When it comes to selecting the right equipment for welding tasks, particularly for specific materials and projects, the choice of welding rods becomes crucial.
The 6013 welding rod, especially in the size of 3/32 inches, is often highlighted for its versatility and ease of use. Understanding how to optimize its performance, particularly in terms of amperage, can significantly impact the quality of your welding work.
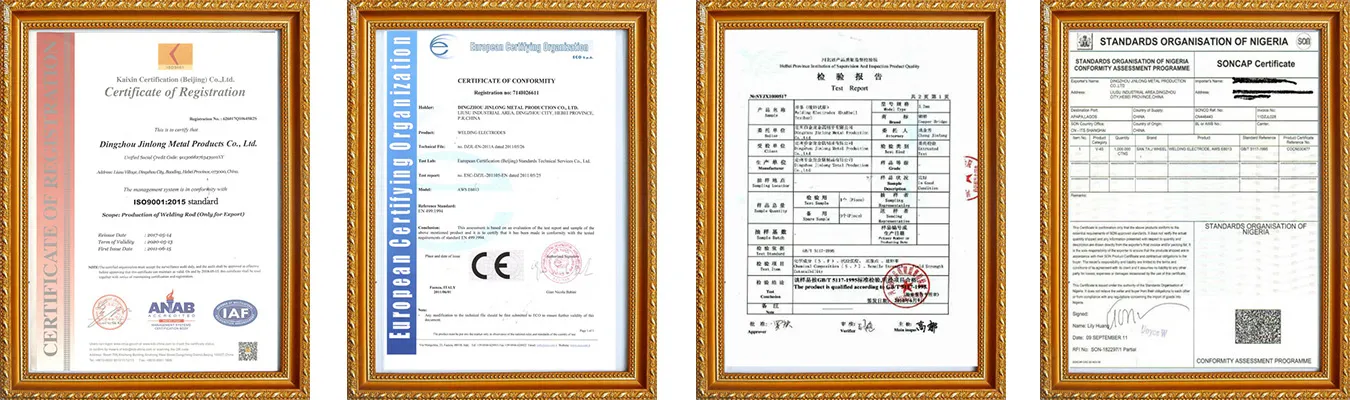
Experienced welders appreciate the 6013 welding rod for its impressive arc stability and smoothness in welding. This rod is ideal for beginners as well as seasoned welders who seek precision without compromising on the aesthetics of the finished product. The 6013 rod is suitable for light to medium industrial work, making it a popular choice in various sectors, from automotive repairs to artful metalwork.
From a professional standpoint, the amperage setting plays a pivotal role in the performance of the 6013 rod, particularly when using a 3/32 inch diameter. The optimal amperage range for this size typically falls between 40 to 90 amps. However, many experts recommend a sweet spot around 75 amps for most applications as this setting balances penetration and bead appearance. Lower amperage could lead to inconsistent welds and insufficient penetration, making the seam weaker and less durable.
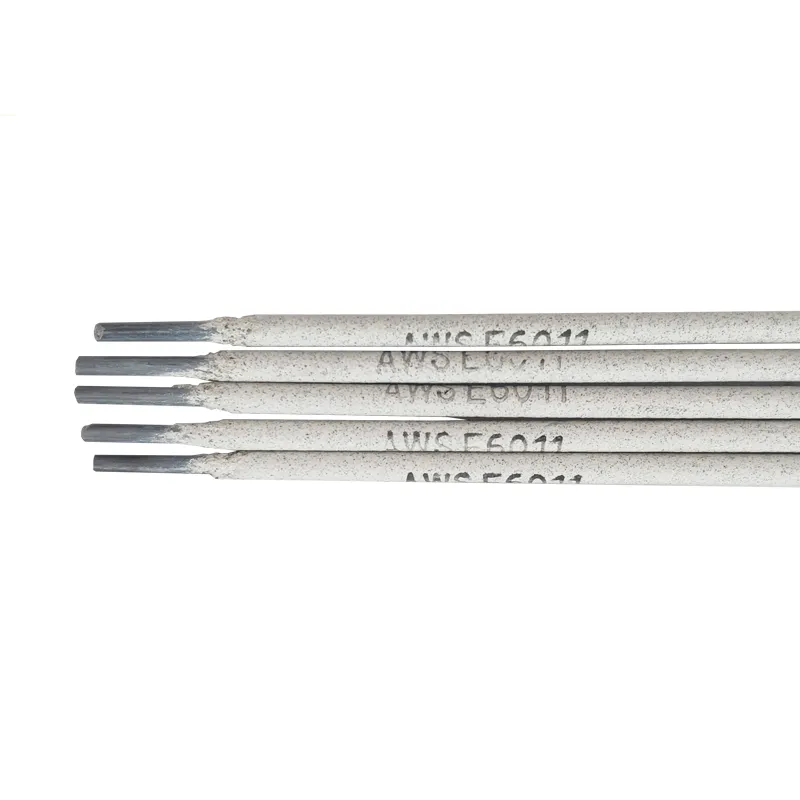
Welders with significant experience argue that the material thickness being welded must also be considered when selecting the appropriate amps. For thinner materials, an amperage setting on the lower end of the spectrum is advisable to prevent burn-through. Conversely, thicker materials may require higher amperage to ensure thorough penetration and fusion of the materials. Herein lies the importance of not just relying on standard settings but adjusting parameters based on the project's specific needs.
6013 welding rod 3 32 amps
Furthermore, the 6013 welding rod is known for its ability to produce slag that is easy to remove, resulting in clean welds that require minimal post-weld cleaning. This rod's composition is predominantly mild steel coated with a high titanium-potassium flux, contributing to its stable arc characteristics and ease of striking the arc. The coating also facilitates smoother welds that possess a visually appealing finish – a critical feature for projects where aesthetics are as important as function.
Trustworthiness in the use of the 6013 rod is often demonstrated through consistent outcomes across various projects. Many authoritative voices in the welding community suggest that the 6013 rod's ability to function effectively on both AC and DC power sources adds a layer of flexibility uncommon in many rods. This dual compatibility broadens its applicability across different welding machines, enhancing the user's overall work tempo and project efficiency.
Authoritative guides on welding consistently point out the importance of electrode storage in maintaining the performance of the 6013 welding rod. Improper storage can lead to moisture absorption, potentially causing porosity in welds. Storing these rods in a dry, temperature-controlled environment ensures that they remain in optimal condition, reducing the risk of flaws that could compromise the structural integrity of the weld.
In conclusion, leveraging the full potential of the 6013 welding rod in a 3/32 inch size revolves around understanding its inherent properties, adjusting amperage settings to fit the demands of specific tasks, and maintaining proper storage conditions. Through expert handling, this welding rod not only meets the fundamental needs of welding tasks but consistently delivers high-quality results, cementing its place as a reliable tool in any welder's arsenal. The amalgamation of experience, professional knowledge, and adherence to best practices ensures that users achieve successful outcomes time and time again.