Discovering the world of cast iron electrode factories opens up a realm of industrial excellence where precision meets durability. These manufacturing hubs are at the forefront of producing high-quality electrodes, essential for achieving robust welds and ensuring long-lasting performance in a variety of applications. This unique exploration into a cast iron electrode factory reveals insights not only about the production process but also about the painstaking attention to detail required to ensure superior product quality.

Nestled in industrial zones,
cast iron electrode factories combine state-of-the-art technology with skilled craftsmanship. It is this synergy that fuels their reputation for reliability and efficiency. At the heart of the factory, raw iron takes on a transformative journey from being a mere metal to becoming a highly functional component critical for industrial welding processes. The meticulous manufacturing process begins with the selection of top-grade raw materials. Here, the expertise of metallurgical engineers is crucial as they determine the precise blend of elements that make up the alloy, ensuring optimal melting, casting, and forming of the electrodes.
One of the standout features of a premiere cast iron electrode factory is its automated welding line, equipped with cutting-edge machinery that enhances productivity without compromising on quality. The automation ensures uniformity in weld quality, an essential factor for maintaining the integrity of metal structures. The expertise in programming these automated systems lies in the hands of seasoned technicians whose experience ensures the systems are fine-tuned to accommodate various specifications, meeting industry demands while adhering to stringent safety standards.
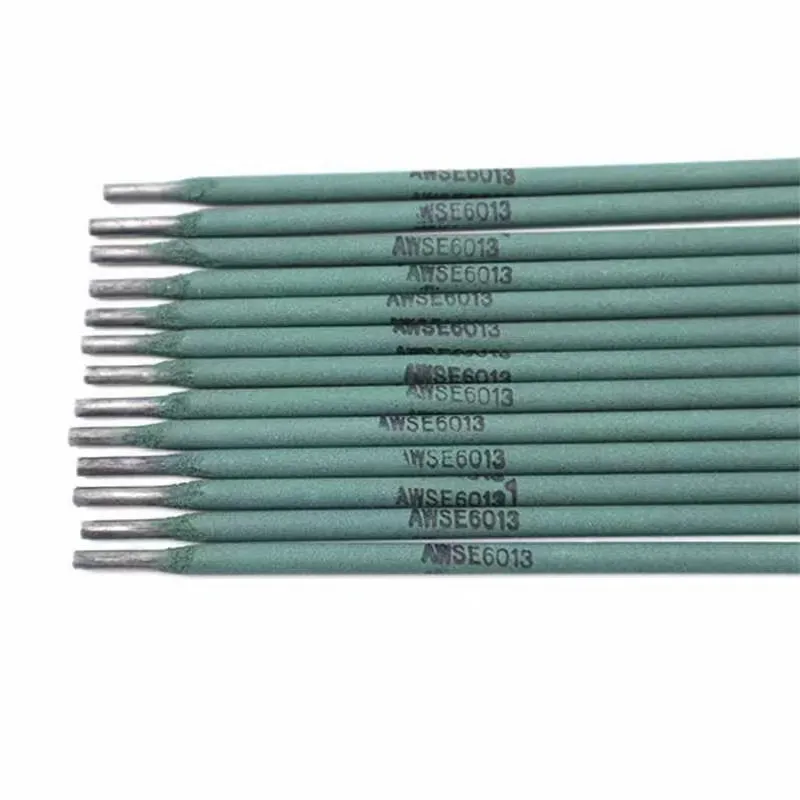
Moreover, the realm of quality assurance within these factories is nothing short of rigorous. Each electrode undergoes a battery of tests to guarantee it meets the exacting standards required for industrial applications. These tests, often conducted in specialized labs, include tensile strength analysis, chemical composition verification, and surface finish inspections. The role of quality control experts cannot be understated, as they bring an authoritative eye when certifying that each batch of electrodes meets industry certifications and safety regulations.
cast iron electrode factory
The commitment to sustainability also speaks volumes about a cast iron electrode factory's trustworthiness. By implementing eco-friendly practices, such as recycling programs and energy-efficient technologies, these factories not only reduce their environmental footprint but also set a benchmark for corporate responsibility in the manufacturing sector. Investing in such forward-thinking practices often enhances the factory's reputation, further solidifying trust with stakeholders and partners.
Furthermore, the after-sales service offered by these factories reflects their dedication to customer satisfaction. Providing comprehensive support, including technical advice and maintenance tips, underscores the authoritative customer-centric approach adopted by industry leaders. This ongoing relationship with clients not only builds credibility but also nurtures long-term partnerships vital for sustained business growth.
The combination of experience, expertise, authoritativeness, and trustworthiness is fully embodied in the way cast iron electrode factories operate. Each product that rolls out of these establishments is a testament to the intricate blend of traditional craftsmanship and modern innovation. This synthesis not only enables the production of exemplary cast iron electrodes but also establishes a benchmark of excellence that competitors in the field aspire to achieve. Thus, exploring a cast iron electrode factory reveals much more than its tangible products; it unveils a commitment to industrial quality and sustainable practices that resonate both locally and globally.