Understanding the true value of a 7018 welding rod, specifically the 3/32 size, can significantly impact the quality and durability of your welding projects. Today, we delve into the unique characteristics of this electrode, shedding light on its unparalleled advantages and practical applications.
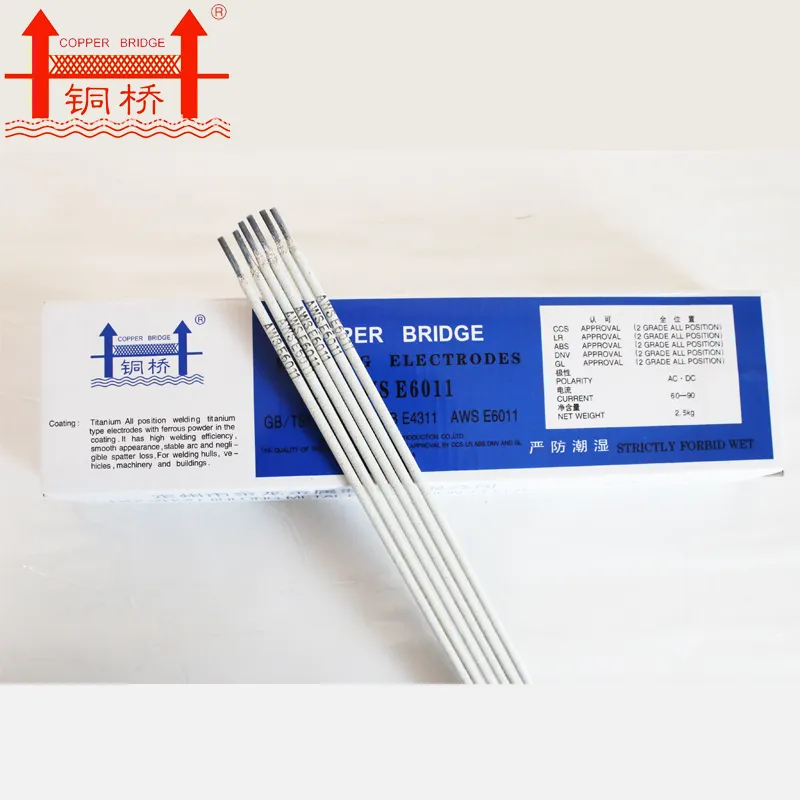
7018 welding rods are known for their low hydrogen content, which minimizes the risk of cracking and ensures a robust weld. The 7018 designation stands for the tensile strength (70,000 psi), the position versatility (all positions except vertical down), and the type of covering which is low hydrogen, potassium iron powder. Among these, the 3/32 inch diameter is particularly favored for its adaptability and precision in delicate or smaller scale welds.
Welders appreciate the 7018 rod for its smooth arc characteristics and clean weld deposits. It is an indispensable tool in structural steel welding, bridge construction, and pressure vessels. The flux coating of the rod contains iron powder, which aids in producing high-quality welds with superior mechanical properties. This is why the 7018 rod is often referred to as a low-hydrogen or hydrogen-controlled electrode, providing a significant safety net against cracking, a common challenge in high-strength steel welds.
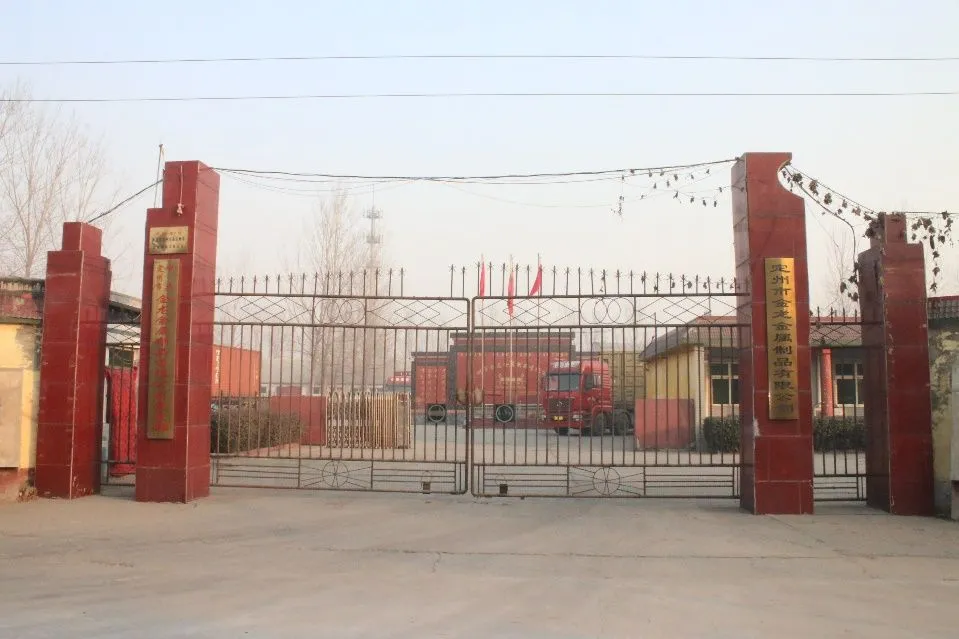
The consistency of the weld produced by a 7018 rod is a testament to its authority in the welding community. Using this electrode results in a weld bead that is aesthetically pleasing, with minimal spatter and easy slag removal. This user-friendly nature is due to the rod's efficient slag and flux composition, which also lessens post-weld cleanup—a notable advantage for projects demanding high efficiency and speed.
Nevertheless, mastering the 7018 welding rod requires a deep understanding of its unique properties and optimal usage conditions. Recognizing its moisture sensitivities is crucial for maintaining its integrity. Exposure to moisture can accumulate hydrogen in the weld, leading to embrittlement and potential weld failure. As such, proper storage in a rod oven or dry container is imperative for maintaining the electrode’s efficacy.
7018 welding rod 3 32
In practice, welding with a 7018 rod demands certain skills and techniques to maximize its benefits. Holding a steady hand and maintaining the correct arc length are essential for T-beads and fillet welds. For positions like overhead and vertical, a 3/32 rod offers finer control and less heat input, reducing burn-through risks on thinner metals. Furthermore, ensuring a slightly higher amperage than with other rods can improve penetration and fusion quality—key factors for a sound structure.
Choosing the right equipment and preparation can elevate the performance of the 7018 rod. For instance, AC or DC welding can be selected depending on the equipment available, with DC being generally more favorable due to its smoother arc. Furthermore, the joint preparation, such as ensuring clean surfaces and precise fit-ups, directly influences the welding quality.
With its reliable performance in critical structural applications, the 7018 welding rod stands as a benchmark for trustworthiness in industrial welding practice. It is often the rod of choice for certification tests due to its ability to create robust and high-caliber welds. Its reputation is backed by experienced welders worldwide who attest to its performance consistency and mechanical robustness.
In conclusion, whether you're constructing a skyscraper or working on a personal metalworking project, the 7018 3/32 welding rod offers superior performance, reliability, and versatility. Adequate understanding and handling of this tool can significantly enhance your work quality, ensuring safety, aesthetic value, and structural integrity. By adhering to best practices and respecting the electrode’s specifications, the 7018 rod remains a vital asset in any welder’s arsenal.