Welding carbon pipes is a specialized skill that requires a deep understanding of the materials and techniques involved to ensure a seamless and durable joint. As an experienced welder who has spent over a decade perfecting the craft, I have witnessed the transformation and innovation in welding technologies and methodologies. This article aims to delve into the essentials of carbon pipe welding, shedding light on the expertise, precision, and trustworthiness required to excel in this domain.
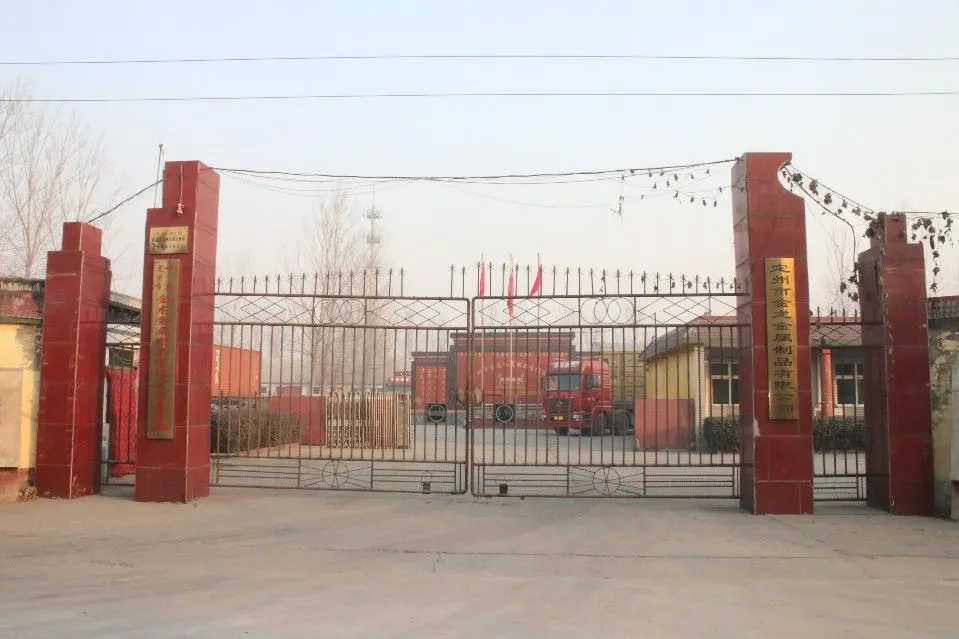
The first step in carbon pipe welding is understanding the distinct properties of carbon steel. Carbon steel is valued for its strength and resilience, making it a popular choice in industries such as construction, oil and gas, and water transport. However, this material's specific characteristics require precise management of heat input during the welding process to avoid issues like cracking and warping.
A successful weld is heavily reliant on the preparation of the pipe. Proper cleaning and beveling are crucial. Cleaning removes impurities that could compromise the weld, and beveling ensures a snug fit between the pipes, allowing for a deeper and more secure weld joint. Experienced welders know the significance of using the right bevel angle, which often depends on the pipe's diameter and the welding technique employed.
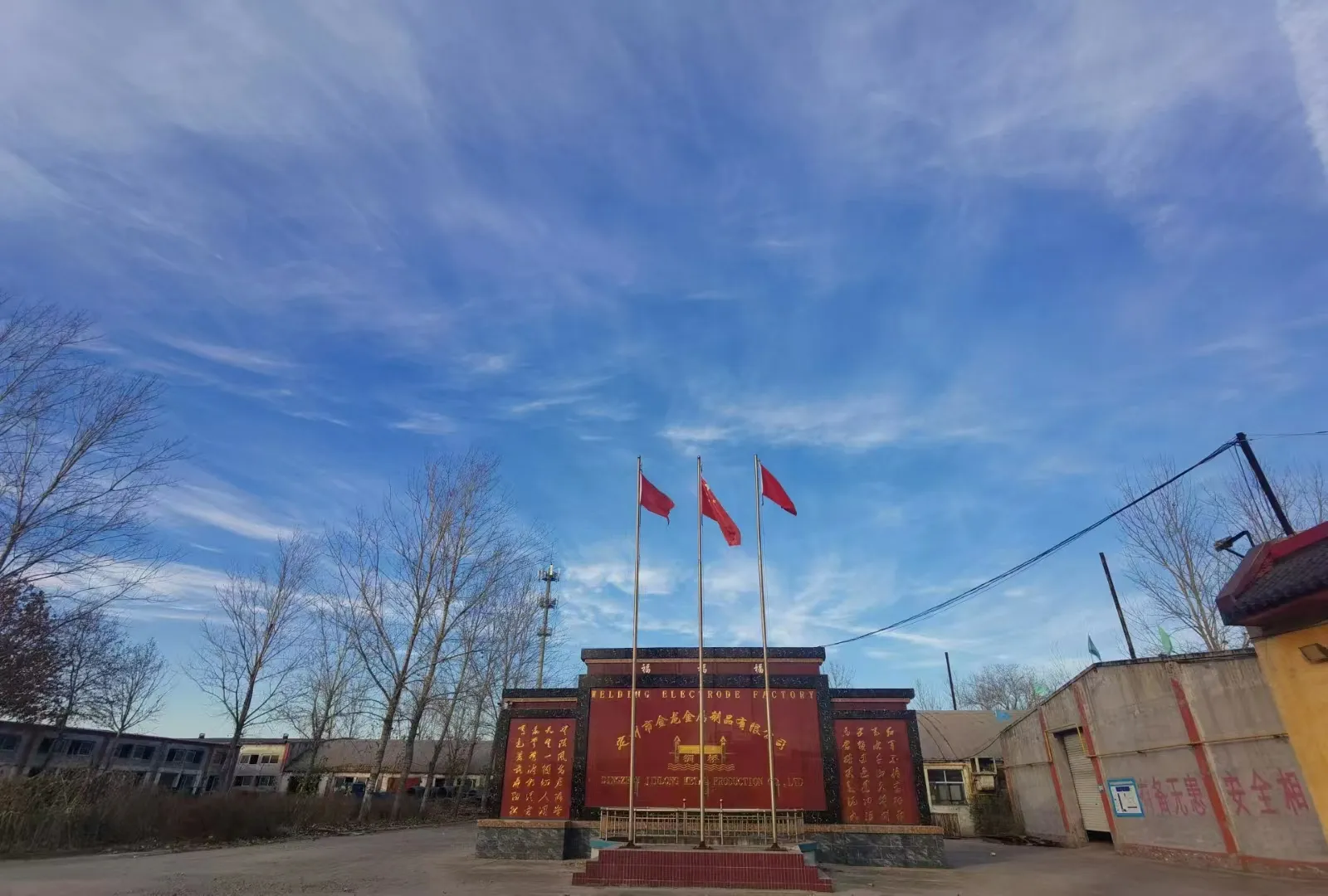
When it comes to welding techniques, there are several methods available, each with its own set of advantages. Shielded Metal Arc Welding (SMAW), also known as stick welding, is one of the most popular techniques due to its versatility and simplicity. However, for projects demanding higher precision and a cleaner finish, Gas Tungsten Arc Welding (GTAW) or Tungsten Inert Gas (TIG) welding is often preferred. TIG welding offers superior control over the welding arc and is often employed for thin wall sections and applications requiring high-quality welds.
