Cast iron artifacts are often cherished for their durability and classic appeal, but when it comes to repairing or modifying such items, the process can be challenging due to the unique properties of cast iron. Cast iron welding, specifically using machinable welding electrodes, has become an essential technique for both industrial and small-scale applications. Here, we delve into the intricacies of this process, providing insights that enhance understanding, assure quality, and promote trust.
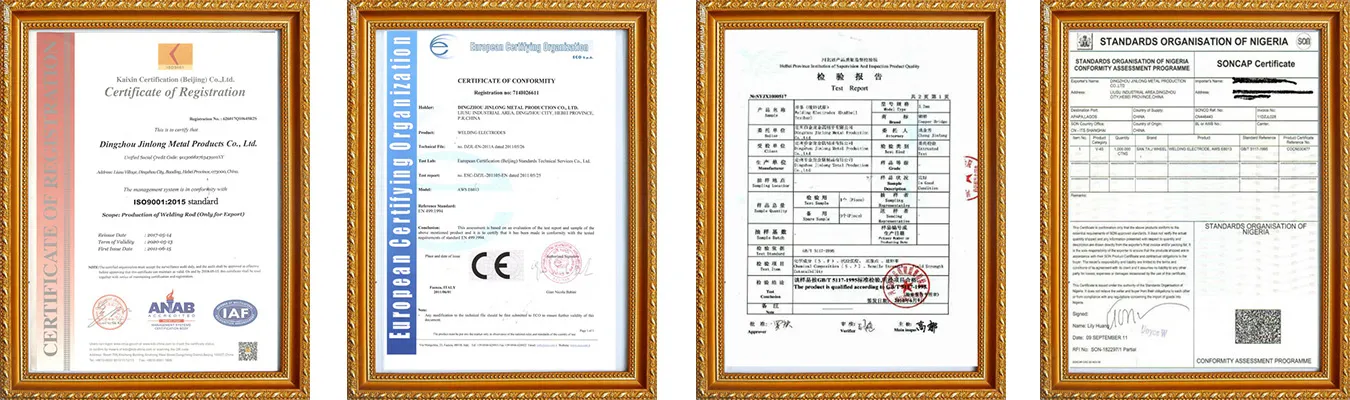
Cast iron is known for its excellent compressive strength yet infamously poor tensile strength, making welding a delicate task. This necessitates the use of specialized welding electrodes designed to address cast iron's brittleness. Machinable cast iron welding electrodes are engineered to fuse seamlessly with the cast iron's granular graphite, minimizing the risks of cracking and ensuring structural integrity post-welding.
One of the primary challenges in welding cast iron is pre-heating. Proper pre-heating of the material to temperatures between 500°F to 1200°F is crucial, as it reduces thermal shock and prevents cracking. This step is fundamental in ensuring the success of the welding process but must be monitored carefully. Excessive heat can lead to warping or altering the composition of the cast iron.
