6013 welding electrodes represent a vital component in the arsenal of any professional welder, known for their versatility and ease of use. These electrodes, also referred to as mild steel electrodes, are particularly well-suited for a variety of welding applications. The following is a comprehensive examination of 6013 welding electrodes, spotlighting their unique specifications, advantages, and best-use scenarios, grounded in industry expertise and real-world experience.
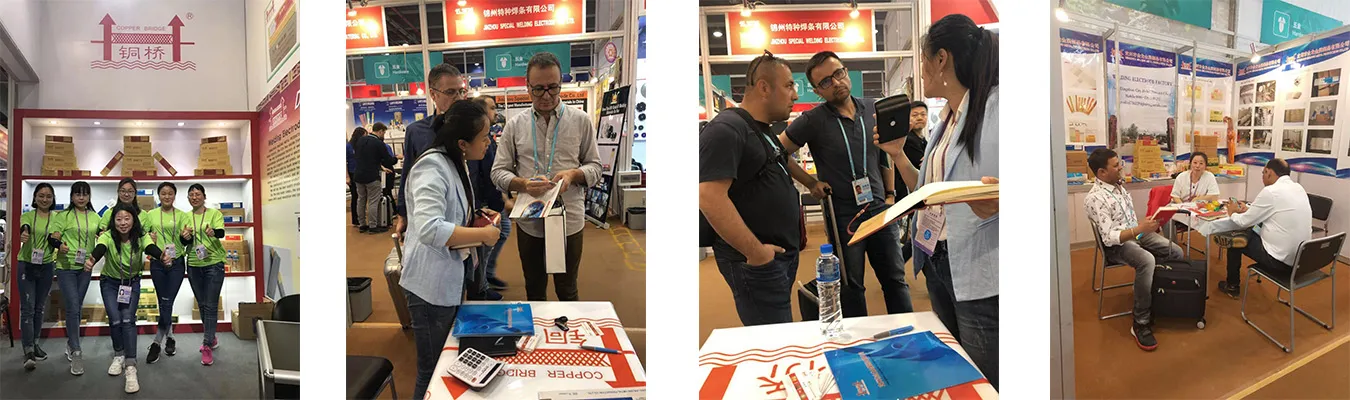
One of the standout features of 6013 welding electrodes is their adaptability to various welding positions. Whether working horizontally, vertically, or even overhead, these electrodes deliver consistent quality. Their low penetration capabilities make them especially effective for thin metal sheets, preventing burn-through while ensuring strong, clean welds.
In terms of expertise, the chemical composition of 6013 electrodes provides a distinct advantage. The electrodes are coated with a high-titanium potassium coating, which facilitates the formation of a stable arc. This characteristic is invaluable for welders who prioritize precision and aesthetics since the slag created by the welding process peels off easily, leaving behind a smooth finish that often requires minimal post-weld cleaning.
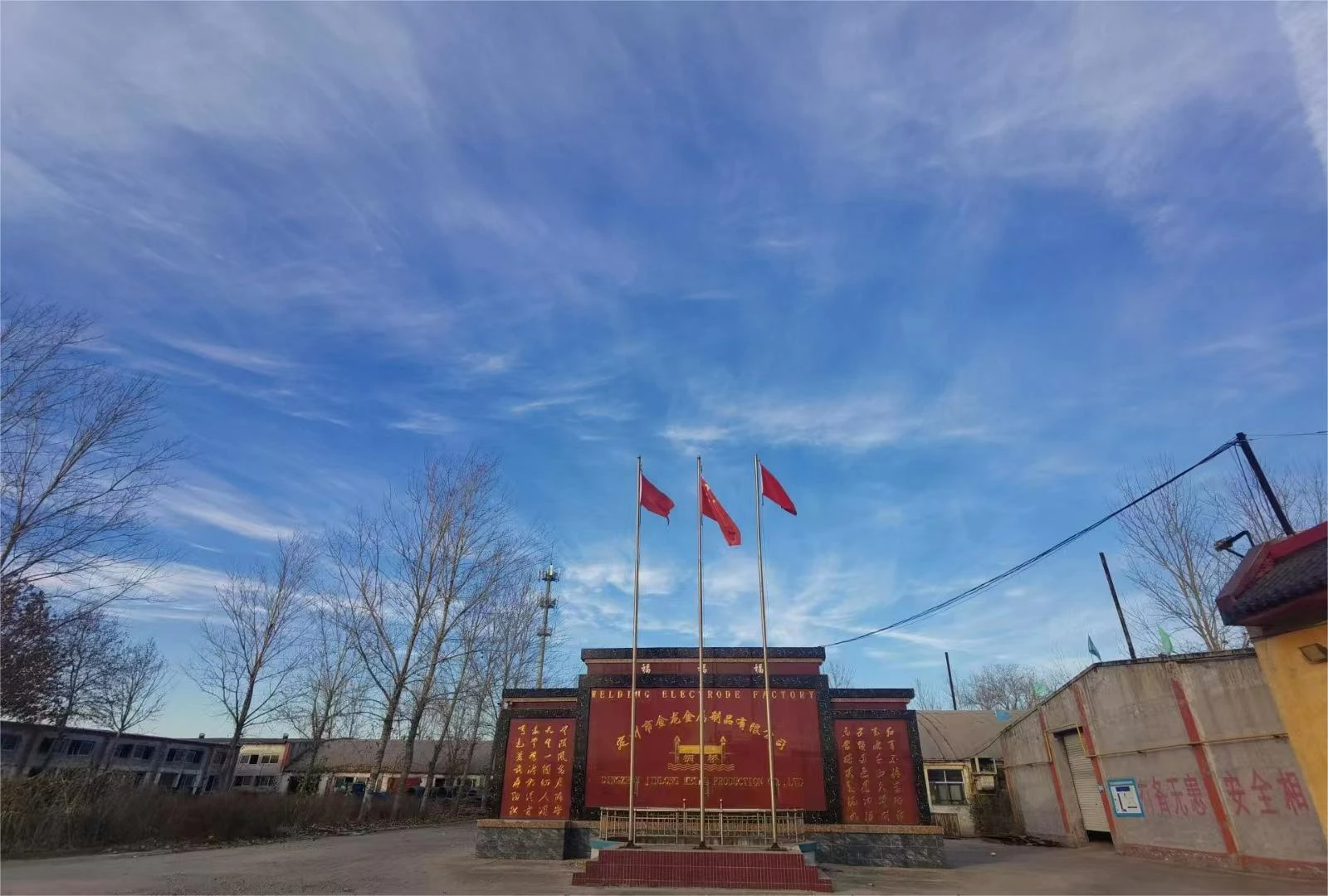
From an authority perspective, 6013 welding electrodes have been thoroughly tested and validated by welding professionals worldwide. Many educational institutions use them in training programs due to their user-friendly nature. Their ability to function optimally at a wide amperage range makes them a suitable choice for many welding machines and power sources, ensuring that they remain a staple in both industrial and smaller workshop settings.
