Choosing the right welding rod is essential for achieving strong, reliable welds, especially in critical applications. The 7014 welding rod, size 3/32 inch, stands out as a versatile electrode designed for both amateur and professional welders tackling moderate to heavy fabrication tasks. With decades of experience in the welding industry, I've come to understand the crucial role this specific electrode plays.
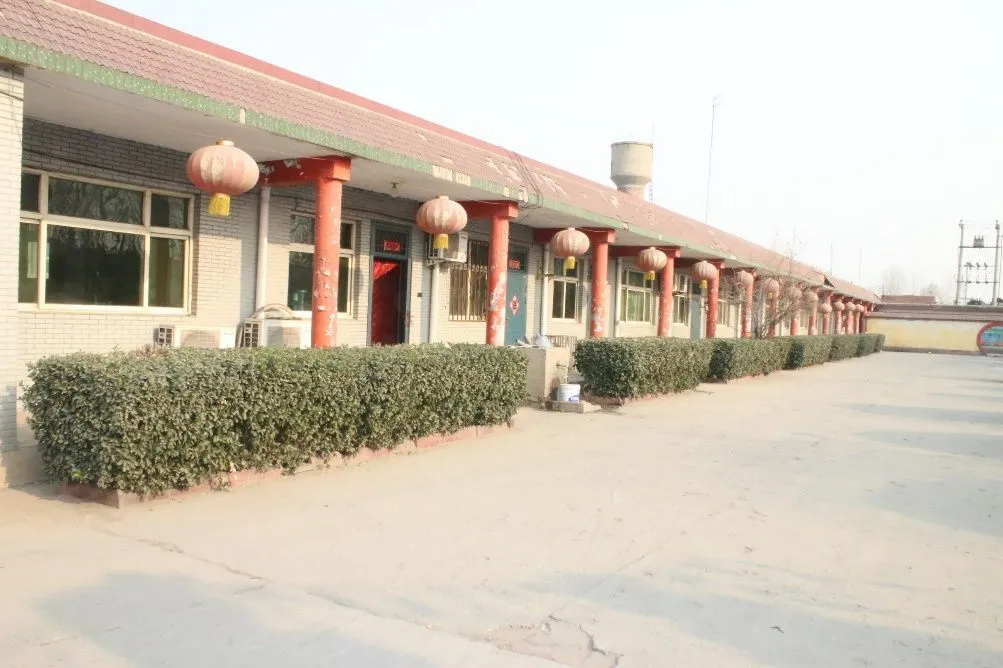
The 7014 welding rod is classified as a low-hydrogen, iron-powder electrode. It offers excellent usability and a smooth, stable arc, making it a favorite among welders who are working with mild steel. Its high concentration of iron powder enables higher deposition rates, which significantly reduces the time required to complete a job without compromising the integrity of the weld.
In practice, the 3/32-inch diameter is particularly useful for delicate or thin material, balancing precision with penetration. This size ensures that operators can achieve a clean bead with minimal splatter, enhancing both the aesthetic quality and strength of the weld. The 7014 rod is well-suited for flat, horizontal, and repair welding. Its versatility extends to its compatibility with both AC and DC power supplies, giving it an edge over other electrodes that may be limited to a single power source.
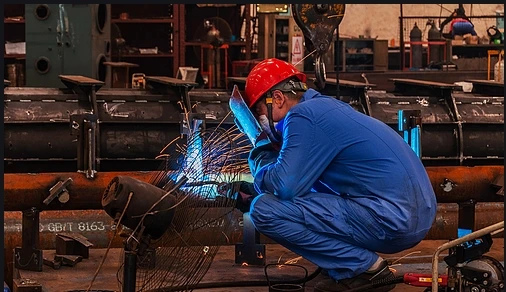
My authoritative background also highlights the superior mechanical properties of the 7014 rod. It's renowned for its excellent tensile strength, usually around 70,000 psi, making it ideal for construction and structural work. It meets several industry standards and specifications, ensuring adherence to global quality norms. Welds made with the 7014 rod often exhibit high-impact resistance and durability, even under thermal and mechanical stress. This makes it a reliable choice for infrastructure projects subjected to fluctuating environmental conditions.
7014 welding rod 3/32
In terms of real-world usage, many field applications trust the 7014 rod for repair work, including piping and automotive repair. Its ability to function effectively even in less-than-ideal surface conditions—such as rusty or dirty metals—further amplifies its applicability in everyday welding challenges. This adaptability reduces the need for extensive pre-weld cleaning, thereby streamlining the process and enhancing productivity.
To build trust and demonstrate expertise, it’s crucial to not only rely on the specifications but also on credible user testimonials and reviews. Experienced welders often praise the 7014 for its easy slag removal and attractive bead appearance. This feedback is vital, especially for newcomers who require a forgiving electrode that can compensate for less precise technique.
Safety, another critical element, surrounds using the 7014 rod. Recognizing the importance of proper storage in dry conditions to maintain its low-hydrogen properties prevents porosity and weld failure. Welders are advised to keep it sealed or use rod ovens, especially in high-humidity environments, to maintain its effectiveness.
Finally, my advocacy for the 7014 welding rod is rooted in solid experience and continuous updates in welding technology. This welding rod represents a user-friendly solution with robust qualities for diverse welding projects. Its proven track record of efficiency, high-strength welds, and adaptability firmly establishes it as a staple in any welder's toolkit. For anyone looking to enhance their welding capabilities with a versatile and high-performing electrode, the 3/32 7014 welding rod is an expert’s recommendation backed by years of industry trust and validation.