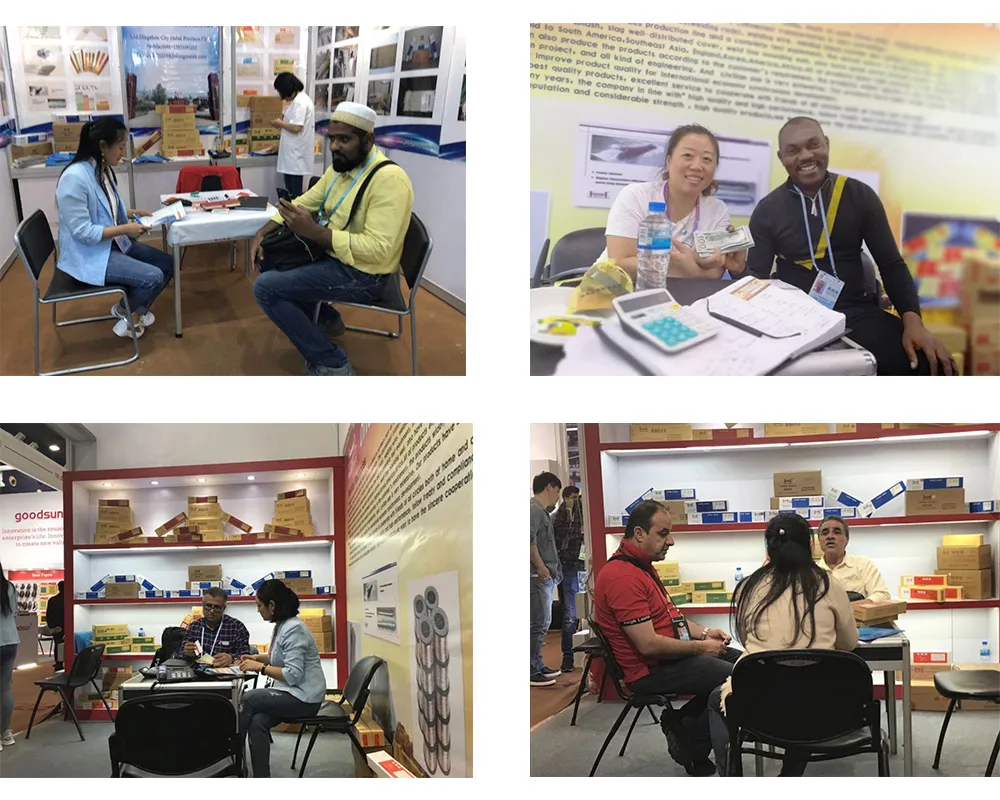
The choice of machinable welding electrodes is pivotal. Electrodes with a high nickel content are favored due to their excellent adaptability to the base material and their ability to produce strong, machinable welds. Nickel-based electrodes provide a weld that can be easily machined, offering flexibility for subsequent fabrication or renovation processes. The machinability factor is critical in applications where precision is paramount, such as in the restoration of engine blocks or vintage cast iron cookware.
Furthermore, the welding technique adopted significantly influences the outcome. Short, controlled welds interspersed with pre-heating and cooling periods reduce internal stresses. This method is crucial in preventing unwanted distortions and ensuring the longevity of the repair. It's recommended to use a stringer bead technique, as it helps in controlling the heat input, thereby reducing the potential for cracks.
Cooling is just as important as pre-heating. Controlled cooling, often achieved by burying the welded piece in insulating materials like sand or slow-cooling within a furnace, helps in maintaining the stability of the weld and the surrounding material. This gradual cooling process prevents rapid contraction and the resultant stresses that can cause fractures.
cast iron welding electrode machinable
Another aspect to consider is post-weld machining. The machinability of the weld is essential, and machinable electrodes allow for this without the risk of chipping or damaging tooling. Post-weld operations may include grinding, drilling, or milling to achieve the desired finish or fit. This capability ensures that repairs not only restore functionality but also meet original design specifications.
The expertise required in cast iron welding using machinable electrodes cannot be overstated. Professionals undertaking such projects must have a thorough understanding of material science, welding techniques, and post-weld finishing processes. Training and certification in welding are indicators of trustworthiness and authority, and consumers are encouraged to seek services from accredited professionals or companies.
In industries such as automotive restoration, industrial machinery maintenance, and culinary equipment refurbishment, the ability to perform trustworthy and long-lasting repairs on cast iron using machinable electrodes is invaluable. It not only extends the life of the items but also maintains their historical value and functional aesthetics.
Finally, it's important to recognize that not all cast irons are created equal. Variations in alloy composition, casting methods, and original intended use can affect how the material responds to welding. Understanding these nuances underscores the importance of expertise in selecting the appropriate electrode and technique for each unique project.
In conclusion, mastering the use of machinable cast iron welding electrodes combines a deep understanding of material properties, precision in technique, and a commitment to quality outcomes. It reaffirms the integrity of cast iron items and reflects the meticulous craftsmanship required in their repair and maintenance. Through informed choice and skilled execution, machinable welding electrodes offer a reliable solution for bringing new life to old iron.