The AWS 7018 welding rod, an essential tool in the welding industry, has garnered attention for its exemplary performance across diverse applications. This electrode is celebrated for its superior weld characteristics, primarily in structural steel projects, offering a blend of reliability, durability, and versatility that few other rods can match.
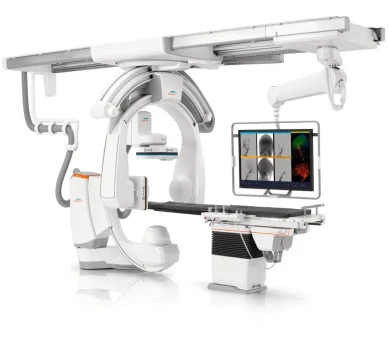
Beginning with its fundamental composition,
the 7018 welding rod is known for its iron powder, low hydrogen coating. This composition is integral to its popularity, as it significantly reduces the hydrogen content in the weld puddle, minimizing the risk of cracking and producing clean, smooth welds. Professionals in the field emphasize the importance of using a low hydrogen rod for critical welding jobs, particularly those involving high-tensile strength materials and projects that cannot afford failure.
Experience in the field suggests that the 7018 yields optimal results when welding mild to low alloy steels. Welders often choose this rod for jobs that require a fine balance between toughness and ductility. For instance, industries involving the construction of bridges, buildings, and pressure vessels frequently rely on the 7018 for its dependable performance and the high-quality weld it produces.
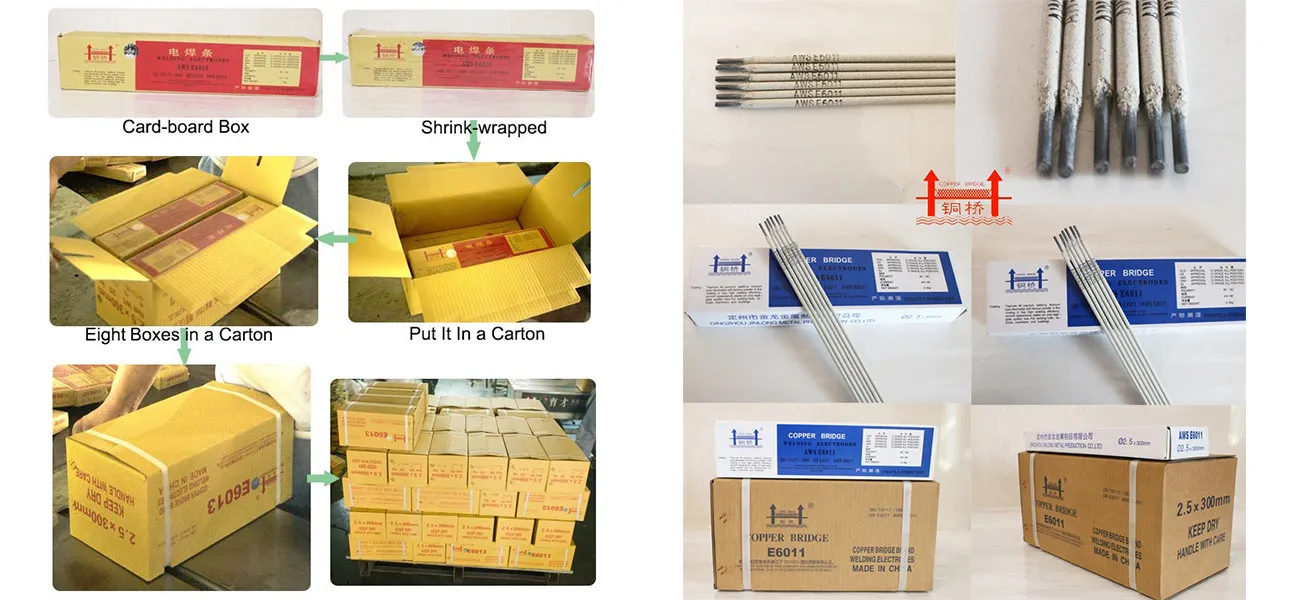
From an expertise standpoint, the AWS 7018 rod stands out for its ease of use, even for those who may not be seasoned welders. The arc is stable and easily controlled, making it a preferred choice for both vertical and overhead welding positions. However, to fully leverage its capabilities, welders must ensure the rods are properly stored in a dry environment. Any exposure to moisture can compromise the low hydrogen properties, which is why professionals recommend using a rod oven to maintain optimal functionality.
Authoritativeness in using the 7018 comes from understanding the specific amperage settings required to achieve optimal weld quality. Typically, welders suggest a range between 70 to 190 amps, varying slightly depending on the thickness of the material and the specific requirements of the project. Adjusting these settings correctly is crucial for achieving the deep penetration and robust fusion that the 7018 is known for.
aws 7018 welding rod
Trustworthiness of the AWS 7018 is reflected in its designation by the American Welding Society (AWS), an authoritative body that provides guidelines ensuring the quality and safety of welding practices. This designation assures that the rod has been tested rigorously to meet specific performance standards, offering peace of mind to engineers and welding professionals who depend on these guidelines to complete critical infrastructure projects.
Moreover, the availability of the 7018 in various diameters expands its applicability across different welding tasks, from smaller scale repairs to large structural welds. This adaptability makes the rod an invaluable asset in the toolkit of any professional welder or fabrication team. The E7018 is especially noted for its remarkable deposition rate, which streamlines the welding process, reducing time and labor without compromising quality.
The versatility of the 7018 extends beyond basic applications. In more advanced welding scenarios, the rod is often used in post-weld heat treatment (PWHT) procedures to relieve stress in the welded material, further enhancing its structural integrity. Engineers and welding technologists recognize that PWHT, when combined with the properties of the 7018 rod, results in welds that withstand the test of time and severe operational conditions.
In conclusion, the AWS 7018 welding rod continues to be a pillar in the welding community due to its reliable performance across a multitude of applications. Its carefully engineered composition, ease of handling, and compliance with strict industry standards make it a go-to electrode for professional welders worldwide. As welding technology progresses, the enduring reputation and versatile functionality of the 7018 ensure it remains a trusted choice for critical welding projects that demand precision and strength.