Navigating the expansive world of welding requires understanding and selecting the right equipment and materials, which is why the AC 7018 welding electrode emerges as a leading choice for both novices and seasoned professionals alike. Combining technological ingenuity with tried-and-true efficacy, this particular electrode stands out in the realm of shielded metal arc welding (SMAW), often referred to as stick welding.
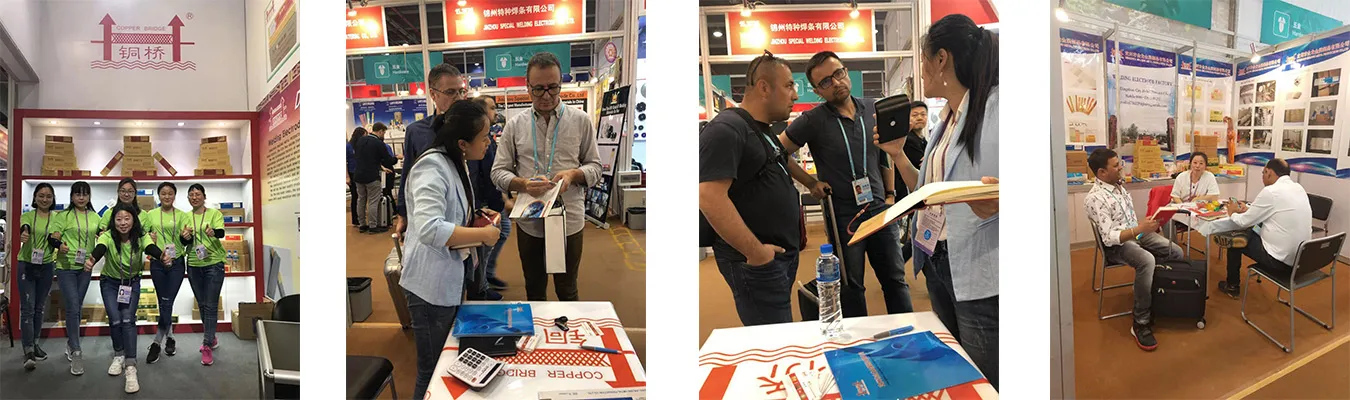
Diving into the specifics, it’s essential to appreciate the AC 7018 electrode primarily for its versatility and reliability across diverse applications. Known for producing exceptionally smooth and strong welds, it is often the electrode of choice in construction, shipbuilding, and pipeline work. What sets the AC 7018 apart is its unique ability to operate on both alternating current (AC) and direct current (DC), providing flexibility that is highly valued in scenarios where equipment or power supply may present limitations.
From an experiential standpoint, welders who have worked with the AC 7018 often commend its capability to create a stable arc, minimizing spatter and producing a cleaner welding finish. This characteristic is particularly beneficial in environments where precision is paramount and post-weld cleaning time needs to be minimized. The electrode’s low-hydrogen coating is another pivotal feature, reducing the risk of cracking in the weld metal and thereby enhancing the structural integrity and longevity of the welds.
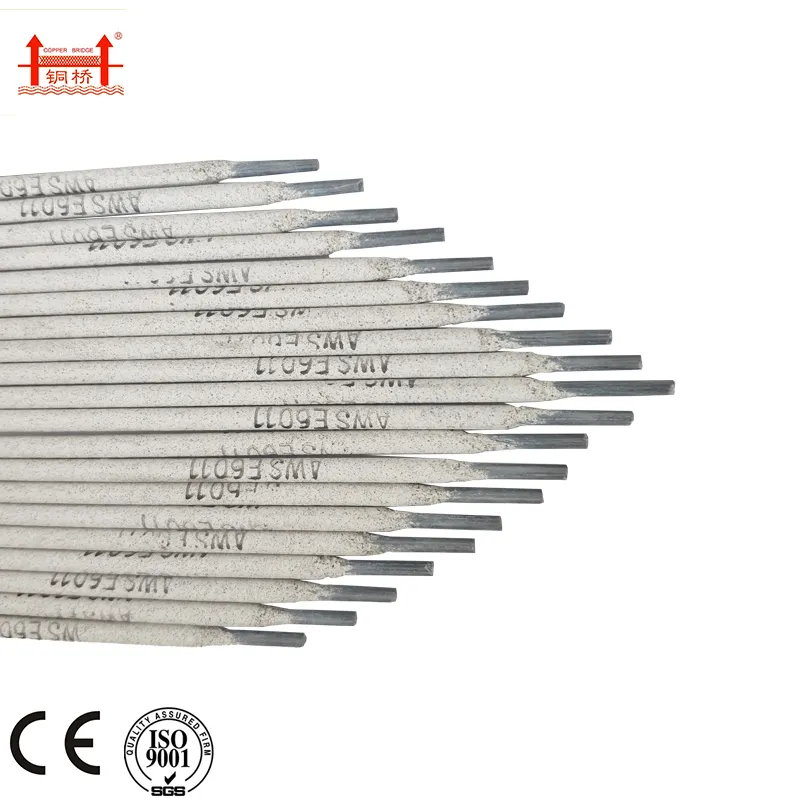
In terms of expertise, professionals in the field repeatedly highlight the AC 7018’s impressive tensile strength rating of approximately 70,000 psi, making it ideal for heavy-duty applications where structural demands are stringent. This performance specification aligns with industry standards and demonstrates the electrode's capacity to withstand significant stress without compromising safety or weld quality. Furthermore, this electrode is frequently employed in out-of-position welding tasks, thanks to its controllable slag and deposition rate, allowing for versatility in different welding orientations.
Authoritativeness in welding circles often points towards the adherence to international standards and regulatory benchmarks. The AC 7018 excels here, as it complies with various globally recognized standards like the AWS (American Welding Society) classification, ensuring that it meets critical safety and quality requirements. Such endorsements offer confidence to procurement specialists and engineers who seek assurance from certifiable product validations when sourcing materials for high-profile projects.
ac 7018
Trustworthiness establishes its cornerstone through the consistent performance and the extensive user base that continually opts for the AC 7018. Many welding organizations and practitioners publish testimonial and case-study evidence online, underscoring the electrode’s consistent delivery on promises of performance. Manufacturers of the AC 7018 often highlight user feedback and third-party testing to substantiate claims regarding reliability, making it a trusted asset in any welder’s toolkit.
It's important to incorporate the AC 7018 within a broader understanding of welding operations. While it delivers robust outcomes, pairing it with appropriate amperage settings and understanding its behavior under specific conditions—like low ambient temperatures or humidity—can enhance its efficacy. Education in proper electrode storage is vital too, as its low-hydrogen construction requires a moisture-free environment to maintain optimal weld quality and safety.
To optimize the AC 7018’s potential, training sessions and professional development courses are recommended to familiarize users with best practices and innovative techniques tailored to this electrode. By investing in such continuous learning processes, welding professionals can elevate their craft, ensuring that the AC 7018 not only meets but exceeds operational expectations.
Ultimately, the AC 7018 electrode serves as a testament to the innovation and progress within the welding industry. Offering unparalleled quality, safety, and adaptability, it continues to empower welding professionals to bridge gaps, construct monumental infrastructure, and forge paths where dreams become tangible realities.