Selecting the right welding rods can make a significant difference in the quality and longevity of a weld. As a seasoned professional in the welding industry, understanding the nuances of different welding rods is crucial to achieving the best possible results. Choosing the appropriate welding rod involves considering various factors such as material compatibility, rod size, and the specific requirements of your welding project.
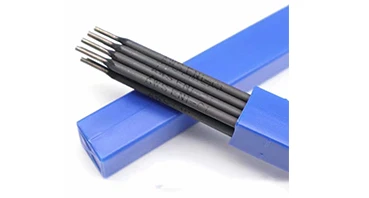
Firstly, it's essential to identify the base material that you are working with. Different alloys require specific rods to ensure a strong and durable bond. For instance, if you are welding mild steel, an E6011 or E6013 rod is often recommended due to their versatility and ease of use. Stainless steel projects, on the other hand, demand stainless steel rods like the E308L to prevent corrosion and maintain the integrity of the weld.
Moreover, the diameter of the welding rod plays a pivotal role in the outcome of your welding task. Thicker materials usually require a larger diameter rod for effective penetration, while thinner materials are best paired with smaller diameter rods to prevent burn-through. Understanding the thickness of your workpiece will guide you in selecting the appropriate rod size, ensuring strong and visually appealing welds.
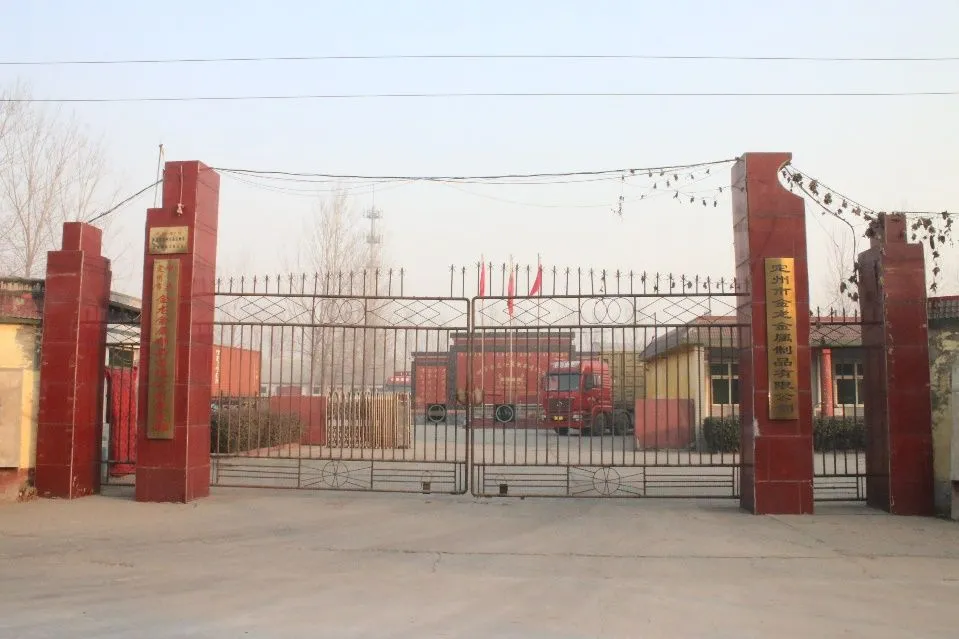
The type of current available (AC or DC) also influences the choice of welding rod. Certain rods are designed specifically for use with alternating current, such as the E6011, which excels in situations where a deeper penetration is needed, like in galvanized steels or rusty and dirty metals. Conversely, the E7018 is a low-hydrogen rod suited for DC operations, known for producing high-quality welds with smooth arcs and reduced spatter.
buy welding rods
Beyond technical specifications, storage and handling of welding rods significantly affect their performance. Moisture can lead to issues such as hydrogen embrittlement, causing welds to crack. It is crucial to keep welding rods in a dry environment, ideally in a rod oven, maintaining them at the manufacturer's recommended conditions. This practice not only extends the shelf life of the rods but also ensures optimal performance during use.
Additionally, the environment and position of the weld must be considered. Some welding rods are better suited for overhead or vertical positions, while others are designed for flat horizontal surfaces. For example, the E7014 is preferred for tackling vertical and overhead positions due to its fast freezing slag, which helps in maintaining the weld pool.
Investing time in researching the manufacturer and reviews of different welding rods can further validate your choice. Trusted brands with positive feedback are likely to provide consistently high-quality products, contributing to successful welding outcomes. Websites and forums where professionals share their experiences can be invaluable resources for insights about different rod types and their applications.
In conclusion, selecting the right welding rod is a combination of understanding the material, the welding position, current type, and environmental considerations. With meticulous research and attention to these details, one can achieve superior and dependable welds. Being informed not only boosts productivity but also enhances the quality of your work, reinforcing your credibility as an expert in the field.