When considering the selection of welding electrodes, the basic 7018 rod frequently emerges as a prime choice among professionals. Known for its versatility and reliability across a variety of applications, the 7018 electrode is the go-to for welders seeking consistent results combined with professional-grade outcomes.
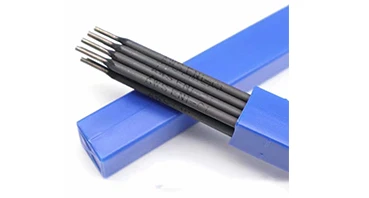
Crafted to excel in a multitude of environments, the basic 7018 welding rod boasts a low-hydrogen coating that minimizes the risk of hydrogen-induced cracking. This specific feature enhances its suitability for critical welds where strength and resilience are imperative. Frequent users, from seasoned welders to those refining their skills, often vouch for the ease of use and the clean, slick weld bead appearances achieved through this electrode.
From an expert's lens, the 7018 is celebrated for its impressive tensile strength, which typically ranges around 70,000 psi, ensuring that it meets demanding industry standards. This robust performance is essential, particularly in structural welding or scenarios where the integrity of the weld could be exposed to significant stress or environmental degradation.
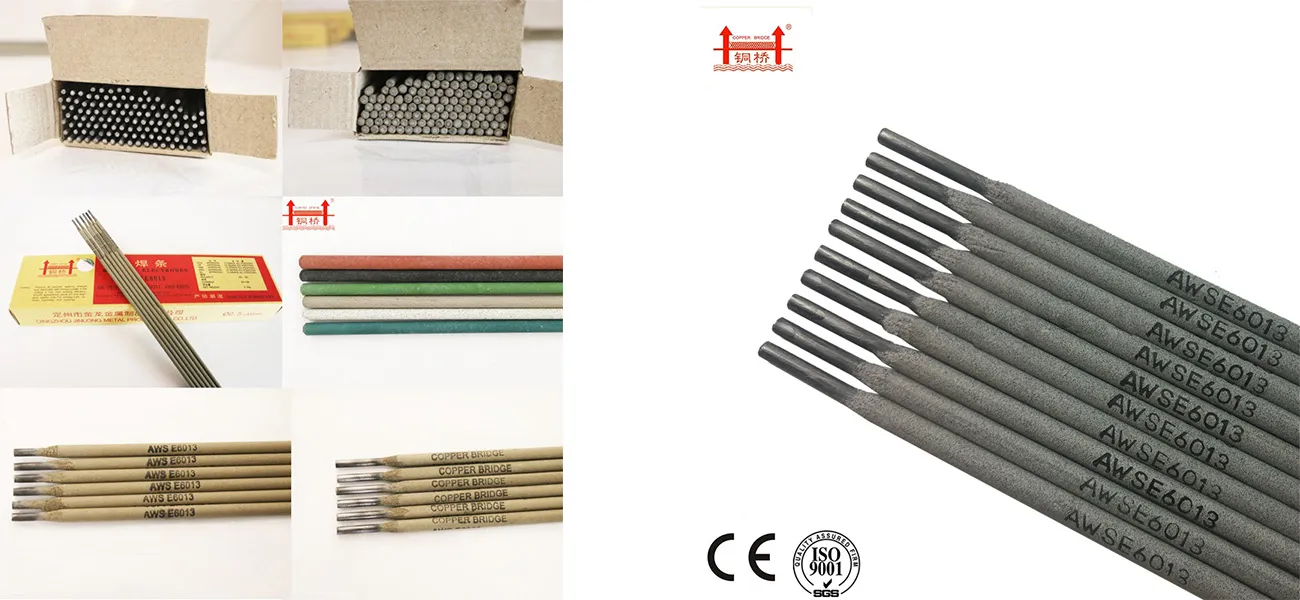
An insight into the composition of the 7018 electrode reveals the integral role of its iron powder flux, which not only assists in smooth arc operation but also contributes to the increased deposition rate. Such a high deposition rate means that a welder can complete jobs quicker without sacrificing quality, providing a balance between efficiency and craftsmanship that is not easily matched by other rods.
For welders who've accrued substantial hands-on experience, the 7018 is lauded for its arc stability. The rod's forgiving arc nature allows for minor inconsistencies in technique, making it suitable for both vertical and overhead welding positions. This adaptability is crucial in industry applications where variables can often deviate from ideal circumstances.
basic 7018
In an authoritative context, the 7018 electrode’s repeat appearances in welding procedure specifications (WPS) and qualifications underscore its legitimacy and trustworthiness within the professional domain. Industries ranging from shipbuilding to construction frequently prioritize this electrode to adhere to strict compliance and quality assurance mandates.
Trust in the 7018 extends beyond its technical specifications. For instance, practitioners regularly report higher satisfaction levels due to the rod's smooth deslagging properties, reinforcing its standing as a user-friendly option. Welding experts also emphasize the importance of proper storage for 7018 rods, as exposure to moisture can undermine the coating’s low-hydrogen characteristics. By maintaining a dry storage environment and following best practices, welders guarantee their projects will achieve optimal integrity and longevity.
For those striving to refine their skills with the 7018, it is harmonious with both AC and DC polarity settings, adding to its adaptability and prospective application in diverse projects. This versatility is particularly beneficial within fluctuating worksite conditions where flexibility is key.
Trustworthiness in welding translates to reliability in performance; the 7018 achieves this through a consistently low defect rate. As a result, fewer repairs or reworks are necessary, leading to increased productivity and customer satisfaction. These practical benefits underline why the basic 7018 continues to be endorsed by welding professionals and educators alike.
As the welding industry continues to evolve, the 7018 maintains its relevance, adapting alongside new technologies and methodologies. It brings a harmonious blend of traditional expertise and modern advancements to the fore, ensuring that welders can tackle projects with assuredness and precision.