The AWS E6013 welding electrode is a cornerstone in the world of welding, known for its ease of use and versatility across various applications. These electrodes are preferred by both beginners and seasoned professionals due to their forgiving nature during the welding process and ability to produce smooth, aesthetically pleasing welds. Here's an in-depth exploration into the practical advantages, expert insights, and authoritative recommendations surrounding AWS E6013 welding electrodes.
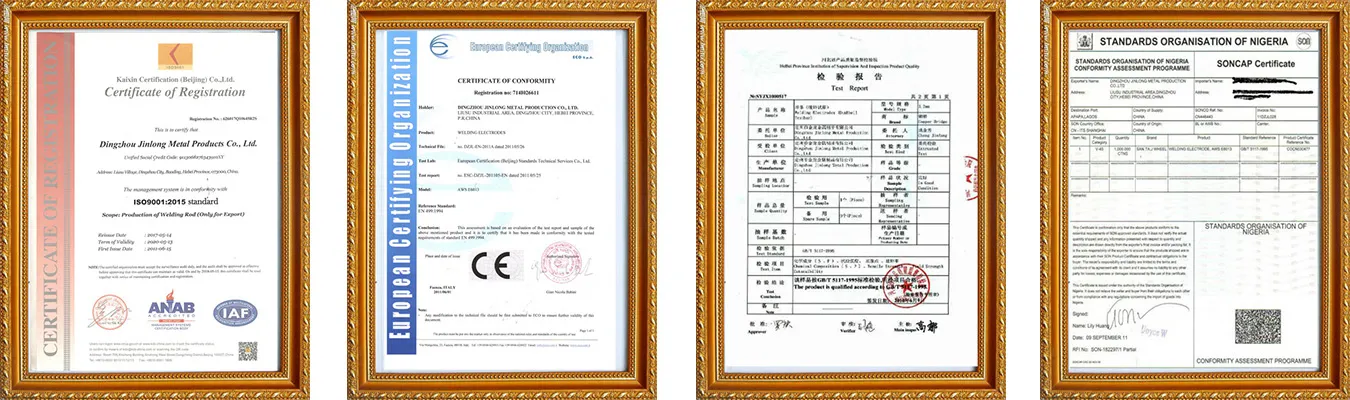
As one embarks on a journey with welding, choosing the right electrode is critical to both performance and the final appearance of the weld. The E6013 electrode is particularly popular due to its rutile-based flux coating, which allows for a soft arc with minimal spatter. This electrode is designed for welding in all positions, making it adaptable to a diverse range of projects, from simple repairs to complex structural work.
Expertise in welding necessitates an understanding of the materials one is working with.
The AWS E6013 is optimal for welding mild steels and thin sections because it provides a stable arc and excellent slag control. The ability to weld in all positions, including vertical up and down, as well as overhead, extends the functionality of E6013 electrodes beyond many of its counterparts.
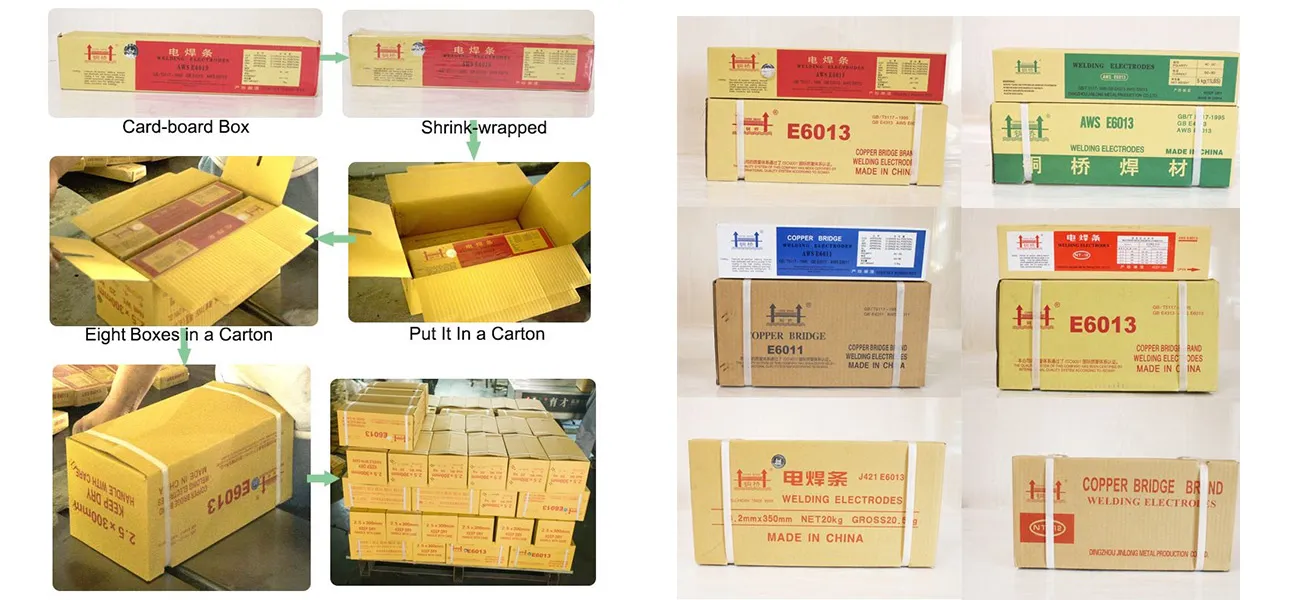
Experience from seasoned welders consistently highlights the user-friendly nature of the E6013. When teaching newcomers, instructors often start with E6013 electrodes because they offer a forgiving puddle control. This characteristic helps in reducing burn-through on thinner metals and allows learners to focus on perfecting their technique without excessive concern over electrode manipulation. The authority of this simplicity is underscored by the consistency of weld beads that E6013 electrodes produce, which is a key factor when evaluating weld integrity.
aws e6013 welding electrode
Trustworthiness in welding materials often hinges on compliance with industry standards and certifications. AWS E6013 electrodes are manufactured in accordance with stringent quality norms that ensure consistent performance. Entrusting one's projects to these electrodes can guarantee that welds conform to professional expectations of strength and durability. Manufacturers of E6013 electrodes supply them in various sizes, further allowing welders to select the diameters best suited for specific tasks. This flexibility accommodates a variety of welding equipment and project scopes, enhancing the reliability of the final product.
When delving into welding with E6013, it's crucial to acknowledge the best practices that maximize their effectiveness. Experts advise maintaining a proper arc length, generally about 1/8 inch from the metal surface, to sustain a smooth arc and minimize spatter. Pre-cleaning the metal surfaces ensures the arc remains stable, contributing to cleaner and stronger bonds. Such insights drawn from industry practice significantly bolster the authoritativeness of using AWS E6013 electrodes in any professional setting.
In adopting E6013 electrodes, mastering the drag technique can also enhance weld precision. This technique involves holding the electrode perpendicular to the workpiece, dragging it along the joint while maintaining a consistent speed. It’s the simplicity of this approach that makes E6013 electrodes the go-to choice for intricate tasks like sheet metal welding, where precision is paramount.
In conclusion, AWS E6013 welding electrodes embody a blend of simplicity, reliability, and versatility that has secured their status as a favorite among welders of all proficiency levels. Their capacity to yield consistent and visually appealing welds, backed by industry-best practices and standards, ensures trustworthiness in diverse applications. By integrating expert knowledge with hands-on experience, the E6013 continues to influence the welding landscape as a cornerstone tool that professionals can rely on for quality and performance.