When seeking a robust solution in the realm of electrical components, understanding the significance of specifications like 7018 5 32 amps becomes essential. Considered an industry standard, this specification is often associated with welding rods—specifically the E7018 electrode, boasting considerable strength, reliability, and consistent performance necessary for various steel fabrication projects.
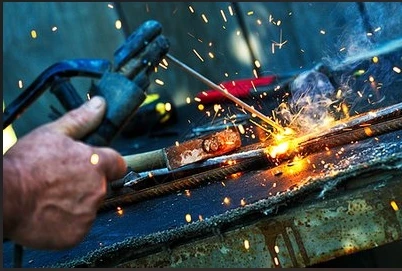
The E7018 electrode is famed amongst professionals for its low-hydrogen features, which make it ideal for welding high-strength materials. Offering exceptional mechanical properties, these electrodes are used to create secure bonds in critical welding applications. The numbers '7018' denote a tensile strength of 70,000 psi, where '1' indicates all-position welding capabilities and '8' signifies a low-hydrogen coating with iron powder, which accounts for high deposition efficiency.
A profound experience with E7018 electrodes begins with understanding its amperage requirements, specifically the mentioned 5 32 amps. When electrodes are referred to in the context of 5/32, it pertains to the diameter of the rod. This dimension is crucial because it affects the amp setting. For a 5/32-inch diameter E7018 electrode, a typical amperage range rests between 120-160 amps, depending on the specific material and project requirements. Adjusting this range can influence penetration and bead formation, making it vital for precise and effective welding outcomes.
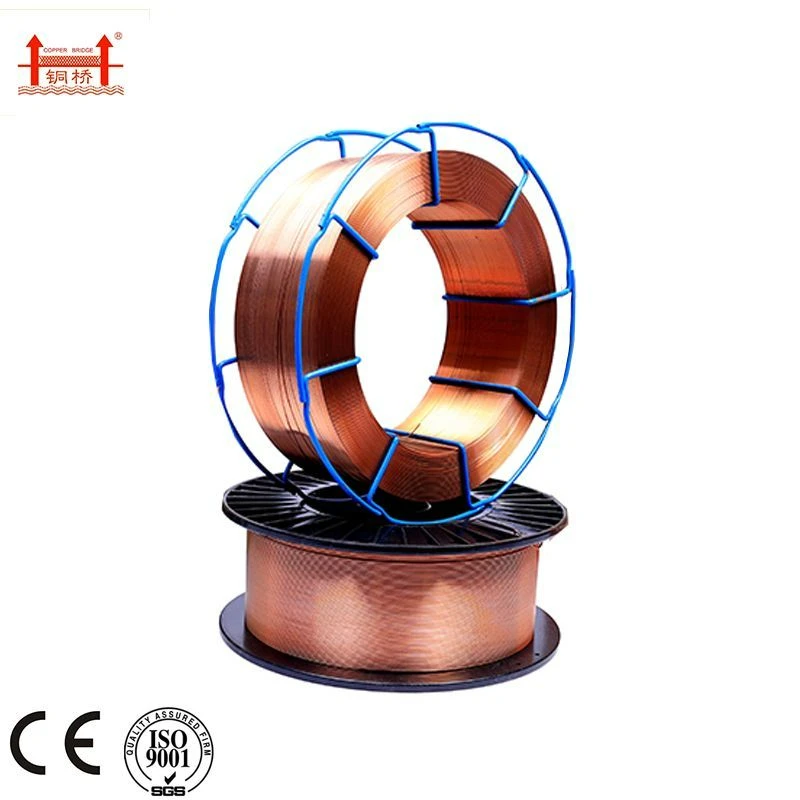
Professionals in the field advocate for versatility in these settings to align with the specific requirements of diverse projects. Emphasizing experience, users report that practicing on scrap materials before engaging in actual projects allows for a perfect dial-in of amperage settings, significantly increasing the quality of work. Adopting a trial and error approach with slight incremental adjustments to the amp settings ensures control over the arc stability and prevents issues such as excessive spatter or weak welds.
7018 5 32 amps
From an expertise standpoint, utilizing E7018 electrodes necessitates a clear understanding of the impact of ambient conditions on performance. Moisture absorption can compromise low-hydrogen benefits, thus, storage in a controlled, dry environment is pivotal. Exposing rods to high humidity leads to hydrogen entrapment in welded joints, risking structural integrity. Therefore, professionals ensure careful adherence to storage recommendations, sometimes opting for rod ovens to maintain optimal conditions.
In authoritative domains, guidelines stress the importance of the post-welding process, primarily the need for proper cooling practices. Rapid cooling can lead to cracks in high-strength steel, therefore, experienced welders apply controlled methodologies to moderate temperature declines. This process promotes structural soundness of the weld, embodying both strength and reliability in end applications.
Establishing trustworthiness in using E7018 rods at 5/32 amps emerges from consistently following best practices. Community networks and professional forums serve as valuable sources of insights, where shared experiences highlight practical challenges and solutions, reinforcing confidence among welders. Prominent amongst these is the feedback loop from projects, which plays a crucial role in honing techniques and ensuring the long-term reliability of welds crafted with precision.
In summation, working with the 7018 5 32 amps specification embodies a synthesis of knowledge, skilled execution, and adherence to rigorous practices. By integrating these elements, professionals achieve results that fulfill demanding industrial standards. Through vibrant exchange of experiential insights and continuous learning, welders worldwide position this specification as a cornerstone in the art and science of welding.