Exploring the Landscape of Cast Iron Electrode Specifications for Enhanced Performance
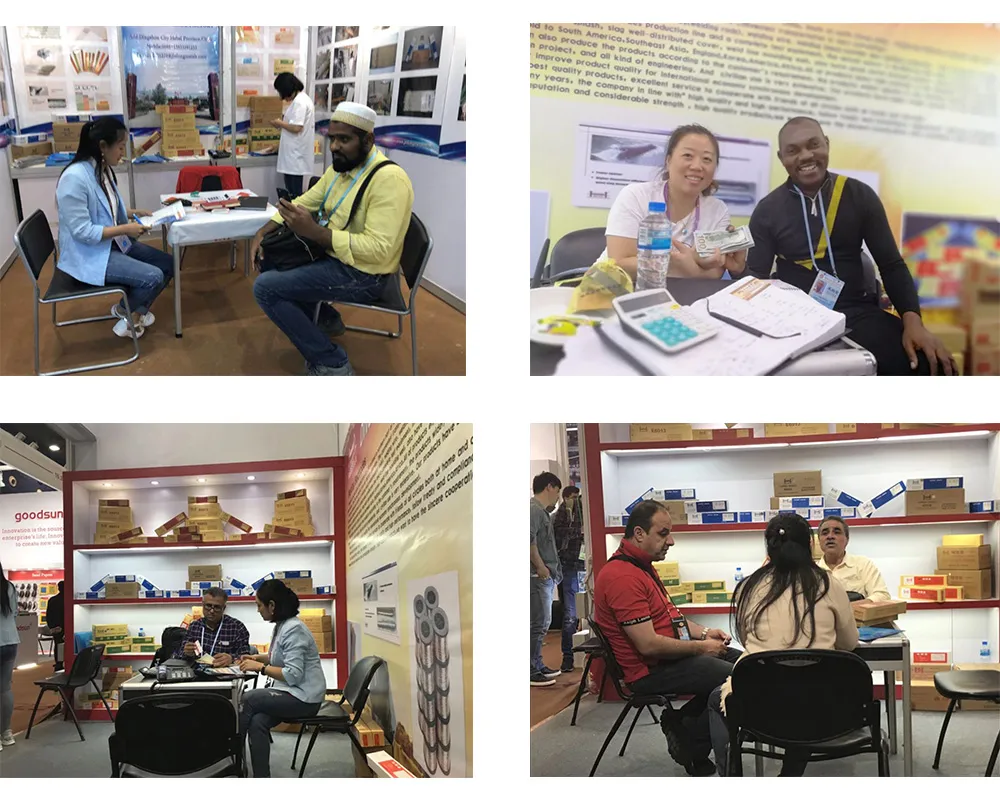
In the intricate world of welding and metallurgy, cast iron electrodes hold a pivotal role. Their unique characteristics and specifications necessitate a meticulous approach in selection and application to ensure optimal outcomes in various industrial scenarios. Understanding the nuanced specifications of cast iron electrodes can lead to improved welding performance, enhanced joint strength, and increased durability of joints, positioning these components as indispensable in the realm of material joining technologies.
Cast iron, known for its brittleness and complex metallurgical structure, poses distinct challenges during welding. The correct choice of electrodes can mitigate common issues such as cracking and ensure compatibility with different cast iron grades. Electrode specifications, including chemical composition, coating type, and diameter, are critical factors influencing the success of welding operations.
