Exploring the Nuances of Cast Iron Gas Welding Rods A Comprehensive Guide for Professionals
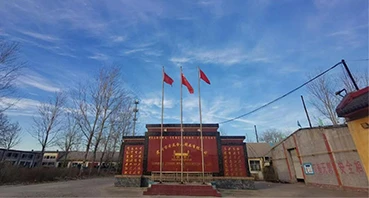
Cast iron, with its distinctive properties and long-standing role in various industries, presents unique challenges in welding. One of the pivotal aspects of cast iron welding is the choice of welding rods, particularly when employing gas welding techniques. This article delves into the intricacies of cast iron gas welding rods, offering insights backed by years of industry expertise.
Understanding the Properties of Cast Iron
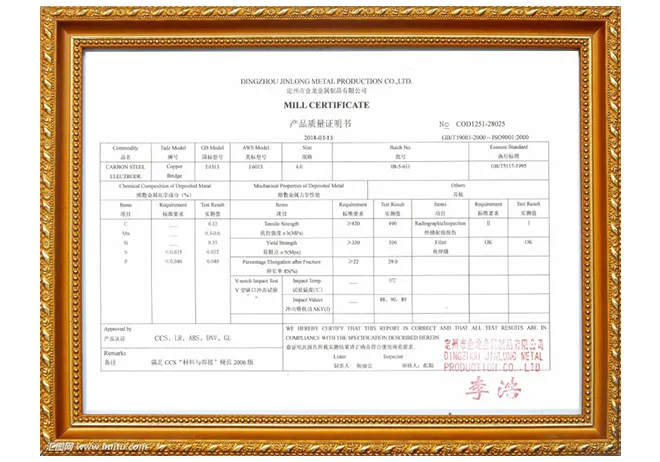
Cast iron is renowned for its high carbon content, which gives it excellent castability and machinability, yet poses challenges in welding due to its brittle nature. During welding, the localized heating can lead to the formation of hard and brittle structures in the heat-affected zone. Therefore, selecting the appropriate welding rod is crucial to minimizing these issues.
The Role of Gas Welding in Cast Iron Applications
Gas welding, using oxygen and acetylene as a fuel source, remains a preferred method for certain cast iron applications due to its ability to provide a controlled heat input. This method is particularly valued for its portability and simplicity, making it ideal for repair and maintenance work on cast iron materials.
Choosing the Right Cast Iron Gas Welding Rod
The effectiveness of gas welding on cast iron significantly depends on the welding rod used. The right welding rod should ideally complement the composition of cast iron, ensuring a durable bond while minimizing any negative impacts on the material.
Nickel-Based Rods Among the most recommended for cast iron gas welding, nickel-based rods offer ductility and superior tensile strength. These rods adapt well to the thermal Cycle of cast iron, reducing the likelihood of cracking.
Copper-Nickel Rods While not as common as nickel rods, copper-nickel alloys can be an excellent choice for certain applications, providing enhanced resistance to corrosion and wear, crucial for industrial settings where longevity is a concern.
cast iron gas welding rod
Technique and Application
Mastery in using cast iron gas welding rods comes with an understanding of both pre-heating and slow cooling techniques. Pre-heating the cast iron before welding minimizes the thermal shock, which is a common precursor to cracking. Similarly, controlling the cooling process ensures the weld area does not cool too quickly, helping prevent stress fractures.
Industry-Proven Best Practices
Through extensive field experience, industry experts advocate for a methodical approach to cast iron gas welding
- Clean the Surface Ensure the cast iron surface is free of oils, rust, and other contaminants. Any impurities can compromise the quality of the weld.
- Control Heat Input Maintain a steady flame and uniform motion to distribute heat evenly across the joint.
- Layered Welding When dealing with thicker sections, apply the weld in layers to allow for even heat distribution and reduce the potential for stress.
The Importance of Continuous Learning
In a field characterized by continuous innovation, welders must stay updated with the latest advancements in welding technologies and techniques. Participation in workshops and training sessions can enhance expertise, leading to more effective use of gas welding rods and improved outcomes in cast iron applications.
Building Authority and Trust
A welder's reputation is built on reliability, efficiency, and precision. By mastering the nuances of cast iron gas welding rods and adhering to best practices, welders can cultivate trust with clients, ensuring their projects are executed with the highest standards of quality and safety. Equipment calibration, adherence to safety protocols, and a commitment to delivering consistent results are pivotal in establishing this trust.
For professionals engaged in cast iron welding,
the selection and use of the appropriate gas welding rods are crucial. Aligning technical expertise with practical experience can turn potential challenges into opportunities for innovation and excellence in the field of metalwork.