In the realm of industrial fabrication and construction, the choice of welding electrodes can make or break the quality of your project.
Carbon steel welding electrodes, known for their versatility and strength, have become indispensable tools in the welding industry. Drawing from years of hands-on experience and deep-rooted expertise, let’s delve into why these electrodes are often the go-to choice for many professionals seeking robust, high-quality welds.
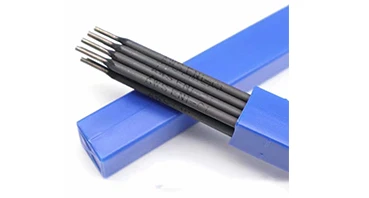
Carbon steel welding electrodes are favored particularly for their adaptability across a multifarious range of welding applications. From routine repairs to major construction projects, these electrodes can handle it all. Their unique composition allows them to join dissimilar metals effectively, thereby reducing material costs and enhancing project efficiency. One key feature is their ability to produce a clean and stable arc, essential for precision welding tasks.
In terms of technical specifications, these electrodes are typically composed of a mild steel core wire with a baked-on coating of flux material. This precise formulation is crucial as it impacts the welding arc and bead formation quality. The flux coating has a multifunctional role it stabilizes the arc, shields the molten puddle from atmospheric contamination, and enhances the mechanical properties of the weld. This becomes critical in environments where the integrity of the weld needs to withstand high levels of stress and strain.
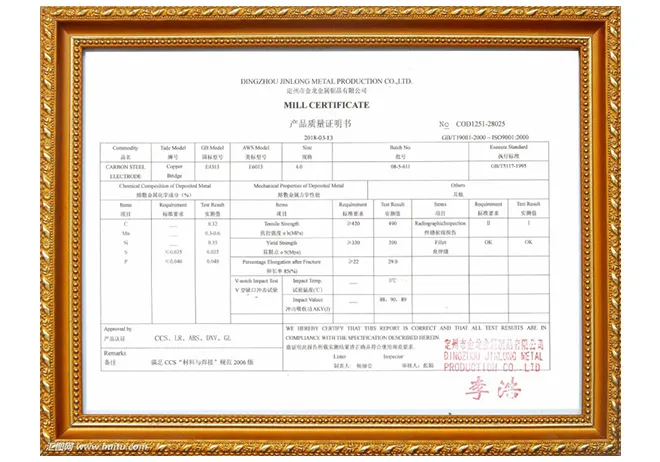
Expert welders often emphasize the importance of selecting the right type of carbon steel electrode for the job. For instance, electrodes classified under E6010 or E7018 each offer distinct advantages. E6010 electrodes are renowned for their deep penetration capabilities, making them ideal for welding through rust or paint and on pipes or structural steel. In contrast, E7018 electrodes provide a smooth, stable arc and are often chosen for high-strength welding where ductility and toughness are paramount.
carbon steel welding electrodes
Furthermore, authoritative knowledge in welding involves understanding the ideal operating parameters for carbon steel electrodes. Factors such as amperage, electrode angle, and speed all influence the quality of the weld. Welding at too low an amperage can result in poor fusion and an irregular bead, while too high an amperage might lead to excessive spatter or burn-through. Thus, fine-tuning these parameters based on the electrode size and project requirements can significantly enhance weld quality and appearance.
With advancements in technology, the development of carbon steel welding electrodes has evolved, incorporating better flux compositions and core wire technologies to meet contemporary challenges. High-quality manufacturers are now providing electrodes that minimize fume emissions, catering to safety-conscious projects that prioritize worker health and environmental sustainability.
Drawing insights from industry trends, it’s apparent that the demand for high-performance carbon steel electrodes is only set to grow. Professionals inclined towards sustainability now look for electrodes that are not only efficient but also environmentally friendlier. As such, manufacturers are prompted to innovate and develop products that align with these expectations.
In conclusion, carbon steel welding electrodes are not just an accessory in welding; they are a foundational aspect that ensures the structural integrity and overall success of the welding project. With continued innovation and development, these electrodes will undoubtedly continue to play a pivotal role in the welding industry. Whether you’re a seasoned professional or a novice welder, understanding the nuances of carbon steel electrodes can lead to better project outcomes and more satisfied clients. Trust in the process, invest in quality materials, and stay informed on the latest in electrode technology to excel in your welding endeavors.