Welding stainless steel using a 7018 electrode is a topic that sparks interest among both seasoned welders and novices. To fully understand this, it’s crucial to explore both the technical specifications of these materials and the practical experience of welders who have attempted this process.
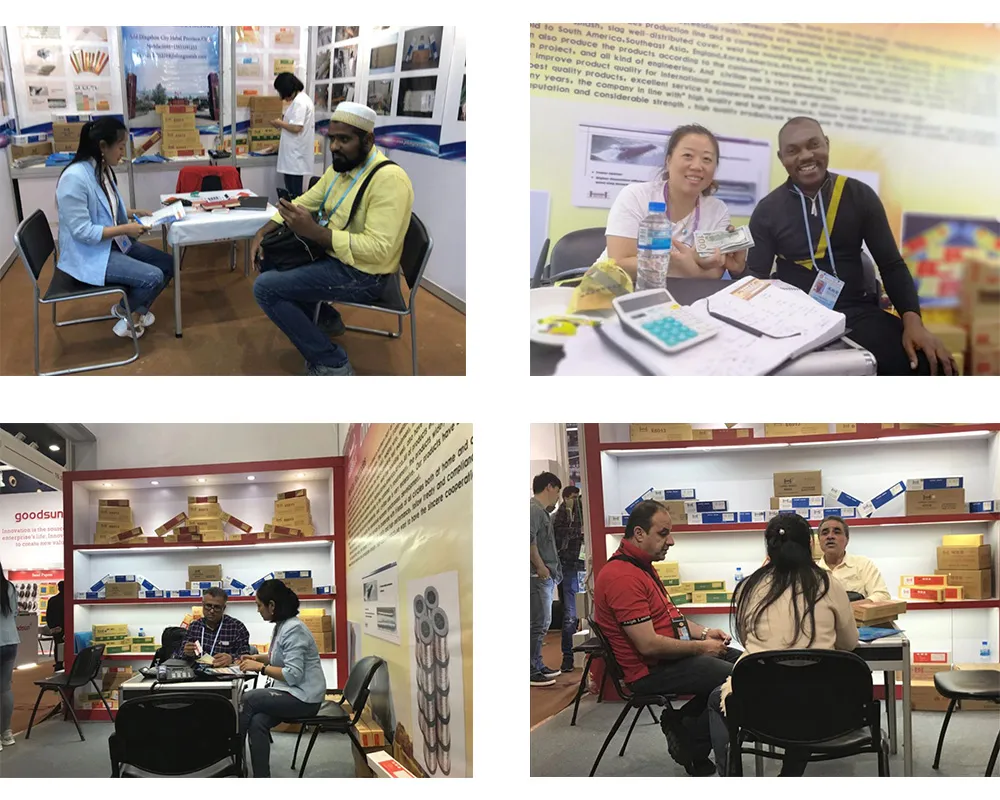
Stainless steel, known for its corrosion resistance and strength, is typically welded with electrodes specifically designed for stainless materials. The 7018 electrode, however, is a low-hydrogen mild steel electrode that is conventionally used for carbon steel. The juxtaposition of these two materials raises the question Can you achieve a successful weld on stainless steel using a 7018 electrode?
From a purely technical standpoint, welding stainless steel with a 7018 electrode is not ideal. The composition of the 7018 electrode and stainless steel differ significantly—7018 primarily consists of iron and a small percentage of carbon, while stainless steel contains chromium, nickel, and molybdenum. These alloying elements in stainless steel require electrodes that prevent chromium carbide precipitation and maintain corrosion resistance.
