Argon welding rods, a crucial component in the process of TIG (Tungsten Inert Gas) welding, are essential for achieving high-quality welds in various metals. Their properties and the unique shielding capabilities they provide are engineer-tested and electrician-approved, ensuring that professionals can execute tasks with enhanced precision and safety.
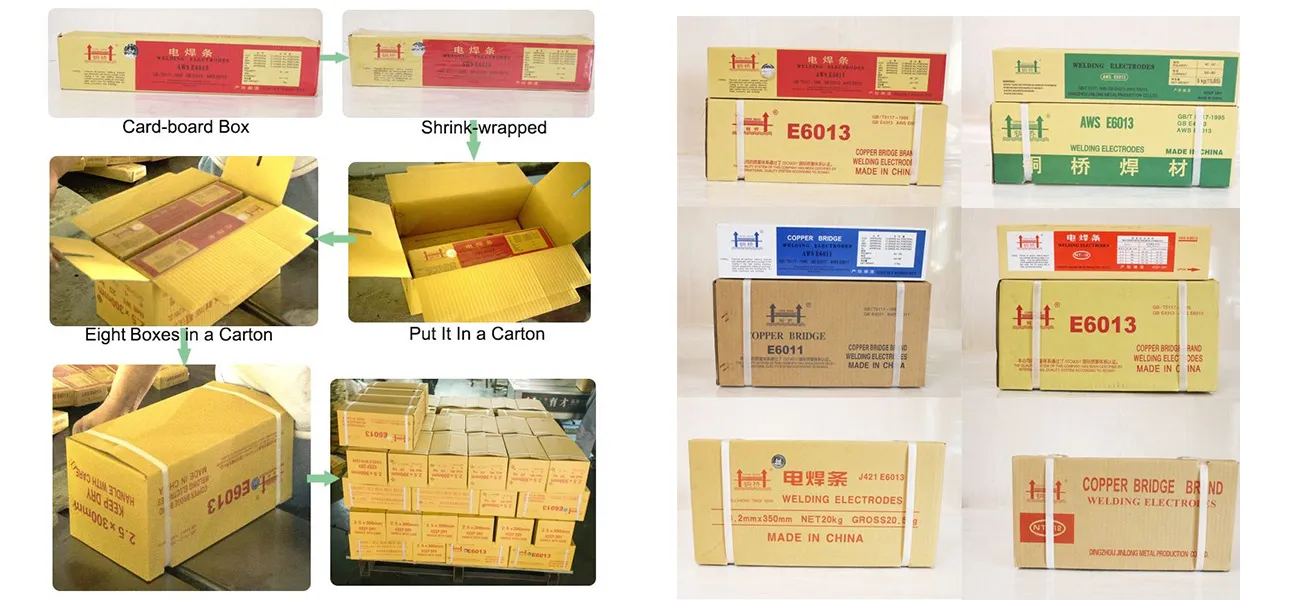
Understanding the Specifications of Argon Welding Rods
Argon welding rods are specifically designed to complement the argon gas used in TIG welding. Their composition is critical as it influences the mechanical properties and overall performance of the weld. Typically, they are crafted from metals such as aluminum, stainless steel, and mild steel, each offering distinct advantages. For instance, aluminum rods are lightweight and resistant to corrosion, perfect for welding outside in harsh conditions. In contrast, stainless steel rods provide superior strength and durability, making them ideal for industrial use.