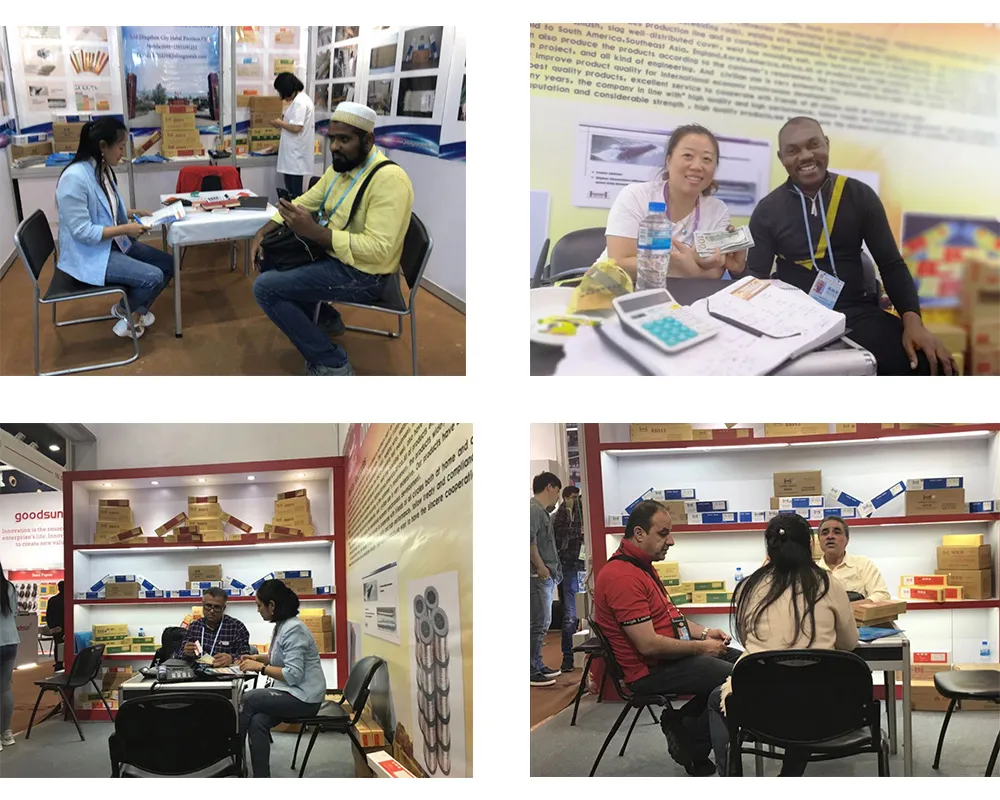
Essentially,
the composition of the electrode plays a crucial role. High-nickel electrodes, for example, are often recommended for their excellent fusion characteristics and the ability to produce a ductile and machinable weld. These electrodes typically boast a nickel concentration above 90%, making them suitable for cold welding where preheating and post-heating are minimized. This specificity ensures minimal risk of thermal cracking, a common issue when working with cast iron.
Electrode coating is another specification dimension that warrants attention. Coatings act as arc stabilizers and protect the molten weld pool from atmospheric contamination. For cast iron electrodes, coatings designed to produce a stable arc and minimize slag inclusion are vital. Basic coatings, which contain calcium fluoride and other stabilizing compounds, are often favored for cast iron applications due to their ability to provide a clean, manageable slag and stable arc.
cast iron electrode specification
The choice of electrode diameter impacts penetration depth and weld bead formation. Smaller diameters offer precision in delicate cast iron components but require skilled handling to maintain consistent arc quality. Conversely, larger diameters can handle heavier work but may necessitate preheating in certain situations to prevent thermal shock to the base material.
In practice, the expertise required to match electrode specifications with specific cast iron grades and welding conditions underscores the need for professional judgment and hands-on experience. Welders must consider factors such as the thickness of the material, the complexity of the shape, and the working position. A tailored approach, informed by continuous learning and adaptation, ensures that each welded joint meets performance expectations in both strength and durability.
Authoritative guidance from manufacturers and seasoned welding professionals contributes significantly to this knowledge pool. Manufacturer documentation often provides detailed insights into the optimal conditions and techniques for using specific electrodes. Meanwhile, knowledge sharing among industry insiders and constant updates on technological advancements foster an environment of trustworthiness and reliability.
The trustworthiness of a cast iron electrode's performance is often judged by its compliance with established standards and certifications. Renowned organizations such as the American Welding Society (AWS) offer certifications that assure users of the quality and reliability of electrode specifications. Compliance with these standards ensures that electrodes deliver consistent results, bolstering confidence in their use across varied applications.
In summary, the intricate nature of cast iron welding demands a comprehensive understanding of electrode specifications. By emphasizing chemical composition, coating type, and diameter, industry professionals can make informed decisions that enhance welding quality and performance. The synergy between experience, expertise, authoritative guidance, and trustworthiness ensures that cast iron electrodes continue to play a vital role in material joining and structural integrity across myriad industries.