price. Electrodes with a high nickel content are preferred for welding cast iron due to nickel’s ability to handle thermal expansion effectively, minimizing the risk of cracking. These high nickel electrodes generally command a higher price due to the cost of nickel as a raw material and its superior welding performance on cast iron.
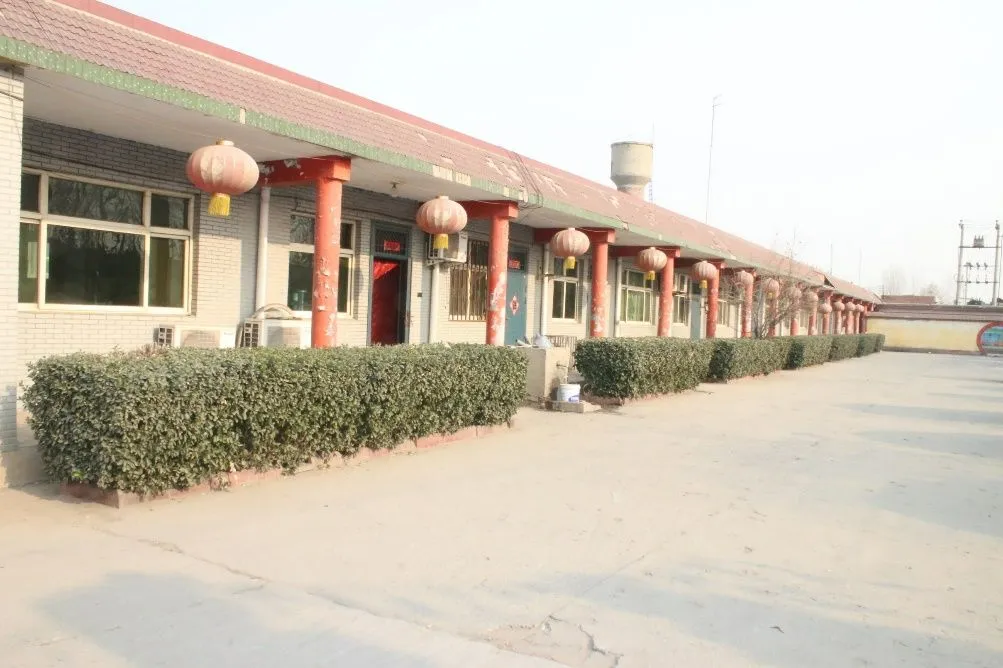
Additionally, the type of coating on the electrode influences pricing. Coatings are engineered to stabilize the arc, offer protection from atmospheric contamination, and add specific characteristics to the weld, such as slag removal properties. Coatings made with higher quality materials or specialized formulations, tailored for specific types of cast iron, are customary in top-tier products. They provide better results but also contribute to higher prices.
Brand reputation and quality also play a significant role. Established and renowned brands in the welding industry often charge a premium for their products due to their proven reliability and performance track record. Brands such as ESAB, Lincoln Electric, and Hobart are known for their high-quality electrodes and stringent manufacturing standards, which justify their price points. These brands offer comprehensive customer support and warranties, further adding value to the purchase.
cast iron welding electrode price
Market demand and supply chain logistics also impact electrode prices. In recent times, fluctuations in raw material availability and increased shipping costs have led to price volatility. Economic factors, such as global trade policies and tariffs, can also influence costs. Staying informed about these dynamics can assist in planning purchases and managing project budgets effectively.
When sourcing electrodes, consider purchasing in bulk, as suppliers often provide discounts for larger volumes, reducing the cost per unit. Moreover, building long-term relationships with suppliers can lead to negotiated rates, especially beneficial for industries with regular high-volume usage.
Ensuring correct storage conditions for welding electrodes is also crucial to maintain their performance quality over time. Moisture and improper storage can deteriorate the electrode coating, leading to suboptimal weld quality. Proper handling and storage preserve the electrode’s integrity, optimizing investment by reducing wastage and maintaining high performance.
Investing in compatible accessories and quality welding machines can further enhance the efficiency and outcome of using high-quality electrodes, ensuring ROI in welding projects involving cast iron. Regular training and certification for welding personnel on the latest techniques and best practices can optimize the use of high-cost electrodes, maximizing productivity and project outcomes.
Ultimately, while the price of cast iron welding electrodes can be higher due to material composition and specialized coatings, the investment is justified by the superior weld quality they provide. Understanding the various factors that influence pricing not only aids in making cost-effective purchasing decisions but also ensures optimal performance and longevity of the welds, securing the overall quality and integrity of any manufacturing or repair project involving cast iron.