Navigating the landscape of carbon steel electrode classification can be a daunting task, yet having a comprehensive understanding is crucial for optimizing product performance in varied industrial applications. The key lies in knowing the nuanced classifications and selecting electrodes that can maximize operational effectiveness.
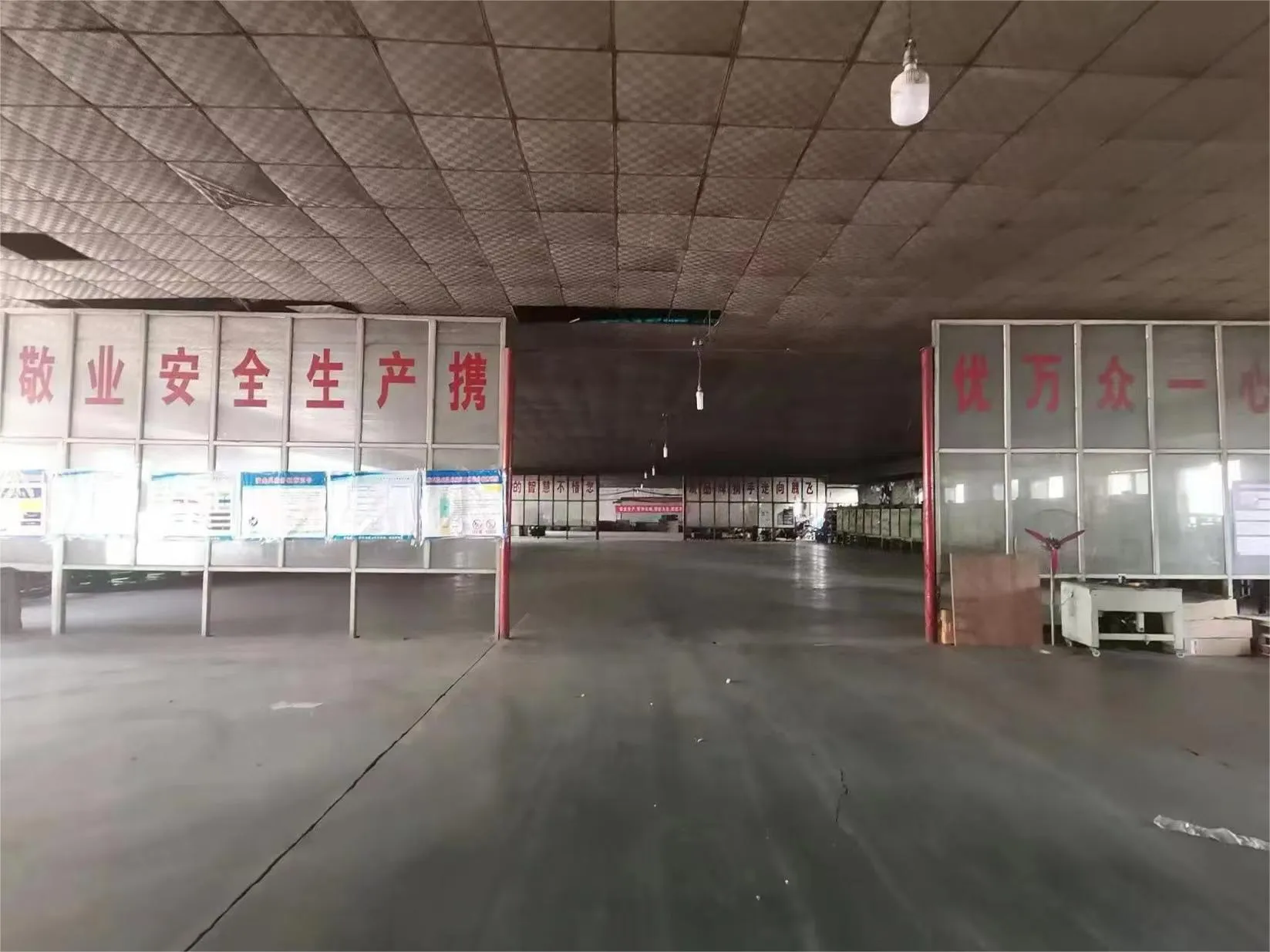
Carbon steel electrodes are primarily used in welding operations, acting as conductive materials that facilitate high-quality, durable welds. They are typically categorized by their chemical composition, mechanical properties, and intended use. One commonly used classification system is the American Welding Society (AWS) specification, which provides a standardized framework for electrode categorization based on detailed criteria.
The AWS classification system uses a series of letters and numbers to denote specific properties of electrodes. For instance, E6010 can be broken down into E for electrode, with subsequent digits indicating tensile strength, welding position capability, and other characteristics. This structured approach allows engineers and procurement specialists to make informed decisions based on specific project requirements.