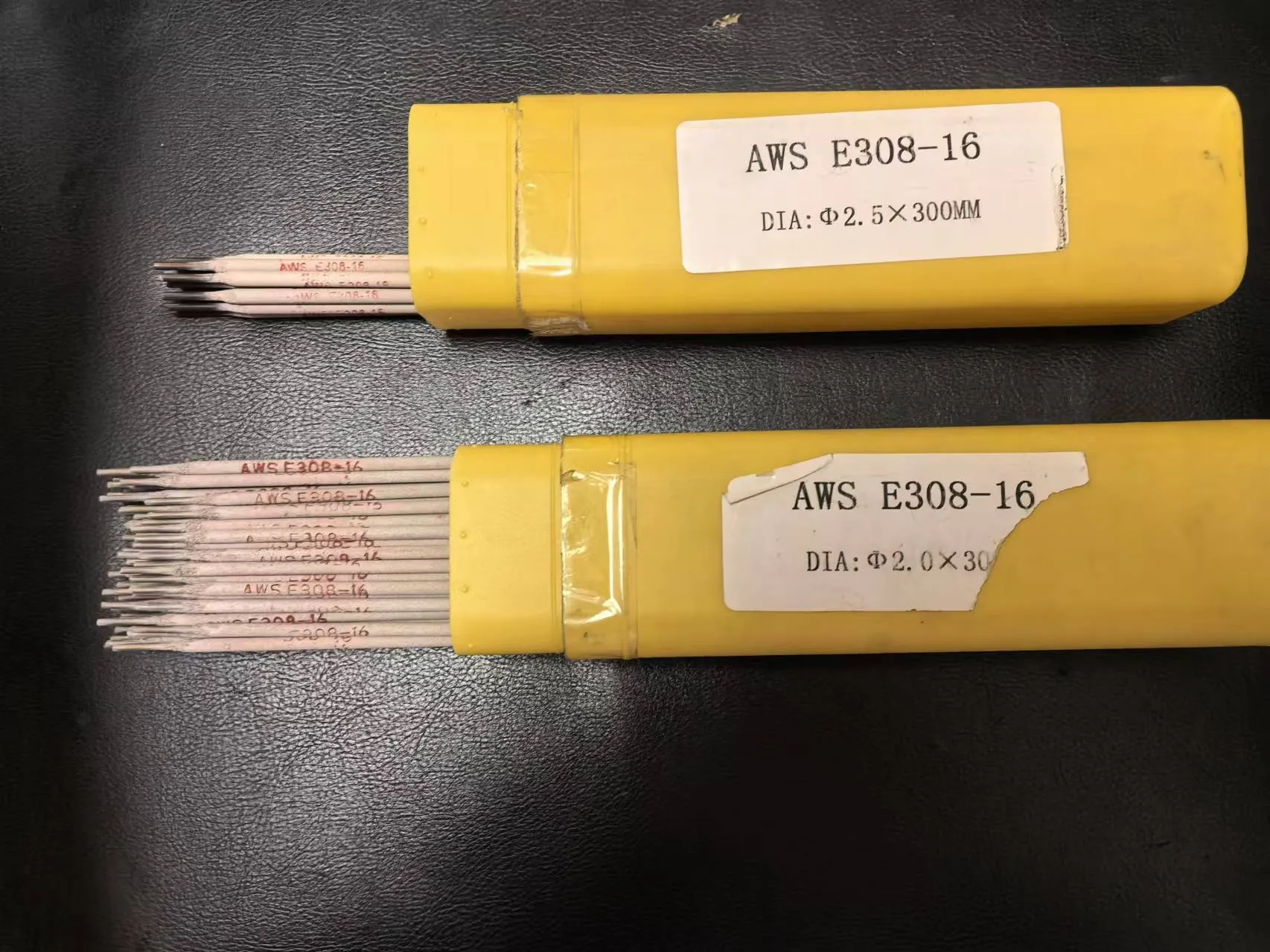
However, in practical situations, welders have occasionally resorted to using 7018 on stainless steel, often due to resource constraints. The experience of these welders provides valuable insights. The major compromise in using 7018 on stainless steel is a potential loss of the mechanical properties inherent to stainless materials. The weld deposit from a 7018 rod may introduce carbon to the stainless steel, potentially leading to carbide precipitation when exposed to air and hence reducing corrosion resistance. This makes such a weld unsuitable for applications where corrosion resistance is critical.
For welders who have experimented with 7018 on stainless for non-critical applications, the consensus highlights the necessity of surface preparation and post-weld treatment. Thorough cleaning of the stainless steel surface can help reduce contamination and improve weld quality. Additionally, careful control of the heat input is vital to avoid overheating, which could exacerbate potential pitfalls of this unlikely pairing.
can you weld stainless with 7018
Professional welders stress the importance of using these techniques sparingly and only when absolutely necessary. For instance, if welding fixtures in a non-corrosive environment where strength rather than appearance or corrosion resistance is paramount, some welders have found that using 7018 can be a workaround. Yet, they caution that structural integrity tests should be applied post-weld to ensure safety standards are met.
From an authoritative viewpoint, welding experts and metallurgy specialists advise against using 7018 electrodes on stainless steel wherever possible, recommending instead stainless steel electrodes like 308L or 309L for optimal results. These are specifically designed to complement the metallurgical structure of stainless steel and maintain its anti-corrosive properties.
To build trustworthiness, rely on firsthand accounts of experienced welders who confirm that while the task is technically possible, it is fraught with challenges and not recommended for critical welds. Documentation of these experiences across welding forums and professional advises creates a repository of knowledge endorsing the cautionary use of 7018 on stainless under non-standard situations.
In conclusion,
welding stainless steel with a 7018 electrode involves considerations of material compatibility and application necessity. While it can be done under specific circumstances, prioritizing the right electrode and understanding the implications on weld integrity is crucial. Always strive to obtain electrodes compatible with the base materials involved; in the case of stainless steel, leverage stainless-specific electrodes to ensure longevity and reliability of the weld.