Choosing the right welding rods is pivotal in ensuring the structural integrity and longevity of any construction. Among the various options, carbon steel welding rods stand out as a popular choice for many industry professionals. With years of experience in the field of welding, I've encountered countless situations where understanding the nuances of these rods can make a significant difference in project outcomes.
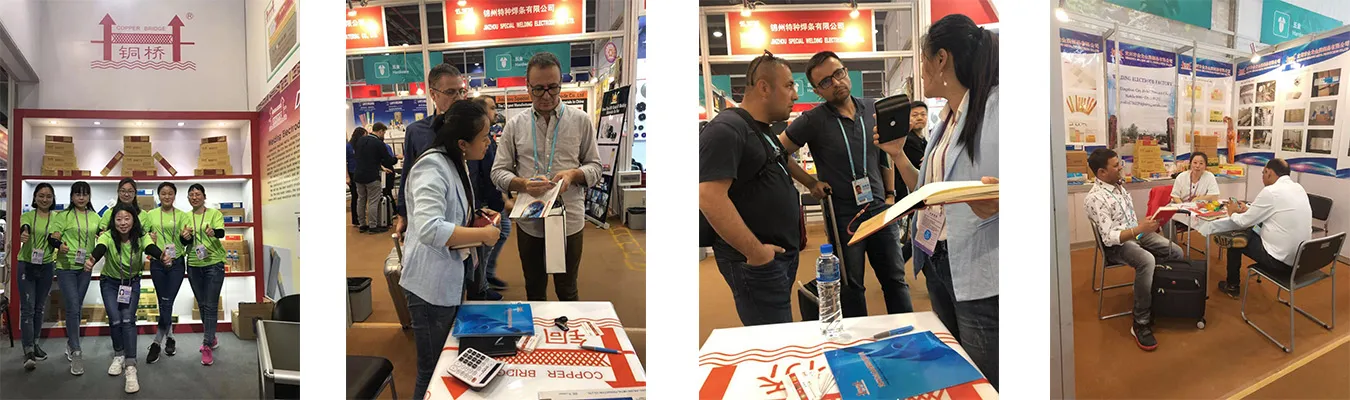
Carbon steel welding rods are particularly known for their versatility and robustness. They are widely employed in construction, automotive repairs, and industrial fabrication due to their strength and durability. When working with carbon steel welding rods, one can expect excellent results, provided the rods are chosen and employed correctly. For instance, they are ideal for projects that demand a strong weld that can withstand considerable stress and pressure.
One crucial aspect to consider when using carbon steel welding rods is their compatibility with the base material. It's essential to ensure that the rod's composition complements the metals being welded. Misalignment in this regard can lead to weak joints that could compromise the entire structure's safety. This makes carbon steel welding rods particularly fitting for projects involving carbon and low-alloy steels.
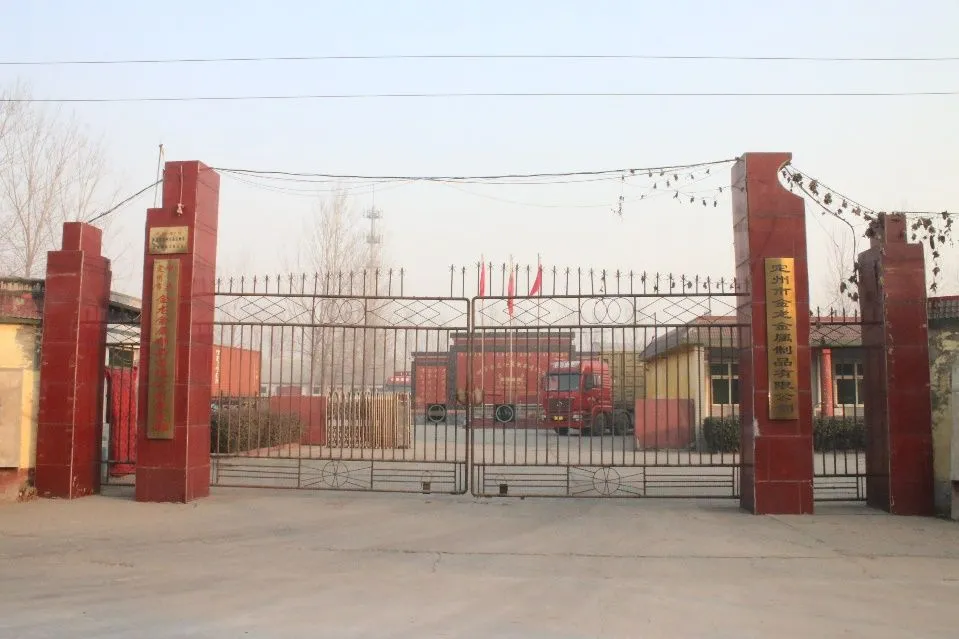
From an expert's viewpoint, selecting the right type of carbon steel welding rod requires an understanding of their classifications. Common types include E6010, E6011, E6013, E7018, each with specific characteristics suited for different applications. For example, E6010 rods are favored for their deep penetration and are often used in pipe welding. In contrast, E7018 rods are designed for high-strength welds, providing excellent ductility and impact properties, making them suitable for critical applications like pressure vessels.
carbon steel welding rods
The electrode's coating is another factor that professionals must consider. The coating not only influences the arc's stability but also impacts factors like slag formation and weld bead appearance. For optimal results, it's vital to follow the manufacturer's guidelines for storage and handling, as moisture can detrimentally affect the rod's performance, leading to defects such as weld porosity.
Trust plays a crucial role when discussing welding materials. Reliable suppliers who provide quality carbon steel welding rods can make a significant difference in achieving successful project outcomes. Professionals often prioritize suppliers with a proven track record, certifications, and compliance with industry standards. This ensures they are investing in products that have passed rigorous quality control checks.
To share a personal experience, a project I managed involved fabricating large steel frameworks. We opted for E7018 carbon steel welding rods due to their superior tensile properties and low hydrogen content, ensuring weld integrity over long-term usage. Despite challenging weather conditions that could have affected the rods' performance, our adherence to proper storage protocols safeguarded the rods' effectiveness, leading to a successful completion without structural issues.
In conclusion, embracing the nuances of carbon steel welding rods is crucial for any professional in the welding industry. Understanding the intricacies of choosing the correct rod type, adhering to proper handling and storage practices, and selecting credible suppliers enhances the quality and reliability of welds. As a dedicated advocate for excellence in welding, I emphasize the importance of continuous learning and adaptation to new technologies and materials to maintain the highest standards in any welding endeavor.