Another aspect not to be overlooked is the role of filler material. Choosing a filler that matches the carbon content of the pipes is crucial for maintaining the integrity and strength of the weld. Welders must also manage interpass temperature, essential for preventing detrimental microstructural changes in the heat-affected zone.
carbon pipe welding
Safety is paramount in the field of welding. Carbon steel welding may produce fumes that require adequate ventilation or fume extraction systems to mitigate health risks. Wearing appropriate personal protective equipment, such as welding helmets, gloves, and protective clothing, is non-negotiable to prevent injuries from heat, sparks, and UV radiation.
Industry standards and certifications play a critical role in establishing trust and authority in carbon pipe welding. Adhering to standards such as those set by the American Welding Society (AWS) not only improves the quality of work but also ensures compliance with occupational safety regulations. For welders, obtaining certifications can demonstrate their competence and commitment to excellence.
Quality control and testing further reinforce the trustworthiness aspect of carbon pipe welding. Non-destructive testing methods like ultrasonic testing and radiographic testing help detect flaws or defects in welds without damaging the pipes. These tests are integral to maintaining the safety and durability standards expected in various industrial applications.
In conclusion, carbon pipe welding is an art that marries science and skill. It demands an in-depth understanding of materials, a mastery of welding techniques, and a rigorous commitment to safety and quality standards. Expertise in this field not only adds value to any project but also builds a reputation for reliability and excellence.