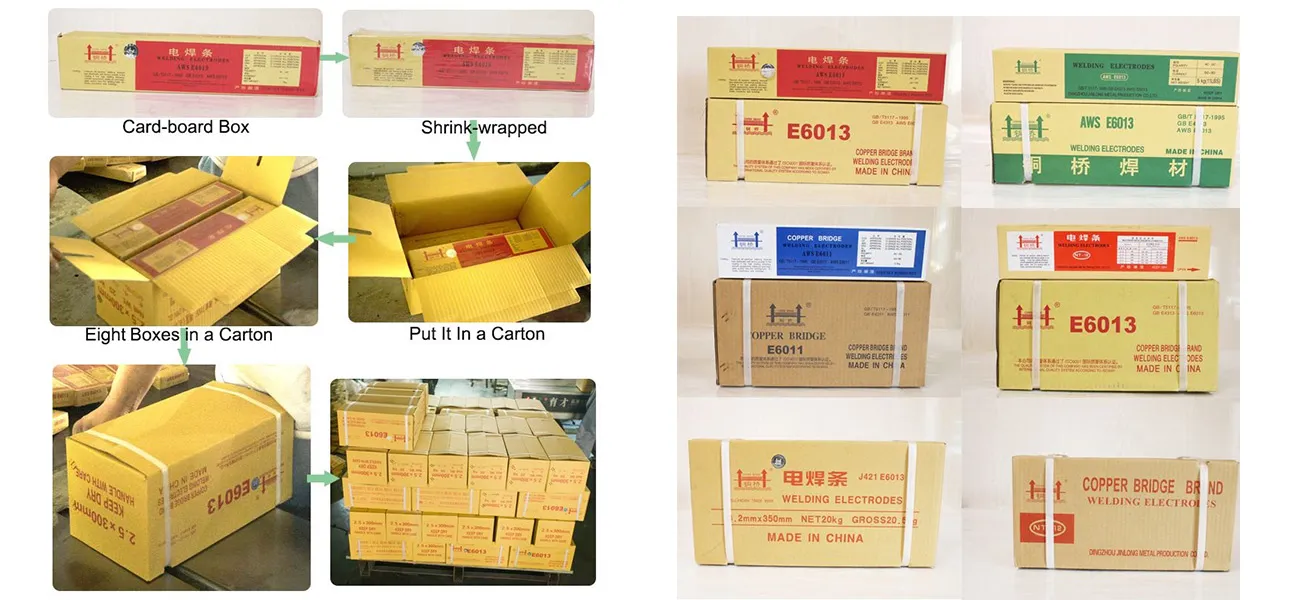
The Role of Argon in Shielding and Weld Integrity
Argon gas plays a vital role in the welding process by providing an inert shield that protects the weld pool from atmospheric contamination. This ensures that the molten metal remains pure and free from oxidation, which can otherwise result in weak joints. The argon atmosphere stabilizes the arc and enhances the quality of the weld by minimizing spatter and the occurrence of porosity in the weld. Experienced welders will emphasize that proper gas flow rates are crucial as they affect the consistency of this protective barrier.
Real-World Applications and Expert Advice
argon welding rod
In industries like aerospace, automotive, and construction, argon welding rods have become indispensable. Their reliability in creating neat, strong, and clean welds in aluminum and other non-ferrous metals makes them the tool of choice for specialists. An expert welder with decades of experience might demonstrate that using argon rods with a slightly larger diameter can enhance penetration and improve heat control in thicker metals.
Furthermore,
maintaining precision in TIG welding requires meticulous preparation and settings. Professionals recommend ensuring that the tungsten electrode is sharpened correctly and the welding equipment is calibrated according to the manufacturer's recommended specifications. Adhering to these guidelines not only extends the life of the welding rods but also improves the structural integrity of the finished product.
Enhancing Performance through Trustworthy Practices
To maximize the effectiveness of argon welding rods, consistency in practice and adherence to safety standards are paramount. Skilled welders consistently stress the importance of wearing appropriate protective gear, such as gloves and goggles. These prevent skin burns and eye injuries, thereby fostering a trustworthy working environment. Maintaining equipment and regularly inspecting welding rods for any signs of wear and tear is a practice embedded in the discipline of conscientious welders.
Moreover, investing in quality rods from reputable manufacturers can not only augment weld quality but also save time and resources in the long run. Authentic customer reviews and verified purchase testimonials can guide welders to ensure they are purchasing products that meet the high standards required for precision welding.
In conclusion, argon welding rods are a fundamental part of the TIG welding process, and understanding their composition, operational mechanisms, and real-world application enhances their effectiveness. By following expert guidance and maintaining trustworthy practices, one can significantly improve welding outcomes, reinforcing the vital role these rods play in modern industries. These aspects reflect the contemporary demands of welding professionals and highlight the importance of continuous learning and adaptation in the dynamic environment of metal fabrication.