Carbon steel pipe welding is a crucial procedure in various industries due to its versatility, strength, and cost-effectiveness. However, welding carbon steel pipes requires precision, knowledge, and experience to ensure the highest quality and durability. This article presents expert insights and authoritative guidance on carbon steel pipe welding, emphasizing vital techniques and considerations for professionals seeking excellence in their welding projects.
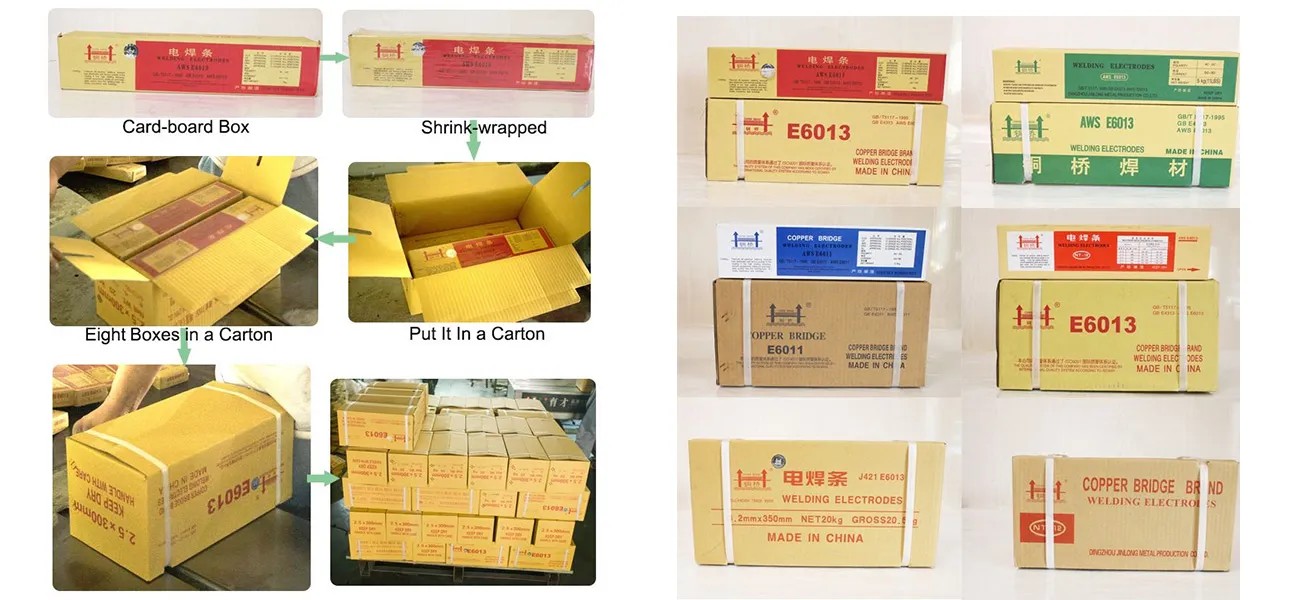
Firstly, the selection of welding techniques forms the foundation of a successful carbon steel pipe welding project. The two predominant techniques used are shielded metal arc welding (SMAW) and gas tungsten arc welding (GTAW). SMAW, often known as stick welding, is favored for its simplicity and cost-effectiveness.
It is particularly effective for thicker pipes due to its deep penetration. On the other hand, GTAW, or TIG welding, is preferred for its precision, offering excellent control over the weld pool, and is ideal for thinner materials and achieving high-quality welds.
Material preparation is a crucial step in carbon steel pipe welding. Proper surface cleaning is essential to avoid contamination, which can lead to weld defects such as porosity or inclusions. Tools like angle grinders or wire brushes are employed to clean the surface of the pipes, ensuring they are free from rust, paint, or any debris. Additionally, proper alignment and joint preparation, including beveling the edges, play a significant role in enhancing the weld quality and strength.
