7018 welding rods, especially the 3/32-inch size, are considered staple tools for welding professionals and enthusiasts alike. These rods are renowned for their effectiveness in welding low to medium carbon steel and cast steel, providing superior quality joints that are both structurally sound and visually appealing. However, mastering the use of these electrodes requires understanding their unique characteristics and ideal usage scenarios.
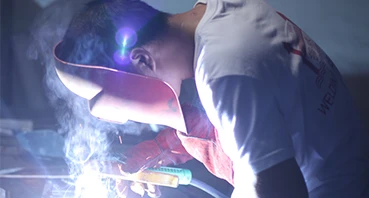
First and foremost, the 7018 welding rod is known for its low hydrogen content, which significantly reduces the risk of weld cracking due to hydrogen embrittlement. This makes it an ideal choice for critical applications where reliability and strength are paramount. The rod’s low-hydrogen coating contributes to a smoother arc and reduces post-weld cleaning requirements, enhancing productivity and achieving cleaner welds.
When it comes to the 3/32-inch size, this specific diameter offers advantages for precision work. Its smaller size allows for detailed welds on thinner materials, which is not achievable with larger rods. The 7018 3/32 rod can provide a neat weld bead with outstanding penetration, making it suitable for tasks like filing welds, small chassis repair work, or ornamental ironwork where aesthetics play a critical role.
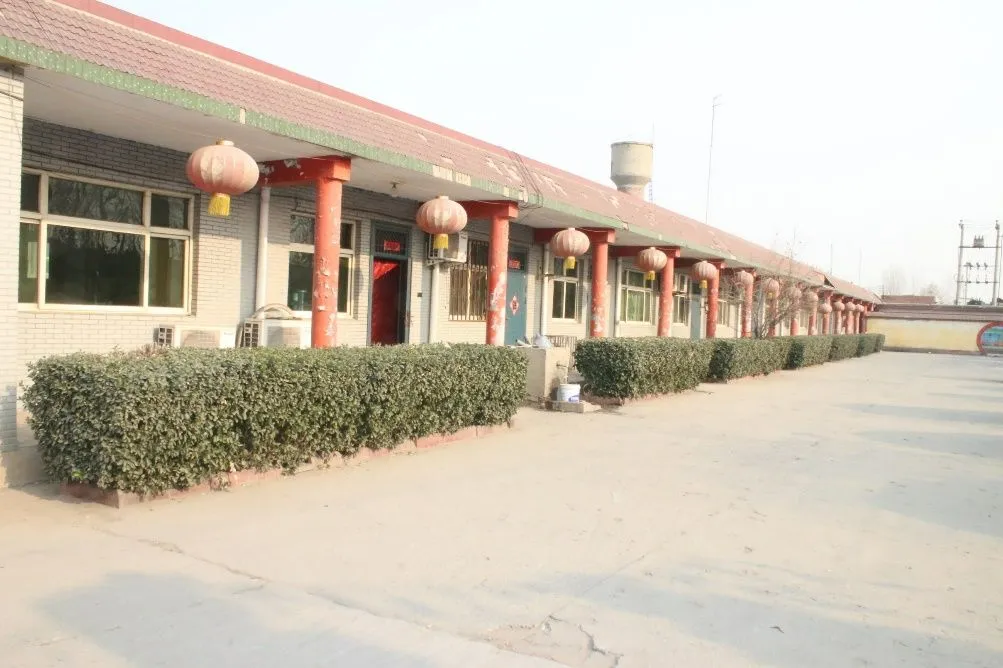
Expert welders often highlight the 7018 rod's versatility, as it supports both alternating current (AC) and direct current (DC) welding. However, preference is often given to DC for its stable arc characteristics and cleaner result. The rod's distinct ability to handle high amperage settings without sacrificing the weld quality also comes into play for larger projects that demand robust infrastructure, such as bridges and structural beams.
Using the 7018 3/32 welding rod efficiently requires understanding its superb out-of-position capabilities. While it performs exceptionally in flat and horizontal positions, experienced welders can also exploit its potential for vertical uphill and overhead welding. This versatility is especially advantageous for welding tasks that involve complex geometries or need scaffold-free work.
7018 welding rod 3/32
The storability of the 7018 rods poses a unique challenge due to their sensitivity to moisture absorption. Professionals and experts stress the importance of keeping these rods dry, often recommending sealed containers or dedicated rod ovens to maintain optimum performance. If moisture is absorbed, re-baking procedures can be utilized, but this involves precise temperature control to ensure the rod returns to a usable state without degrading its flux coating.
In terms of authoritativeness and expertise, workshop manuals and welding certifications often suggest the 7018 rod for numerous applications due to its compliance with stringent industry standards, making it a trusted tool in the hands of qualified welders. Training programs emphasize the rod's properties, encouraging knowledge transfer from seasoned professionals to apprentices, thereby maintaining high safety and quality standards in welding practices.
Ultimately, the success in using 7018 3/32 welding rods lies in the skill and knowledge of the welder. Trustworthiness in welding outcomes is often gauged by the welder’s proficiency in technique, power settings, and environmental conditions. Therefore, it’s crucial for welders to develop familiarity with their equipment and consistently practice, ensuring they bring out the full potential of these outstanding electrodes.
For those seeking the perfect balance between strength, versatility, and precision, the 7018 welding rod 3/32 inch remains a go-to tool. With the right approach and adequate experience, welders can achieve remarkable results, solidifying their work's integrity and aesthetic appeal. These welds are not just bonds between metals; they are the craft and dedication of skilled individuals who understand the intricate dance between power, material, and technique.