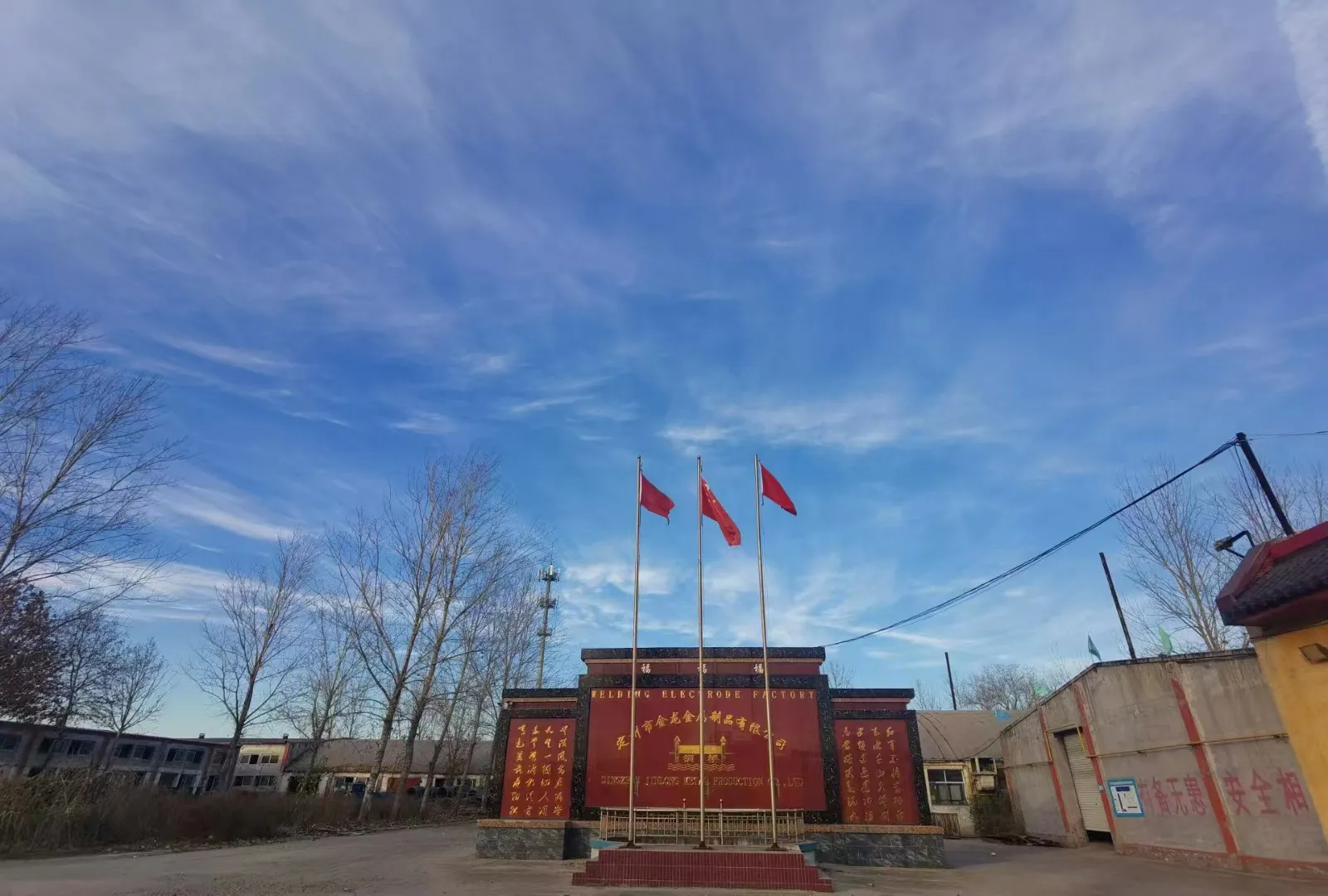
Experience in the field has shown that selecting the right carbon steel electrode is not merely about deciphering codes. The contextual application, such as the working environment, materials being welded, and the required strength of the weld, plays a significant role in decision-making. For instance, electrodes with higher tensile strength are favored in heavy-duty industrial applications like shipbuilding, where robustness is paramount.
carbon steel electrode classification
Expertise in electrode properties also underscores the importance of understanding flux types, as these can greatly affect both the welding process and final weld quality. Flux is imperative in stabilizing the arc and shielding the base metal from atmospheric contamination. In complex projects where precision and quality are critical, such as aerospace or automotive construction, using the right flux-covered electrode can significantly enhance the outcome.
Authoritativeness in carbon steel electrode classification is further enhanced through ongoing research and development. Leading manufacturers continuously innovate to produce electrodes that meet evolving industry standards and specific consumer needs. Professionals often rely on authoritative sources such as AWS publications and technical datasheets from reputable manufacturers to guide their choices.
Trustworthiness in electrode selection is fortified through rigorous testing and adherence to industry standards. Users depend on third-party endorsements, certifications, and field-test results to ensure that electrodes meet promised specifications. Trust is built upon consistent product performance and verifiable adherence to advertised qualities, essential for maintaining credibility in high-stakes projects.
In conclusion, mastering carbon steel electrode classification involves a delicate balance of understanding coded specifications, leveraging real-world application experiences, integrating expert knowledge, and trusting in proven industry standards. By maintaining a clear focus on these elements, businesses can ensure that they select electrodes that not only meet but exceed operational demands, thereby optimizing both productivity and weld quality in their industrial operations.