When it comes to welding between alloy steel and carbon steel, selecting the right electrode is crucial for achieving a high-quality, durable weld. The fusion of these two metals is common in industries ranging from automotive to construction, where each offers distinct benefits. With years of hands-on experience, this guide aims to delve deeper into the essentials of choosing the best welding electrode, enhancing both your knowledge and application expertise.
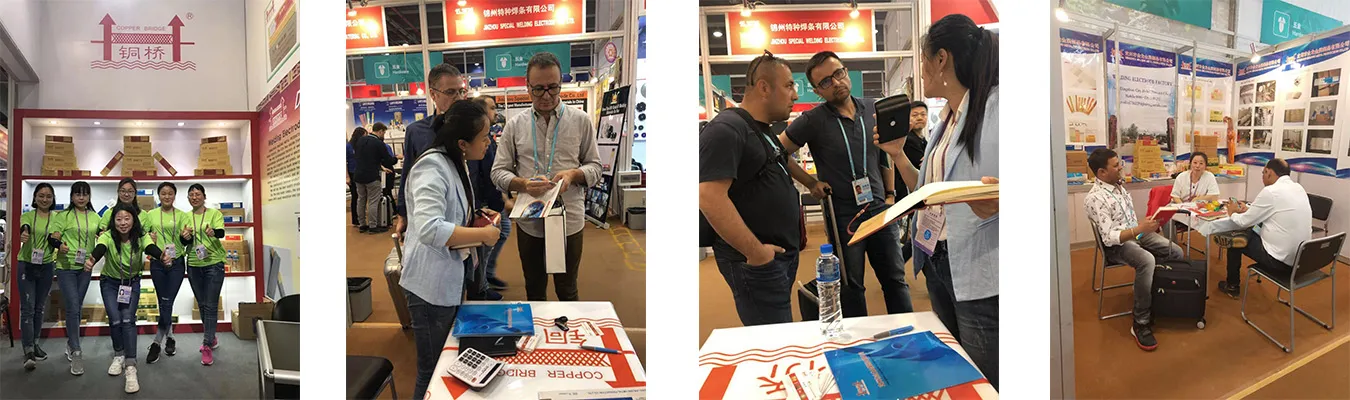
Alloy steel is prized for its durability, resistance to corrosion, and ability to retain strength at varying temperatures. On the other hand,
carbon steel is favored for its strength and cost-effectiveness. Joining these metals typically requires an electrode that can bridge the properties of both without compromising integrity. The choice of electrode plays a pivotal role in managing factors like crack resistance and mechanical compatibility.
Before selecting an electrode, one must assess several key factors the composition of the base metals, the specific working environment, and the mechanical properties desired in the finished weld. These considerations help in narrowing down a suitable electrode that complements the properties of both alloy and carbon steel. Based on extensive research and application testing in the field, one popular choice that emerges is the E309L-16 electrode.
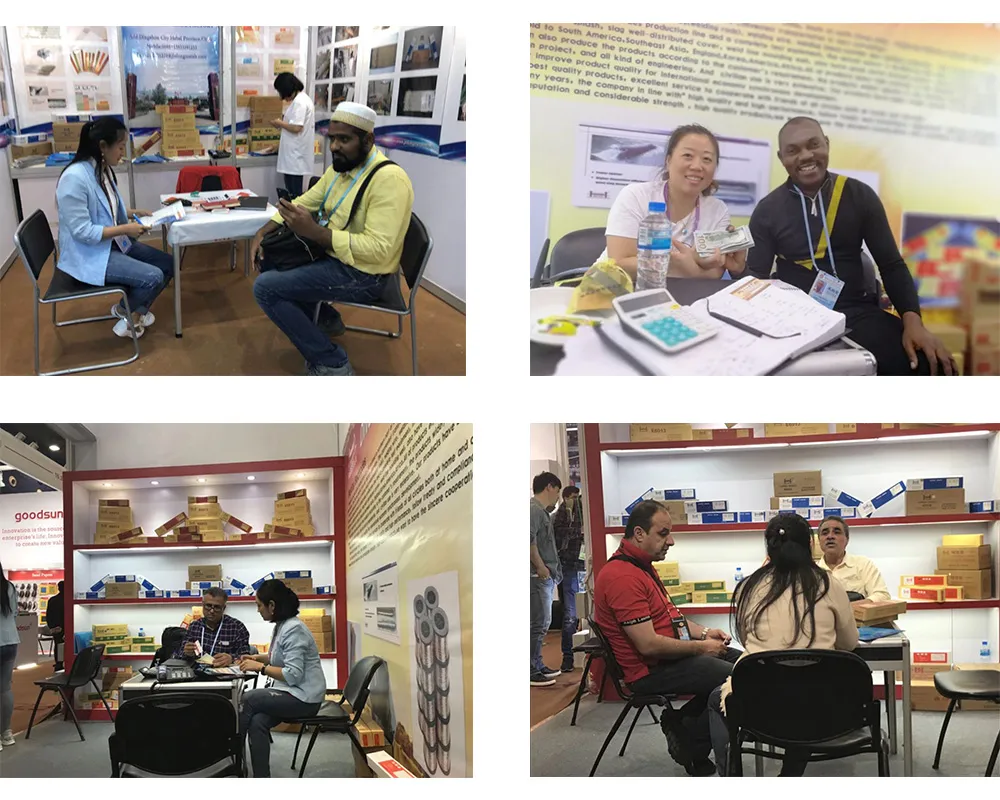
The E309L-16 electrode stands out as an excellent option due to its capability to handle dissimilar metal welding. It offers a stable arc, good slag detachability, and produces welds that are resistant to cracking. The low carbon content minimizes carbide precipitation, which is essential for maintaining corrosion resistance and mechanical strength of the weld. Experts in welding metallurgy emphasize the significance of a low carbon content, especially when working with alloy steel, to prevent weakening of the weld joint over time.
alloy steel to carbon steel welding electrode
Another considerable option is the E10018-D2 electrode, especially in scenarios where higher tensile strength is required. This electrode is designed specifically to weld alloy steels that demand both robust mechanical properties and the ability to withstand significant stress. It effectively mitigates the risk of hardening, ensuring a smooth weld between alloy and carbon steel. Specialized training in its use can further enhance results, as manipulating the weld pool requires precision.
The process doesn’t end at selecting an electrode; the technique and equipment settings are equally important. Experienced welders stress the importance of preheating and post-weld heat treatment (PWHT) in such scenarios. Preheating helps minimize thermal shock and reduces the chances of developing cracks around the weld zone. PWHT is recommended for relieving residual stresses and achieving desired mechanical properties, which is critical in pressure retaining applications.
Trustworthiness in choosing the right electrode can be enhanced by consulting detailed manufacturer specifications and seeking expertise from certified welding professionals. Certifications like AWS (American Welding Society) standards ensure the electrodes meet rigorous testing requirements. Incorporating their insights attests to a more informed decision-making process, positioning your welding operations within a framework of reliability and efficiency.
In the dynamic landscape of metallurgy and material science, staying informed of the latest electrode technologies can offer a competitive edge. Expertise comes from not just understanding welding principles, but also from a willingness to adapt and innovate with newer techniques and materials. Leveraging this knowledge not only improves welding performance but also elevates operational standards in environments where alloy and carbon steels intersect.