Arc welding rods for cast iron represent a niche yet essential tool for both professional welders and DIY enthusiasts working with cast iron materials. Catering to the specific properties of cast iron, these rods facilitate effective and robust repairs and fabrications, ensuring structural integrity remains unchallenged.
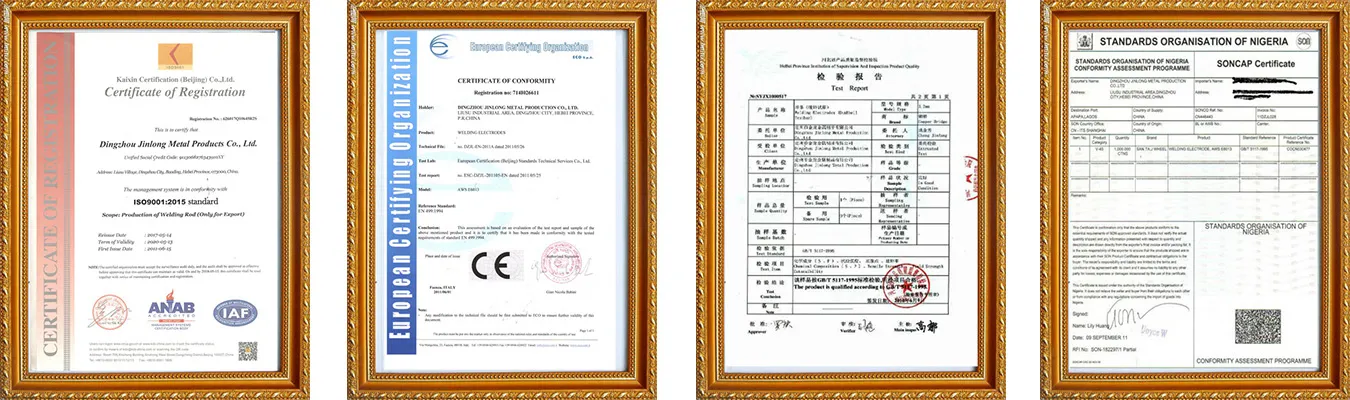
Cast iron's inherent characteristics — its high carbon content and rigidity — make it challenging to weld. The material is prone to cracking and warping under the intense heat of welding. Therefore, selecting the right welding rod becomes crucial. Nickel-based rods are widely considered the optimal choice for welding cast iron. These rods possess properties that closely match those of cast iron, offering flexibility and reducing the risk of stress concentrations and failures. The elasticity they provide is essential for accommodating the thermal expansion and contraction that occurs during the welding process.
One of the distinguishing features of arc welding rods designed for cast iron is their composition. A higher nickel content not only provides a bond that withstands thermal cycling but also ensures that the welds produced are machinable, a significant advantage if the welded joint requires post-weld processing.
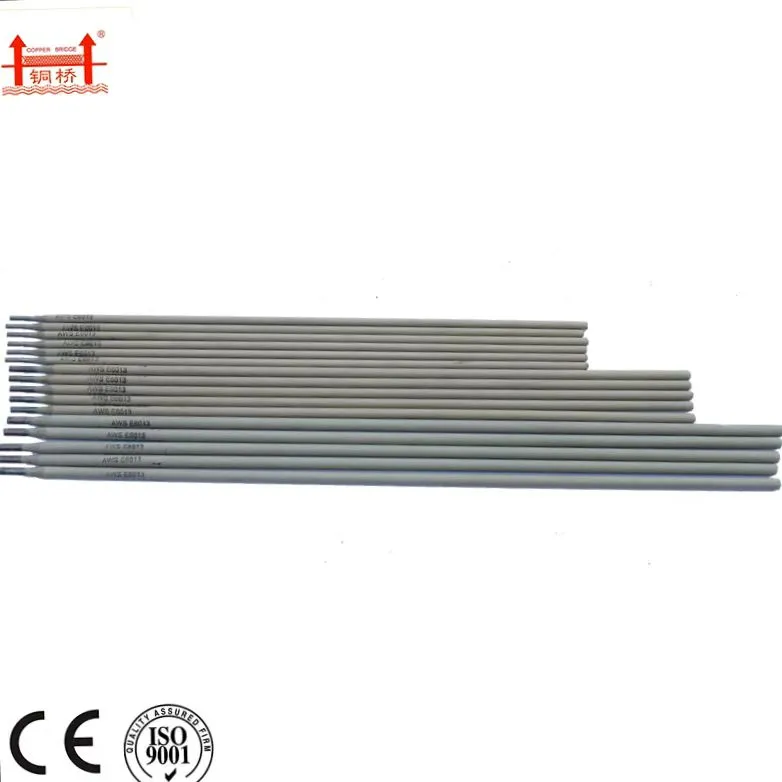
When choosing an arc welding rod for cast iron, welders must consider the grade of cast iron in question. Grey cast iron, with its graphite flakes, differs from ductile iron which contains graphite in spherical nodules. Each type influences the welding technique and rod selection. For example, coated nickel-iron electrodes tend to be a preferable option for high-strength applications and varying types of cast iron.
Professional welders often emphasize the importance of preheating the cast iron workpiece before proceeding with the arc welding process. Preheating minimizes the risk of thermal shock which can lead to cracks forming in or near the weld zone. Maintaining an appropriate temperature during the process ensures that the weld cools down slowly, thereby mitigating the stresses that can lead to failure.
arc welding rods for cast iron
The technical demands of welding cast iron necessitate attention to detail and a deep understanding of both materials and equipment. Closing the weld with controlled heat and managing the heat input are techniques that require practice and expertise, setting apart amateur efforts from professional results. Expert welders attest to the significance of maintaining a balanced heat input by stitching or using a weave pattern, which evenly distributes the stress and reduces the instances of stress-induced cracking.
Trustworthy suppliers of arc welding rods for cast iron often provide detailed specifications and recommendations, aiding customers in making informed decisions. User reviews and feedback can serve as reliable indicators of product performance, offering insights into real-world applications and durability.
As industries and hobbyists continue to rely on cast iron for its durability and cost-effectiveness, the demand for effective welding solutions grows. Investments in the right arc welding rods not only reinforce the quality of structural repairs but also enhance the lifespan of cast iron components. Whether repairing a vintage car engine block or addressing fissures in industrial machinery, the right welding solution is an investment in reliability and efficiency.
For mechanics, artisans, and welders, understanding the unique challenges presented by cast iron and the solutions offered by modern arc welding rods is fundamental. It bridges the gap between innovative repair capabilities and traditional craftsmanship, ensuring that cast iron remains a viable and trusted material in both contemporary and future applications.