6013 welding electrodes
Furthermore, trustworthiness in welding applications is paramount,
and 6013 electrodes do not disappoint. Their reliability is proven in both amateur and professional environments, being forgiving on less-than-pristine metal surfaces while yielding reliable welds. This resilience is particularly noted when dealing with rusty or painted metals, where other electrodes might falter.
Apart from their performance, the economic consideration of 6013 welding electrodes plays a crucial role for businesses looking to maximize their resources. The affordability, combined with their high deposition rates, ensures they remain a cost-effective choice without compromising on quality—a critical factor for operations looking to balance budgets while maintaining high operational standards.
Drawing from real-world experience, many seasoned welders recommend using 6013 electrodes in scenarios requiring high-speed, aesthetically pleasing welds on thin-walled materials. Their ability to perform exceptionally well in low-voltage settings further enhances their usability in varied electrical conditions, a testament to their robust design and manufacturing integrity.
In summary, 6013 welding electrodes embody a blend of versatility, reliability, and accessibility, making them indispensable for welders seeking superior performance and efficiency. Their consistent delivery of quality welds across diverse environments underscores their standing in the industry. For anyone involved in metal fabrication, understanding and utilizing 6013 welding electrodes can not only enhance the quality of the end product but also streamline the welding process itself, reaffirming their place as a trusted tool in the welding industry.