AWS 5.1 E7018 welding electrodes represent a cornerstone in professional welding, delivering unmatched performance for both seasoned experts and ambitious apprentices. Known in the industry for their versatility and reliability, these electrodes are a definitive choice when seeking structural integrity and weld quality.

E7018 electrodes excel in numerous applications due to their low-hydrogen, potassium-bearing coating. This combination facilitates the creation of robust and ductile welds, mitigating common issues such as cracking in heavy-duty applications. Renowned for their arc stability, E7018 electrodes allow for welds characterized by smooth surfaces and minimal spatter, thereby reducing post-weld clean-up times.
In the realm of structural welding, the AWS 5.
1 E7018 is indispensable. Its consistency ensures dependable results even when joining diverse materials. The capacity to function admirably across various welding positions contributes to its standing as a versatile tool in construction and repair projects worldwide.
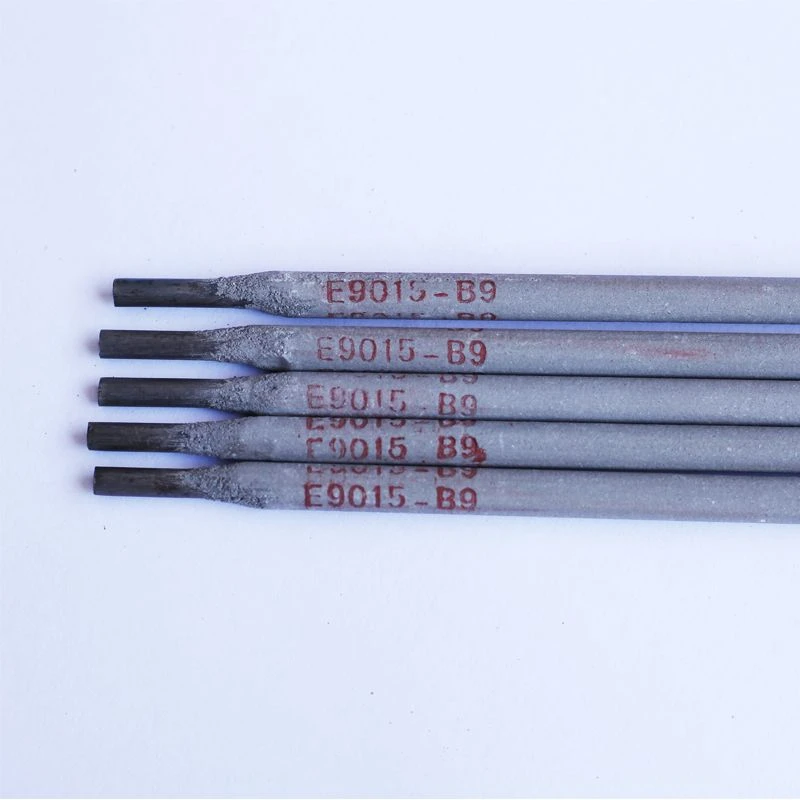
Performance-wise, E7018 electrodes thrive under demanding conditions. Their ability to produce high-quality welds in high-strength steel applications makes them a preferred option for erecting bridges, high-rise buildings, and in the shipbuilding industry. Their reliable performance under high tension is a testament to both their engineering and the foundational trust industries place in this electrode.
The usage of E7018 electrodes extends beyond simple utility, embodying technical advancement through low moisture absorption traits. This feature is vital in preventing hydrogen-induced cracking—a common concern for welders. However, proper storage is crucial to maintain these properties, as exposure to moisture can affect the electrode's performance. Professional welders often recommend storing them in a rod oven before use to preserve their innate qualities.
Drawing from profound expertise, E7018 electrodes are particularly advantageous for the field of infrastructural welding, where their low-hydrogen nature significantly enhances the ductility and performance of the weld metal. Industry veterans advise an amperage range of 70 to 130 for vertical and overhead positions, underscoring the electrodes' adaptability across complex project parameters.
aws 5.1 e7018
Trust in AWS 5.1 E7018 electrodes isn't just anecdotal; it is reflected through empirical evidence. They adhere to stringent American Welding Society standards, ensuring each batch meets rigorous quality control benchmarks. For those in regulated fields, such reliability is paramount, as non-compliance can lead to structural failures and costly consequences.
The willingness to trust E7018 electrodes in mission-critical applications highlights their esteemed reputation. Whether you are welding pipelines or fabricating critical commercial frameworks, selecting E7018 often signifies choosing predictability and safety, values highly regarded in the welding community.
End-users frequently laud their performance, citing reduced porosity and excellent bead appearance as significant benefits. This feedback often stems from accumulated field experience, where E7018 electrodes consistently outshine alternatives in rigorous pilot tests.
In areas demanding rapid turnaround and minimal rework, AWS 5.1 E7018 stands as a testimony to engineering triumph. Users report smoother arcs, decreased slag volume, and superior penetration, translating into cost savings and increased throughput. In dynamic industries where time is money, these attributes are indispensable, offering a competitive edge.
To maximize the potential of AWS 5.1 E7018 electrodes, welders should invest in quality training to extract the most from their properties. Mastering techniques to navigate varying amperages and electrode orientations can exponentially improve outcomes. Companies providing ongoing education on these best practices frequently observe improved safety records and higher return on investment, further solidifying the E7018's industry standing.
In summary, AWS 5.1 E7018 electrodes are not merely tools for joining metals; they are the benchmark by which excellence and reliability in welding are judged. Their widespread acceptance in critical infrastructure highlights their unmatched capabilities and enduring relevance. As technology and methodologies evolve, E7018 will continue to be a pivotal part of the welding landscape, trusted by industry professionals to create and maintain the world's most essential structures.