Understanding the intricacies of using products like the 7018 1 electrode is crucial for individuals and businesses aiming to optimize welding projects. The 7018 1 electrode is renowned in the welding industry for its superior strength and precise welding capabilities, making it a staple for projects requiring robust structural integrity.
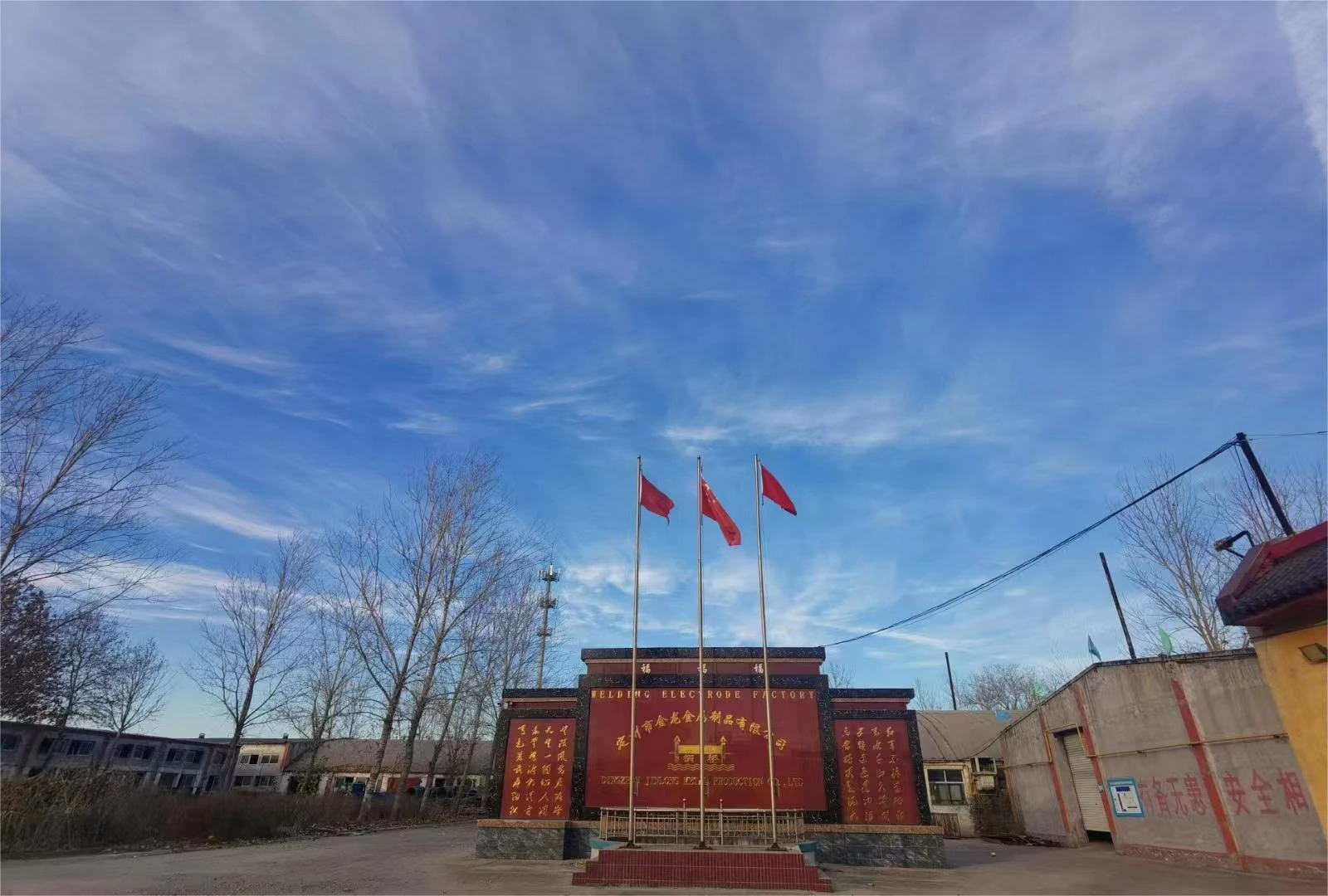
The 7018 1 electrode, a low-hydrogen, potassium-coated electrode, stands out for its ability to produce smooth, flawless welds in demanding environments. Its formulation limits hydrogen content, thereby minimizing the risk of hydrogen-induced cracking—a significant concern in the welding world. The versatility and reliability of this electrode make it indispensable for industries such as construction, shipbuilding, and pipe welding.
Users with extensive experience highlight the electrode's ease of use, particularly noting its arc stability and ease of striking and re-striking. Welders with varied levels of expertise find it user-friendly, attributing this to the electrode’s balanced chemistry, which facilitates easy control and manipulation. For tasks involving thicker sections and high-stress applications, the 7018 1 electrode is a preferred choice, ensuring the welded joint sustains high strength and significant ductility.
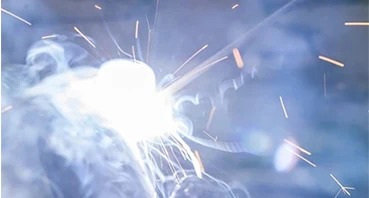
Moreover, professionals recognize the electrode's adaptability across different welding positions, including flat, horizontal, vertical, and overhead. This flexibility makes it suitable for diverse applications, from fabricating high-pressure pipelines to constructing critical load-bearing structures. Welders frequently attest to its reliability, citing successful project outcomes in both controlled industrial settings and challenging outdoor environments.
Authoritative institutions and industry standards often endorse the 7018 1 electrode, underscoring its compliance with stringent quality and safety regulations. For instance, certifications from prominent welding societies guarantee that the electrode meets or exceeds necessary mechanical and chemical properties for high-performance welding.
7018 1 electrode
However, to maximize the performance of the 7018 1 electrode, proper storage and handling are paramount. This low-hydrogen electrode is sensitive to moisture, which can affect its performance by increasing its susceptibility to cracking. Experts recommend storing the electrodes in a dry, controlled environment and using an electrode oven to maintain optimal dryness before use.
Furthermore, trustworthiness in outcomes using the 7018 1 electrode can be assured by adhering to the correct welding parameters. This involves maintaining appropriate amperage, voltage, and travel speed. Deviations might compromise weld quality,
leading to defects. Thus, understanding machine settings and calibrations, based on the specific electrode and application, is vital for achieving optimal welds.
In terms of cost-efficiency, the 7018 1 electrode is affordable while delivering high-quality results. Its longevity in the welding market attests to its durability and performance, making it a cost-effective choice for professional welders and businesses alike. Incorporating this electrode into a welding workflow can result in reduced downtime, increased productivity, and significant long-term savings.
For newcomers or professionals seeking to enhance their expertise, training is available through accredited programs and workshops. These platforms offer insights into advanced welding techniques using the 7018 1 electrode, based on collective industry experiences and technological advancements, thereby strengthening user competence and confidence.
In conclusion, the 7018 1 electrode embodies a blend of innovation, reliability, and efficiency. It has carved its niche in the industry by consistently meeting the demands of challenging welding applications. Professionals lauding its benefits do so based on proven experience, knowledge gained over years, and alignment with industry standards. Whether for structural work, high-pressure systems, or intricate fabrications, the 7018 1 electrode remains a trusted tool in the welder's arsenal, assuring quality and safety in every finished weld.