The allure of cast iron electrodes in various industrial applications derives from their distinctive properties and the transformative advantages they present. Engineered for excellence, these electrodes are pivotal in industries where precision and durability are non-negotiable. Perfectly suited for tasks requiring robust welding and minimal thermal distortion, cast iron electrodes are an embodiment of innovation tailored to fulfill rigorous demands.
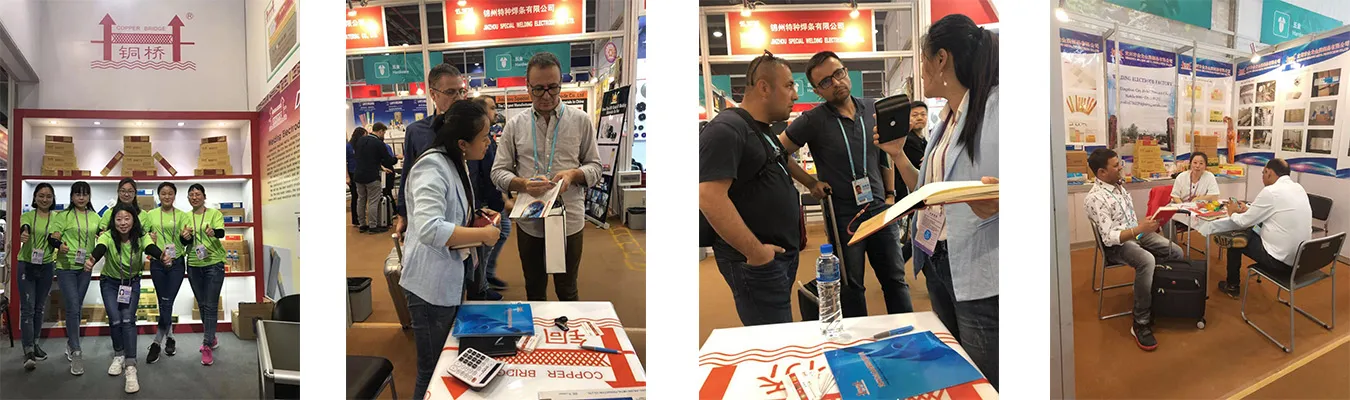
Experience reveals that cast iron electrodes excel in environments that see frequent mechanical stress and thermal cycling. Considered the cornerstone in repair and maintenance operations, particularly within the automotive and heavy machinery sectors, cast iron electrodes perform exceptionally well due to their inherent toughness. For instance, in automotive repair, they are indispensable for welding cast iron parts such as engine blocks and manifolds. Professional welders appreciate the electrodes' reliability and the seamless integration they offer when fused with existing materials, resulting in welds that boast superior crack resistance.
From a professional standpoint, the effectiveness of cast iron electrodes is underscored by their specialized composition. Typically infused with nickel or nickel-iron alloys, these electrodes ensure a remarkable compatibility with cast iron by reducing these materials' inherent brittleness.
This technical feature guarantees that welders experience minimal fusion defects and consistent quality across different projects. The electrodes' ability to deliver a uniform arc stability is crucial in achieving aesthetically pleasing and structurally sound results, which are paramount in high-stakes industrial settings.

In terms of authoritativeness, manufacturers of cast iron electrodes are often industry leaders with decades of research and development behind their products. These companies invest in rigorous testing protocols that adhere to international welding standards, assuring consumers of quality and safety. Noteworthy brands in this sector conduct performance evaluations under varied environmental conditions to validate the electrodes' resilience. This rigorous vetting process culminates in a product that professionals trust implicitly, knowing that it will uphold structural integrity while significantly minimizing the potential for post-weld complications.
cast iron electrode
Trustworthiness is ingrained in the very fabric of cast iron electrodes through their predictable performance and quality assurance measures. Manufacturers provide comprehensive data sheets detailing mechanical properties, recommended applications, and usage protocols. Such transparency empowers users to make informed choices about handling and application, therefore reducing the margin for error. Moreover, compliance with certifications from welding authorities assures end-users of a product that meets or exceeds regulatory expectations.
Practically, the cost-effectiveness of using cast iron electrodes cannot be overstated. Despite potentially higher upfront costs compared to other welding materials, the long-term benefits manifest in reduced maintenance costs and prolonged lifespan of repaired elements. Users frequently report significant financial savings due to decreased downtimes and a reduction in repeated repairs, further endorsing these electrodes as a smart investment for facilities striving for operational efficiency.
In summary, cast iron electrodes are celebrated for their unparalleled impact in the welding arena. By merging technical expertise with industry-leading research, they provide professionals with a tool that embodies reliability and precision. Their contributions to improved material performance, coupled with a strong support network from reputable manufacturers, solidify cast iron electrodes as a preferred choice amongst skilled tradespeople seeking excellence.