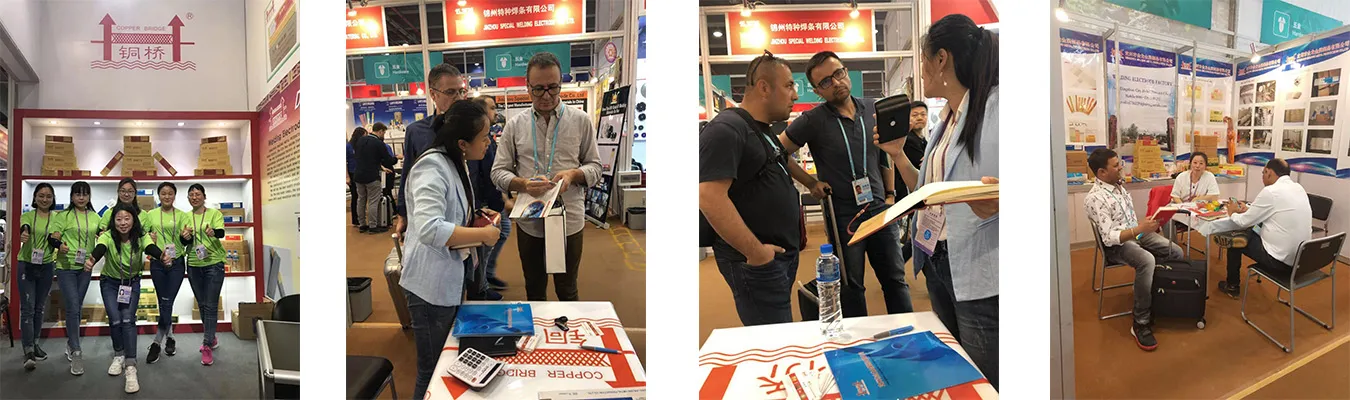
Preheating the carbon steel pipes is often recommended, particularly for high-carbon equivalents or thicker materials. Preheating helps to reduce the thermal gradient between the weld area and the surrounding metal, thereby minimizing the formation of cracks. It's imperative to monitor the temperature closely to ensure consistency, usually at a range of 100°C to 200°C, depending on the carbon content and thickness of the pipe.
Welding parameters significantly impact the outcome of the welding process. The choice of parameters, such as current, voltage, and travel speed, should be based on the pipe's thickness and position. Generally, a lower current is used for root passes, with increased current for fill and cap passes. This ensures deep penetration and adequate fusion between the weld and the base metal. Adjusting these parameters precisely requires extensive experience and understanding of the welding dynamics involved in carbon steel pipe welding.
carbon steel pipe welding
Post-weld heat treatment (PWHT) is another critical factor, particularly for high-strength carbon steel alloys. PWHT relieves residual stresses imparted by the welding process and can enhance the weld's toughness and ductility. The decision to implement PWHT should consider the pipe's intended application, material properties, and any potential exposure to cyclic stresses.
The welding environment must also be controlled diligently to avoid problems like hydrogen-induced cracking. Welders should ensure a dry and conditioned environment, using rod ovens to keep electrodes at optimal temperature and humidity conditions. Moreover, protecting the weld area from drafts or rapid cooling is vital to prevent the occurrence of weld defects.
Quality assurance is pivotal in carbon steel pipe welding. Non-destructive testing methods such as ultrasonic testing (UT) or radiographic testing (RT) are employed to inspect weld quality without causing damage. These methods can detect internal weld defects, such as lack of fusion or porosity, ensuring the weldment's integrity and reliability.
In conclusion, authoritative knowledge and expertise in carbon steel pipe welding are essential for achieving high-quality and durable welds. By selecting appropriate techniques, preparing materials diligently, controlling welding parameters, and implementing rigorous quality checks, welding professionals can ensure their work meets the industry's highest standards. Trustworthiness in welding processes not only ensures structural integrity but also enhances the overall safety and performance of the welded components in their respective applications.